A flanged ball valve stands as a critical component in fluid and gas control within various industries, providing unmatched reliability and efficiency. This type of valve, with its robust design, is essential for applications that demand a dependable seal and minimal leakage. Unlike threaded or welded connections, flanged ball valves offer the superior advantage of being easily removable from a pipeline, making maintenance operations significantly less cumbersome and more cost-effective.
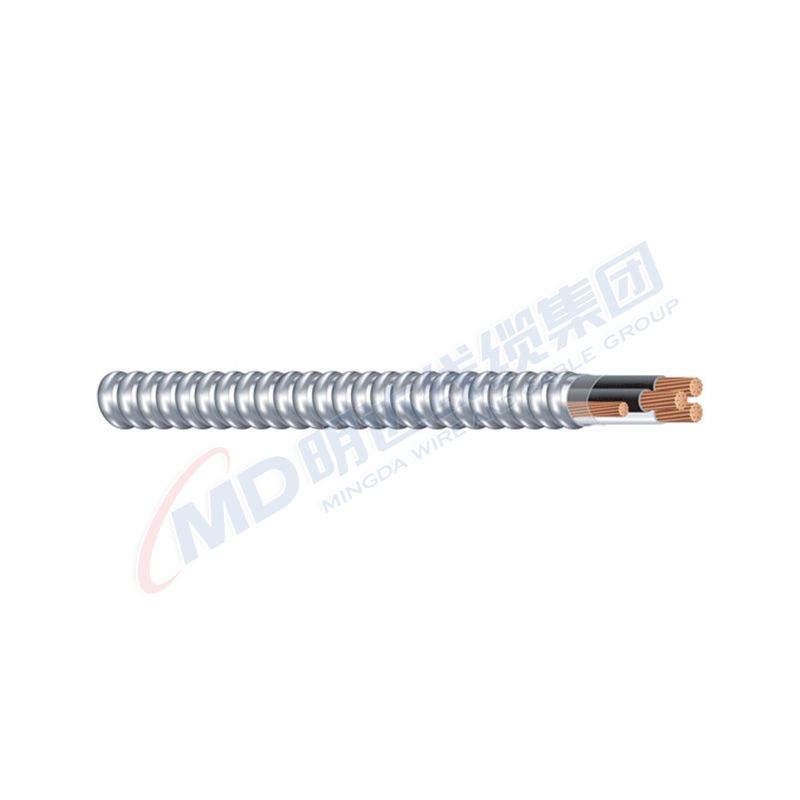
The core of a flanged ball valve’s function lies in its spherical disc — the ball — which precisely regulates fluid flow through varying degrees of rotation. This precision is the product of advanced engineering; the ball is meticulously polished to ensure smooth operation and prevent any hiccups in the motion that might compromise the system. The ball is also designed to pivot on seats made from durable materials like Teflon, which are engineered to withstand extreme pressures and temperatures, ensuring a tight seal over a broad spectrum of conditions.
These valves are constructed to endure the most demanding environments, evident in their material variety, ranging from stainless steel to carbon steel, each chosen based on the specific requirements of a given application, such as chemical compatibility and pressure demands. Stainless steel, for instance, offers excellent resistance to corrosion, making it ideal for industries dealing with harsh chemicals. In contrast, carbon steel, with its robust physical properties, is preferred for high-pressure applications.

One of the standout features of a flanged ball valve is its ease of operation. The quarter-turn mechanism simplifies control, allowing for quick fluid stoppage or release. This mechanism is crucial in emergency scenarios where swift isolation of a fluid is necessary, underscoring the valve’s role in enhancing safety measures within a system.
Industry experts favor flanged ball valves for their versatility, which is showcased in diverse applications ranging from oil and gas pipelines to wastewater management systems. In oil refineries, they are utilized to control the flow of crude oil and refined products, ensuring operational efficiency and safety. In contrast, in the municipal wastewater sector, these valves are integral in managing sewage flow, where their resistance to wear and degradation is critical in extending the maintenance cycle and reducing life-cycle costs.
flanged ball valve
Their design also incorporates features intended to bolster reliability and safety. Many flanged ball valves include anti-static devices, which prevent static electricity that might ignite volatile fluids, and blowout-proof stems, which ensure that in high-pressure scenarios the stem remains securely in place, averting potential system failure.
The design paradigm of flanged ball valves is equally informed by industry standards such as API, ANSI, and ISO, which provide guidelines ensuring each valve meets stringent safety and performance benchmarks. Regular audits and certifications by recognized bodies verify that flanged ball valves not only comply with international safety standards but thrive in surpassing them, further strengthening their reputation for reliability.
Moreover, modern technological advancements have seen the integration of smart technology into flanged ball valves, allowing for real-time monitoring and predictive maintenance. Sensors can now relay data about valve condition, pressure levels, and possible points of failure back to control systems, permitting operators to make informed decisions based on live feedback. This evolution in valve technology not only improves safety but also preserves operational longevity.
When selecting a flanged ball valve, one should consider factors such as the operational environment, the nature of the fluid being managed, pressure and temperature requirements, and specific industry regulations. Consulting with a valve expert ensures the selection of a suitable valve model that aligns with operational needs and enhances overall system uptime.
In summary, flanged ball valves represent an intersection of engineering excellence and industrial necessity. They offer a reliable solution for effective fluid management across a wide range of applications, ensuring both safety and efficiency. Their evolution continues to underline the pace of technological progression in the field of industrial machinery, offering a glimpse into the future of fluid control systems and the ongoing drive towards greater reliability and smarter functionality.