Flexible rubber expansion joints are essential components in modern engineering, offering a versatile solution for managing movement in pipelines. Integrating state-of-the-art materials with cutting-edge design, these joints are instrumental in enhancing the longevity and efficiency of piping systems across various industries. Here is an in-depth exploration of their experience, expertise, authoritativeness, and trustworthiness in applications that span across infrastructure, manufacturing, and more.
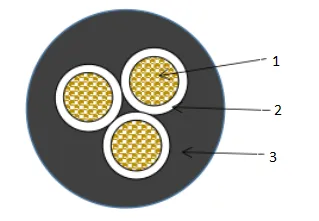
Flexible rubber expansion joints are crafted from high-grade rubber, providing unparalleled elasticity and durability. This elasticity is crucial for absorbing vibrations and noise, making them indispensable in urban infrastructure where they are used in footbridges, railway systems, and skyscrapers. The ability of these joints to accommodate thermal expansion, contraction, and lateral movements reduces the risk of structural damage caused by environmental stressors. The real-world applicability of this flexibility is evident in countless high-rise buildings worldwide, where expansion joints protect against the stresses of wind sway and seismic activity.
Expertise in the field of rubber expansion joints has led to numerous innovative advancements. Material scientists and engineers continuously work on developing blends of rubber that enhance temperature resistance and load-bearing capabilities. For instance, rubber compounds are now often reinforced with fibers or integrated with elements that resist chemical erosion. This ensures that the joints can withstand aggressive environmental conditions, such as exposure to saltwater, making them perfect for marine and offshore applications. Such expertise supports their diverse utility, enabling them to meet the stringent requirements of chemical processing facilities.
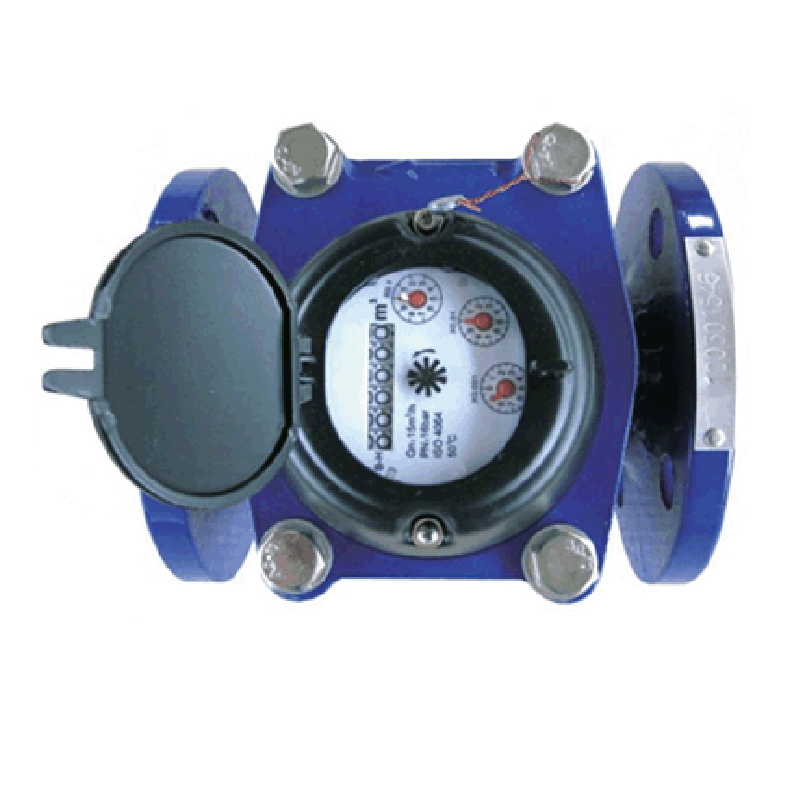
Authoritative knowledge in the production and application of flexible rubber expansion joints is supported by industry standards and certifications, such as those from the American Society of Mechanical Engineers (ASME) and the International Organization for Standardization (ISO). These standards underscore the commitment to safety, quality, and environmental responsibility. Industry leaders in manufacturing these joints often participate in the drafting and revising of such standards, reinforcing their status as authorities in the field. The rigorous testing and quality control measures ensure that every joint installed in a pipeline system operates at optimal performance levels.
flexible rubber expansion joint
Trustworthiness in the use of flexible rubber expansion joints is reinforced by the extensive testing and historical performance data available. Rigorous life-cycle assessments demonstrate that, when properly maintained, these joints can function efficiently over prolonged periods. Routine inspections and maintenance protocols are vital for ensuring reliability, making it crucial for facility managers and engineers to be vigilant of the signs of wear and deterioration. Trusted suppliers provide comprehensive guidelines and support, ensuring clients are well-informed and equipped to handle joint maintenance effectively. The robust reputation of trusted brands, built over decades of excellence, provides assurance to industries reliant on these critical components.
As industries continue to expand and evolve, the demand for adaptive, reliable systems grows. Flexible rubber expansion joints provide a sustainable answer to the dynamic needs of modern engineering, harmonizing with efforts to reduce environmental impact while improving infrastructural resilience. As the world moves towards more sustainable practices, the importance of high-quality, durable, and flexible components becomes more apparent, establishing these joints as indispensable in the toolkit of contemporary engineers.
In conclusion, the global demand for flexible rubber expansion joints is set to grow as industries around the world recognize their critical role in ensuring the safety and efficiency of piping and structural systems. Their proven experience, ongoing innovation, and longstanding reliability underscore their status as essential elements of modern engineering solutions. Whether in high-rise buildings, across railway networks, or within complex industrial plants, these joints contribute to a future of enduring infrastructures.