Galvanized rubber expansion joints are pivotal in numerous industrial applications, offering both flexibility and resilience where pipework systems encounter temperature fluctuations, vibrations, and misalignments. Recognizing the unmatched utility of these components requires an appreciation of their unique construction and the expertise involved in their application.
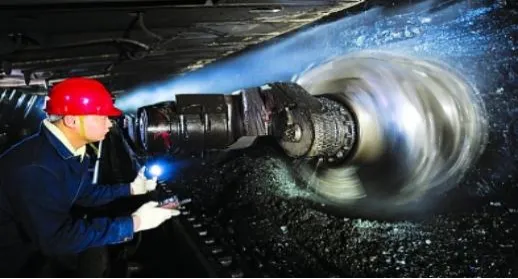
At their core, galvanized rubber expansion joints consist of a robust rubber body reinforced with a galvanized coating, designed to withstand corrosive environments while managing stress within the piping systems.
The integration of galvanized steel provides another layer of defense, tackling erosion due to humidity or chemical exposure. This dual-material construction ensures a balanced blend of flexibility and durability, making these joints indispensable in sectors ranging from wastewater management to petrochemicals.
Experience in implementing galvanized rubber expansion joints reveals their capacity to significantly extend the service life of piping systems. In environments where thermal expansion and contraction are frequent, the flexibility provided by rubber expansion joints prevents possible fractures or leaks. For instance, in heating, ventilation, and air conditioning (HVAC) systems, these joints compensate for movement and mitigate sound transmission, ensuring smooth and silent operation. Plant engineers who have experienced chronic issues with rigid connections often find a shift to galvanized rubber expansion joints brings newfound dependability.
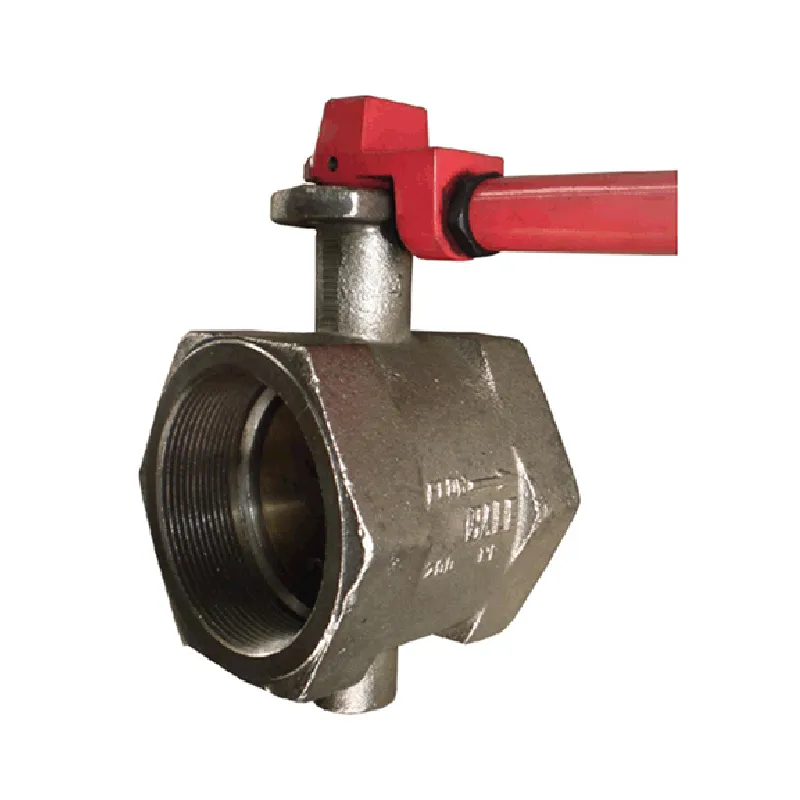
Professionals with expertise in this field continuously advocate for incorporating these joints due to their ease of installation and maintenance. Compared to traditional all-metal expansion joints, rubber alternatives with a galvanized exterior offer simpler handling without compromising performance. The preemptive nature of this solution often translates into cost savings in maintenance and operational downtime. Key installations at chemical plants have shown a marked decrease in unscheduled shutdowns thanks to the preventive capacities of these joints, emphasizing their imperative role in industrial efficiency.
galvanized rubber expansion joint
Institutional testimonials from authorities in construction engineering often underscore the authoritative stance that galvanized rubber expansion joints hold in infrastructure resilience. Evolving from academic research to practical applications, numerous case studies reinforce the efficacy of these joints in high-demand situations. Organizations that follow stringent quality standards, such as American Society of Mechanical Engineers (ASME), often illustrate their trustworthiness through certifications and stringent testing procedures. This provides end-users with unwavering assurance regarding product performance and longevity.
Moreover, the trustworthiness of manufacturers producing these joints further solidifies their assertive presence in the market. Reputable manufacturers invest in research and development to push the boundaries of material science, ensuring that their galvanization processes meet the highest industry standards. This commitment to quality manifests in extensive warranties and customer support, forming a backbone for consumer confidence.
The encapsulated utility of galvanized rubber expansion joints extends beyond traditional applications. As industries face increasingly complex compliance requirements, these joints provide an adaptable and eco-friendly option, aligning with green engineering principles due to their longevity and reduced replacement frequency. An industry increasingly focused on sustainable development sees the reduced environmental footprint from minimized waste and resource usage as invaluable.
In summary, the experience, expertise, authoritativeness, and trustworthiness surrounding galvanized rubber expansion joints highlight them as a cornerstone in modern piping solutions. Their multi-faceted advantages—from mechanical performance to economic efficiency—cement their role in ensuring industrial infrastructures remain robust and reliable amidst evolving technical demands.