As someone who's spent over a decade delving into the intricacies of various mechanical systems, I have found flap check valves to be indispensable in many industrial applications. These unsung heroes sit quietly within fluid systems, ensuring the seamless flow of liquids and preventing the backflow that can cause significant disruptions or even damage. Understanding their design and functionality is crucial for anyone involved in system design, maintenance, or engineering.
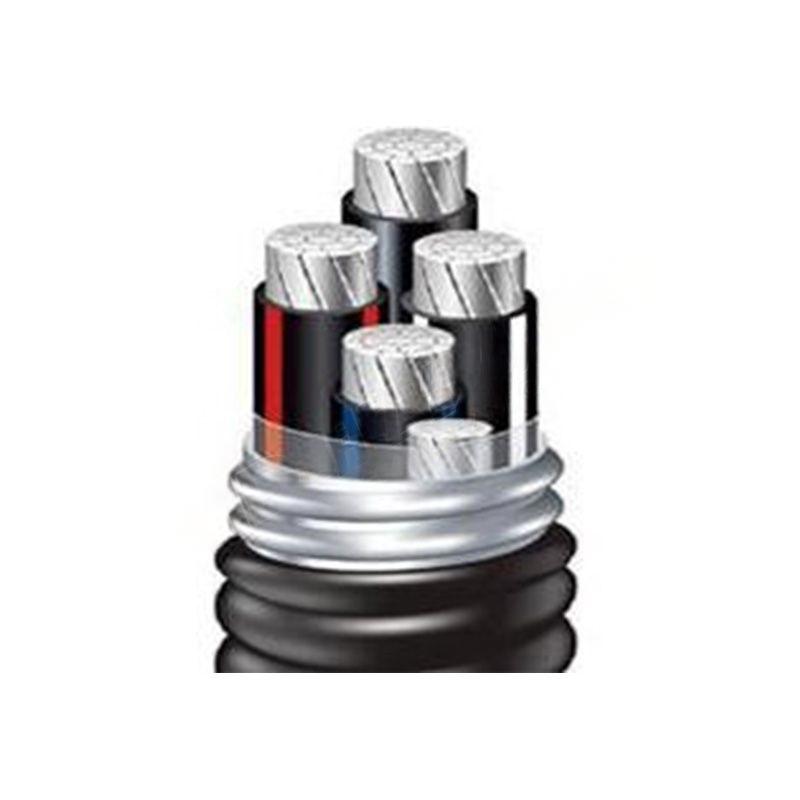
A flap check valve is a type of non-return valve, which allows fluid to flow in one direction while preventing it from going the opposite way. This characteristic is vital in systems where maintaining a unidirectional flow is essential, such as in water treatment facilities, plumbing systems, and certain chemical processing setups. These valves are engineered to handle various pressures and fluid types, making them versatile components in complex fluid dynamics systems.
One of the cornerstone experiences in using flap check valves is their reliability. In my career, I've seen many systems that have been operating smoothly for years, with minimal maintenance, due to the robustness of these valves. Typically constructed from durable materials like stainless steel, brass, or PVC, they can withstand the rigors of demanding environments, including exposure to corrosive substances or extreme temperatures. This durability is a testament to their engineering precision and the careful selection of materials, ensuring a long service lifespan with reduced downtime.
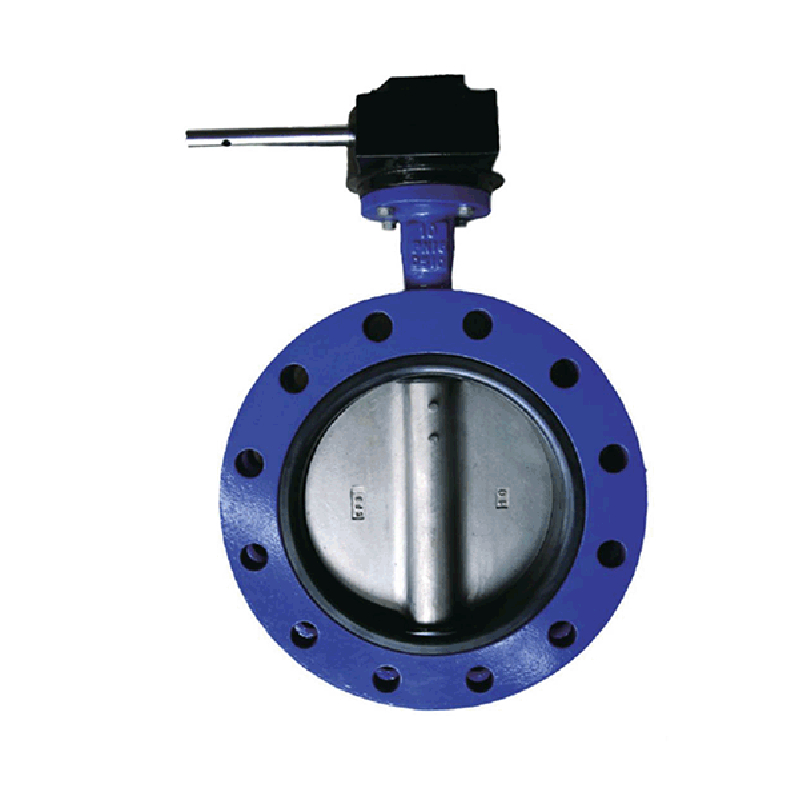
From an expertise standpoint, installing and maintaining these valves requires an understanding of their internal mechanisms and operational parameters.
The flap, often a disc or a flat panel, is connected to a hinge or pivot within the valve body. When fluid flows in the intended direction, it pushes the flap open, allowing passage. Conversely, any attempt at backflow results in the flap sealing shut, effectively preventing reverse movement. This simple yet effective mechanism is crucial for maintaining efficiency and safety in many systems.
flap check valve
Moreover, selecting the right flap check valve involves understanding the specific needs of your system. Factors like fluid type, flow rate, pressure, and temperature all influence the ideal valve choice. For instance, systems requiring frequent opening and closing might benefit from a valve with a soft sealing mechanism to reduce wear, while high-pressure applications might necessitate a valve with a reinforced flap and body to withstand the forces involved. Working with a knowledgeable supplier or engineer can ensure that the right valve is chosen, providing years of reliable service.
The authoritativeness of flap check valves in industry is undisputed, given their widespread adoption and critical role in system safety and efficiency. Industry standards and certifications, such as those from the American Society of Mechanical Engineers (ASME) or the International Organization for Standardization (ISO), provide benchmarks for quality and performance. These standards ensure that products meet rigorous testing and compliance criteria, offering assurance to engineers and operators alike.
Trustworthiness in flap check valves is built through years of proven performance and adherence to best practices. Manufacturers who invest in research and development, advancing valve technology, and incorporating feedback from field applications, earn a reputation for producing reliable components. Similarly, routine inspections and timely maintenance contribute to their continued performance, with simple checks on flap condition, hinge integrity, and seal effectiveness preventing potential issues.
In conclusion, flap check valves are a pillar in the architecture of reliable fluid handling systems. Their appeal lies in their simplicity, efficiency, and dependability, making them a favored choice across numerous industrial applications. By integrating experience, expertise, authoritativeness, and trustworthiness, these valves not only meet operational demands but exceed them, ensuring systems run smoothly and safely over time. Whether you're an engineer, a maintenance technician, or a procurement specialist, understanding and leveraging the benefits of flap check valves will undoubtedly augment the effectiveness of your fluid systems.