In the world of industrial components, the flanged ball valve stands as a pinnacle of engineering prowess, marrying simplicity with effectiveness. These robust devices are crucial for various applications that require precise control over fluid flow. Their design, predicated on expertise in mechanical engineering, showcases their exceptional capabilities for numerous industries such as chemical processing, oil and gas, and water treatment plants.
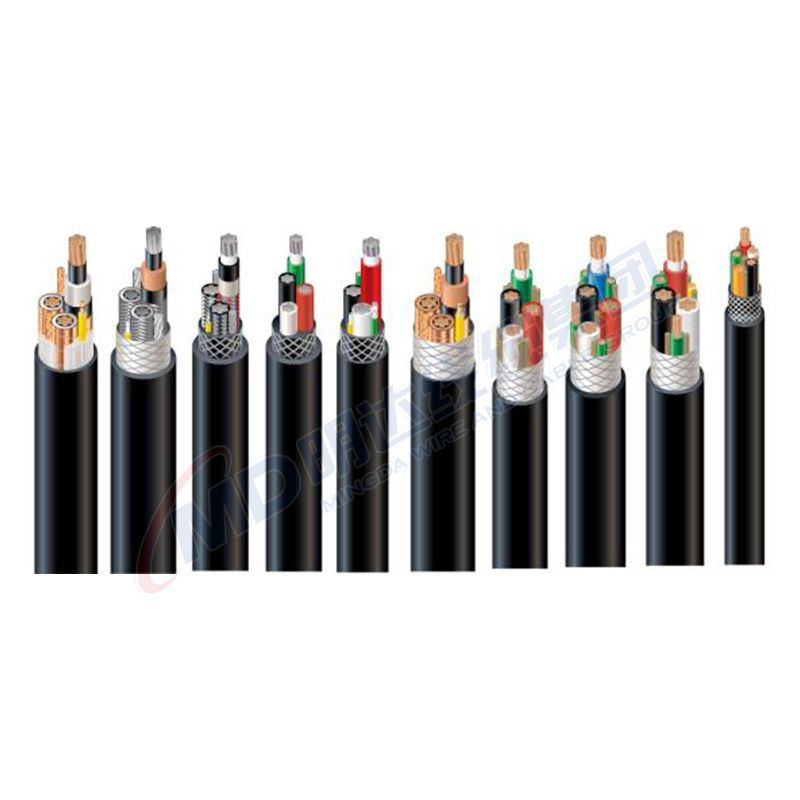
A flanged ball valve, characterized by its spherical closure unit, is designed to provide a reliable and leak-proof seal. This is achieved through the use of a rotatable ball with a bore through its center, pivoted at quarter-turn angles to allow or block flow. The expertise employed in crafting these devices ensures they withstand high pressures and temperatures, making them indispensable in setups where reliability is crucial.
The standard for flanged ball valves revolves around their robust construction, adeptly crafted from materials such as stainless steel, carbon steel, or specialized alloys. These materials are chosen for their durability and resistance to corrosion, ensuring long-term service even in aggressive environments. Expertise in metallurgy plays a key role here, as it allows for the selection of appropriate materials tailored to specific operational needs.
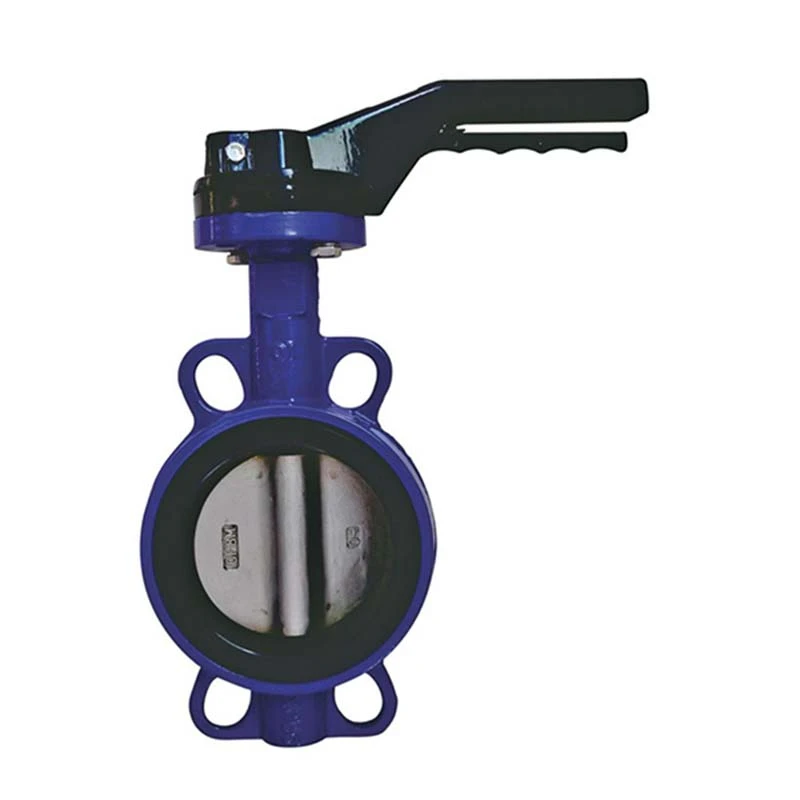
Flanged ball valves earn their name from the flanges that bolt them securely to pipes. This design not only provides stability in high-stress applications but also facilitates easy installation and maintenance, distinguishing these valves as a preferred choice in replaceable and serviceable systems. The engineering detail in these flanges also allows the incorporation of different standards, like ANSI, DIN, or JIS, catering to international industrial norms and boosting their authoritative standing in the global market.
The field of fluid dynamics heavily influences the application of flanged ball valves. Their design minimizes turbulence and pressure drop when fully open, optimizing flow efficiency. This efficiency is a testament to the authoritative understanding of fluid behavior, ensuring that the valves not only meet but exceed operational expectations for varying flow conditions.
flanged ball valve
Professionals in industries relying on these valves value their trustworthiness for their low maintenance requirements. The simplistic yet effective design reduces the likelihood of mechanical failures, with the trusted use of PTFE or other high-performance polymer seats providing excellent sealing capability. This reliability minimizes downtime, ensuring continuous operation - a critical factor for industrial applications where efficiency impacts profitability.
Experts continually innovate the design of flanged ball valves, integrating advanced technologies such as smart sensors and actuators. These enhancements allow for remote monitoring and control, offering predictive maintenance capabilities which bolster the trust and adoption of these valves in automated process systems. By continually adapting to technological advancements, manufacturers maintain the authoritative edge required in an evolving market landscape.
In practical application, case studies demonstrate the life-span and cost-effectiveness of flanged ball valves. For instance, a chemical plant replacing outdated valves with high-performance flanged ball models reported a significant drop in leakage incidents and maintenance costs. This real-world evidence underlines the experience-driven dependability and efficiency improvements garnered through their application.
Thus, in selecting a flanged ball valve, decision-makers not only procure a piece of hardware but secure a legacy of engineering excellence represented in decades of progressive improvements and field-driven adaptations. The choice of a flanged ball valve symbolizes a commitment to performance, reliability, and innovation, aligning with the highest expectations of quality and longevity in industrial implementations.