Understanding the flange type silent check valve is crucial for industries that prioritize efficiency and reliability in fluid control systems. As a significant component within piping systems, this valve is renowned for its design, which minimizes noise and prevents water hammer, a common issue in many commercial and industrial applications.
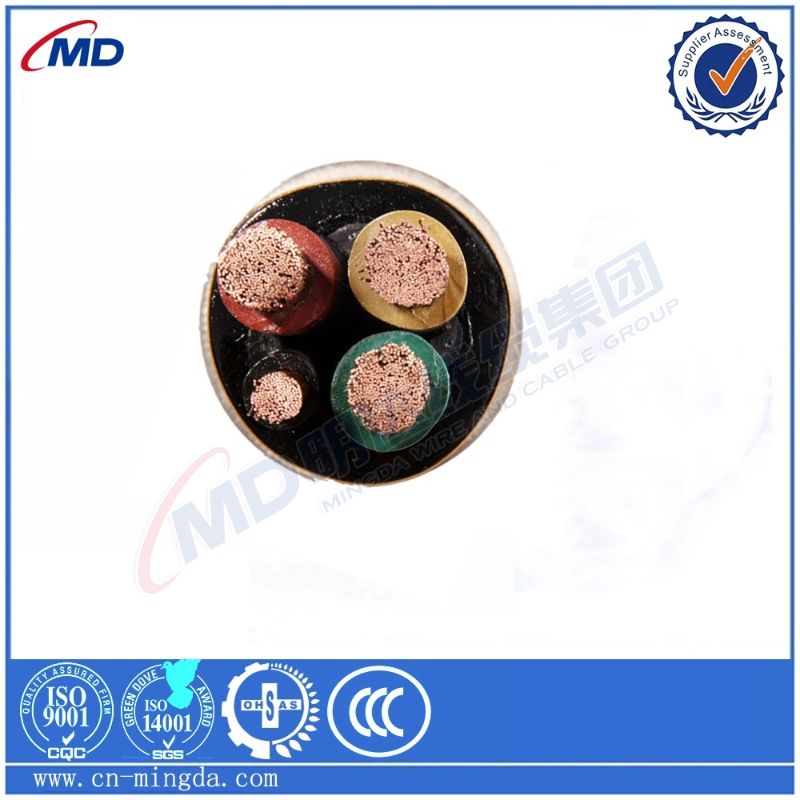
The flange type silent check valve employs a disc that moves forward and backward, controlled by the inlet and outlet pressure of fluids. Unlike traditional check valves that might slam shut and create a loud noise, the silent check valve closes slowly, reducing the hydraulic shocks and subsequent noise. This characteristic makes it invaluable in settings where maintaining a quiet and stable environment is essential, such as in hospitals or residential water systems.
Precision engineering is at the core of the flange type silent check valve. It requires a high level of expertise to design and manufacture a valve that meets the rigorous standards of modern industries. Expert manufacturers often emphasize the symmetrical design of the valve, which ensures even pressure distribution and minimizes wear and tear on its components. This kind of insightful engineering minimizes maintenance costs, which is crucial for operations dependent on continuous uptime.
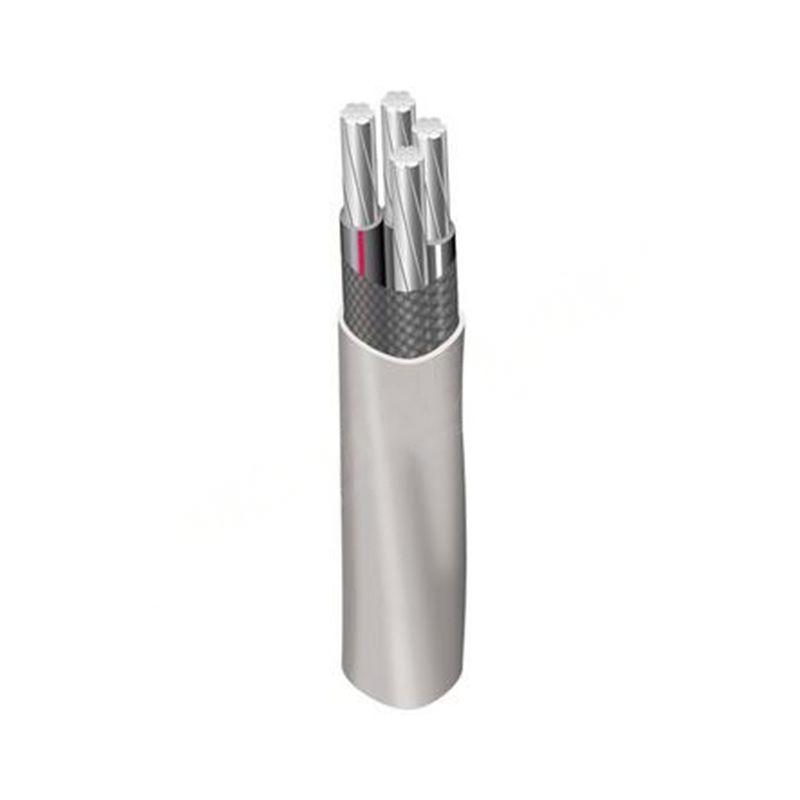
Functionality and reliability are closely tied to the materials used in manufacturing these valves. Typically crafted from durable metals like stainless steel, cast iron, or ductile iron, these valves offer excellent resistance to corrosive environments. This choice of material not only extends the valve's lifespan but also enhances its performance across various temperature and pressure ranges. When selecting a flange type silent check valve, it's advisable to consult with specialists who can provide guidance based on specific industry requirements, such as chemical resistance or exposure to extreme temperatures.
In terms of installation, the flanged ends of these valves offer a significant advantage. They allow for easy attachment between piping sections, ensuring a robust connection that can handle high-pressure systems effectively. Properly aligning and torquing the flanges is critical for optimal operation and safety, necessitating professional knowledge and experience. Incorrect installation can lead to misalignment and potential leaks, compromising the entire system's integrity.
flange type silent check valve
Expertise in this domain involves understanding the dynamics of fluid systems and selecting the appropriate valve size. A valve that is too small can cause excessive pressure drop, while one that is too large might not close properly, leading to backflow and contamination risks. Acquiring the right valve size involves calculations based on flow rate, pressure, and the fluid's characteristics.
Moreover,
the industry reputation of silent check valve manufacturers speaks to their authority. Companies with a long-standing history of innovation and quality often provide comprehensive support and warranties. Engaging with such firms enhances trustworthiness, offering peace of mind that their products have undergone rigorous testing and meet international standards.
Decision-makers should consider the certification and compliance factors associated with these valves. Adherence to standards like API, ANSI, or ISO signifies a commitment to quality and reliability. Trusting manufacturers with these credentials ensures that the check valves will perform as expected in critical applications.
For industries like petrochemical, pharmaceutical, or any sector requiring precise fluid control, the flange type silent check valve proves indispensable. Its combined attributes of noise reduction, durability, and reliability position it as an essential component in modern piping systems.
To summarize, the flange type silent check valve is more than just a tool; it represents a blend of innovation and practical engineering. Emphasizing expertise and reliability, this valve ensures operational efficiency and longevity, securing its place as a trusted component in the complex world of fluid control. Engaging with industry experts and reputable manufacturers ensures that businesses can effectively harness the full benefits of this sophisticated piece of technology, keeping systems running smoothly with minimal downtime.