Flow control check valves are essential components in various industrial applications, serving as pivotal elements to regulate the flow of liquids and gases. These devices ensure that the flow of substances occurs in a single direction, preventing backflow and potential damage to the system. Implementing the right flow control check valve requires a deep understanding of its mechanisms, functions, and the specific needs of the industry.
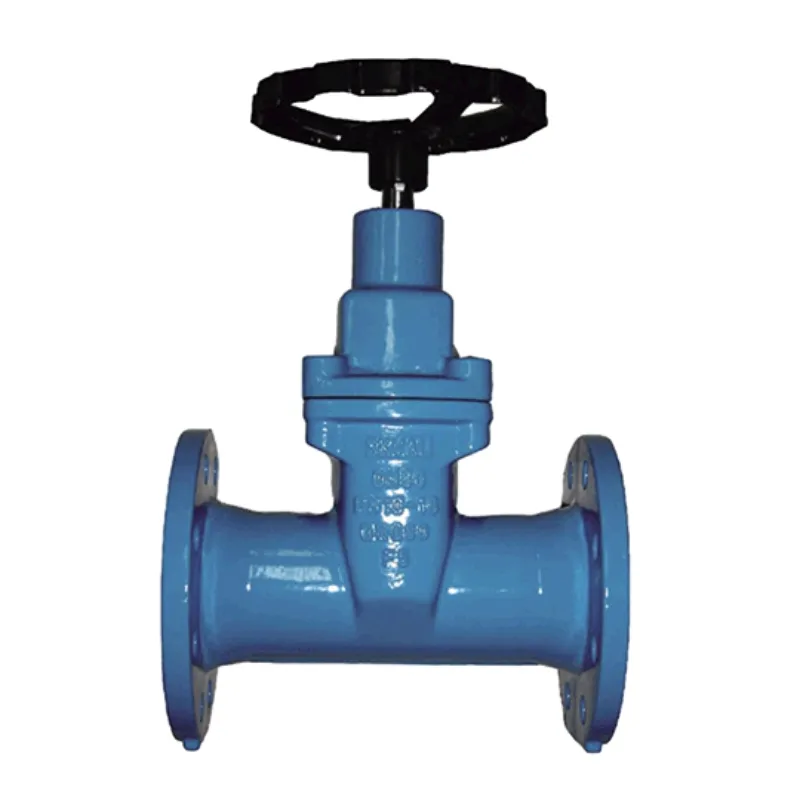
Industries across the spectrum—ranging from oil and gas to water treatment facilities—rely on flow control check valves to maintain efficient and safe operations. In oil and gas pipelines, for example, these valves prevent reverse flow, which could otherwise lead to catastrophic failures. Similarly, water treatment plants depend on them to maintain a consistent flow rate, crucial for both efficiency and safety.
Choosing the right type of flow control check valve involves considering various factors such as the fluid type, pressure, temperature, and the specific application requirements. There are different types of check valves, including swing check valves, lift check valves, and ball check valves. Each type has its unique benefits and is designed for particular applications. For instance, swing check valves are generally used in situations where low fluid resistance is crucial, whereas lift check valves are suitable for high-pressure systems.
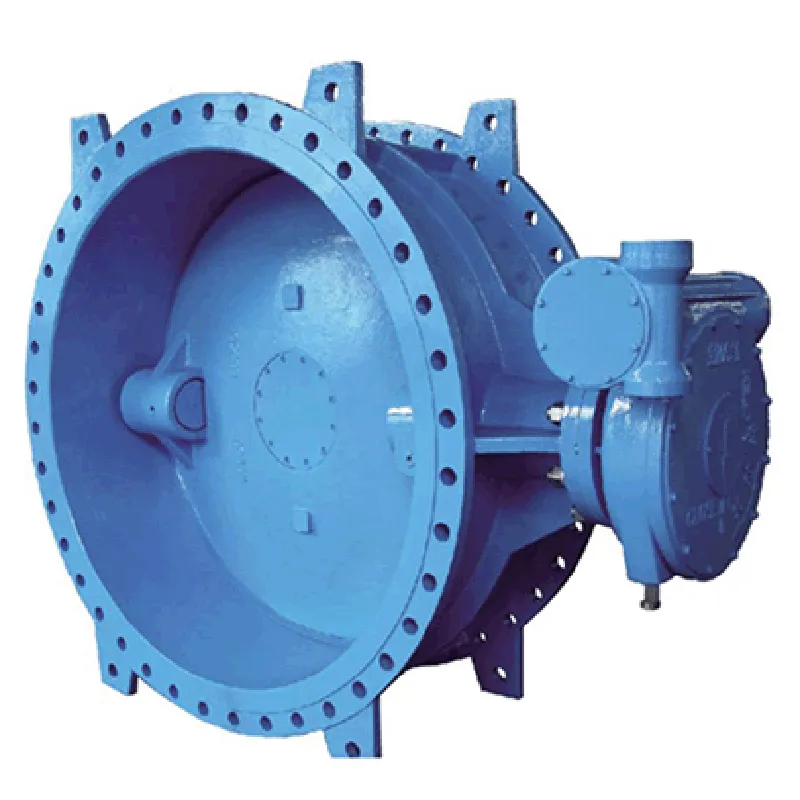
The material used in constructing the valve is another critical consideration. Check valves must be durable and resistant to the specific external conditions they will face. Stainless steel, for instance, is often favored for its corrosion-resistant properties, making it ideal for harsh environments. Others may opt for plastic valves in systems where chemical compatibility is crucial.
Real-world experience has highlighted the need for reliable and efficient valve operation. For instance, an engineer at a chemical manufacturing plant noticed frequent issues with backflow, which led to production downtimes. By upgrading to a more robust flow control check valve, the plant not only eliminated the backflow issues but also improved overall process efficiency and reduced maintenance costs.
flow control check valve
Manufacturers of flow control check valves constantly innovate, ensuring these components meet the rigorous standards of modern industry. By leveraging advanced materials and cutting-edge technology, they produce valves that offer increased longevity, reliability, and efficiency. For instance, some manufacturers incorporate smart technology features that allow for real-time monitoring and automated adjustments to the flow conditions, optimizing performance and minimizing the risk of failure.
Trust in a valve's performance is paramount as industries cannot afford unexpected downtimes or safety risks. Valves should meet international standards and undergo rigorous testing to ensure they perform under expected conditions. Working with a reputable manufacturer that provides warranties and comprehensive after-sales support further enhances the trustworthiness of these vital components.
Expertise in selecting and maintaining flow control check valves is also critical. Professionals in this field must be well-versed in the latest industry standards and technologies to offer the best solutions tailored to different industrial needs. Continuous training and staying abreast of technological advancements ensure that these experts can provide informed recommendations and professional maintenance services.
In conclusion, flow control check valves are integral to the efficient and safe operation of numerous industrial systems. Understanding their applications, selecting the appropriate type and material, and keeping up with innovations in the field constitute best practices. Industries must continue to prioritize expertise and trustworthiness when selecting these components to ensure operational efficiency and safety. As technology evolves, so too must the approach to implementing and managing these critical systems.