The ductile valve represents a pivotal component in the field of fluid control systems, renowned for its unique flexibility and resilience attributes. In comparison to traditional valves composed of more brittle materials, ductile valves are engineered using ductile iron, which stands out for its high tensile strength and durability. This material choice endows the valve with the capability to endure various pressures and temperatures, making it an indispensable asset in both industrial and residential applications.
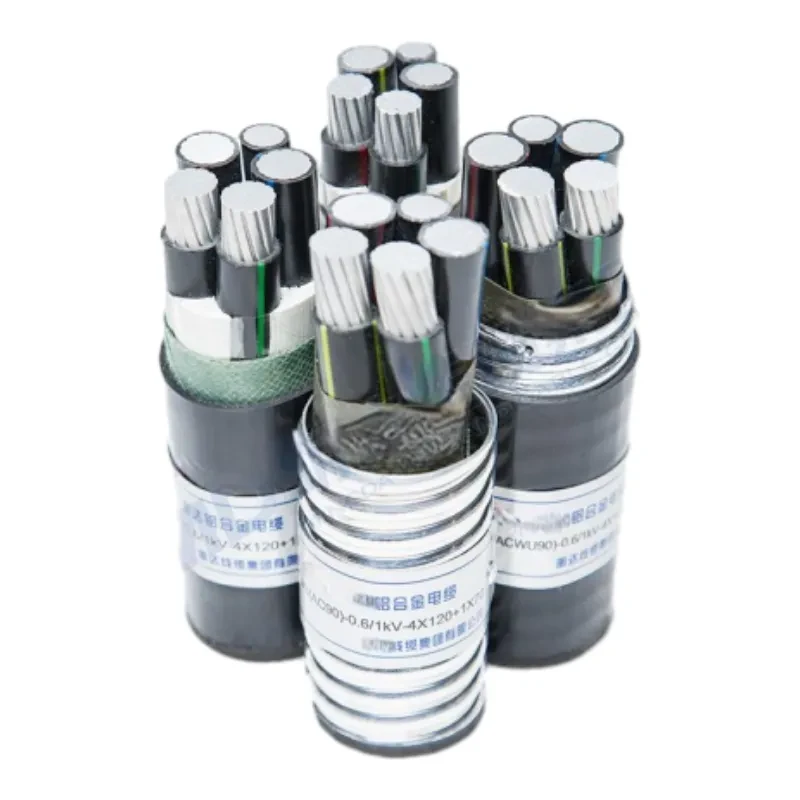
From an experiential standpoint, users of ductile valves consistently report a superior level of performance and reliability under challenging conditions. They have gained a reputation for maintaining operational integrity even when subjected to fluctuating pressure conditions. This is crucial in industries like oil and gas, water treatment, and construction, where system efficiency and stability can directly impact operational costs and safety. An example from an experienced industry professional highlighted a scenario where a ductile valve was able to outperform cast iron alternatives significantly in a high-pressure steam environment, decreasing maintenance frequency and prolonging the lifecycle of the entire system it was integrated into.
In terms of expertise, the manufacturing of ductile valves involves a high degree of precision and adherence to stringent quality standards. Engineers focus on ensuring that the microstructure of the ductile iron is perfectly controlled to maximize its graphite nodules, which contribute to its ductility without compromising strength. This fine balance is overseen by seasoned metallurgists and engineers who bring years of experience to the design and production processes. Additionally, innovations like varying alloy compositions and heat treatment techniques are leveraged to fine-tune the valve’s properties, optimizing them for specific operational contexts.
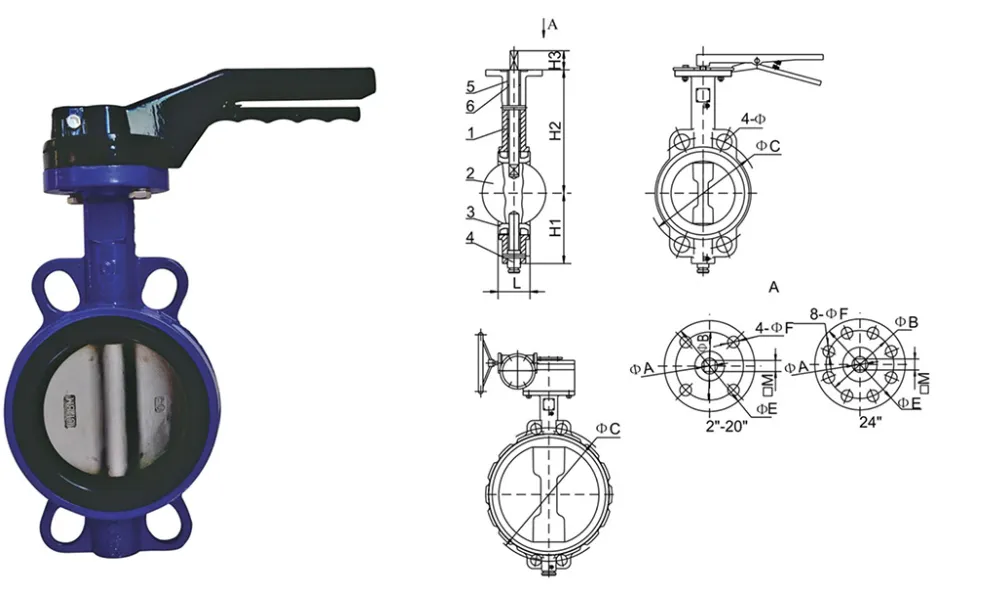
ductile valve
Authoritativeness in the context of ductile valves is established through rigorous testing and certification processes. These valves are subjected to a battery of assessments to ensure compliance with international standards such as ASME, ISO, and ANSI.
Such certifications not only validate the valve’s performance metrics but also provide stakeholders with a tangible benchmark for quality assurance. Leading manufacturers often have extensive libraries of performance data and case studies available to potential clients, showcasing the valve's capacity to perform reliably in diverse applications.
Trustworthiness is inherently tied to the material's long-term performance and the credibility of its manufacturer. A commitment to sustainable manufacturing practices and the environment further enhances a ductile valve's reputation. Companies that emphasize transparency in their supply chain, from raw material acquisition to final product delivery, build greater trust. They often provide extensive warranties and customer support services, reinforcing consumer confidence in their products. Moreover, employing ductile iron, which is recyclable, aligns with global efforts towards sustainable industrial practices, thus appealing to eco-conscious stakeholders.
In conclusion, ductile valves possess a combination of experience-driven efficiency, expert manufacturing, authoritative certification, and trustworthy practices, which make them a premier choice for various critical applications. Their developmental trajectory suggests a continuous evolution, supported by ongoing research into advanced material science and manufacturing innovations. This focus on progressive improvement guarantees that ductile valves will remain a cornerstone technology in efficient fluid management solutions well into the future. As industries advance, those incorporating ductile valves are likely to experience enhancements in system integrity, cost reduction, and operational safety, ensuring they stay ahead in performance and environmental stewardship.