Ductile iron check valves are integral components within numerous industrial applications, known for their resilience and reliability. By understanding the unique characteristics and applications of these valves, industries can make informed choices in their piping systems, enhancing both efficiency and longevity.
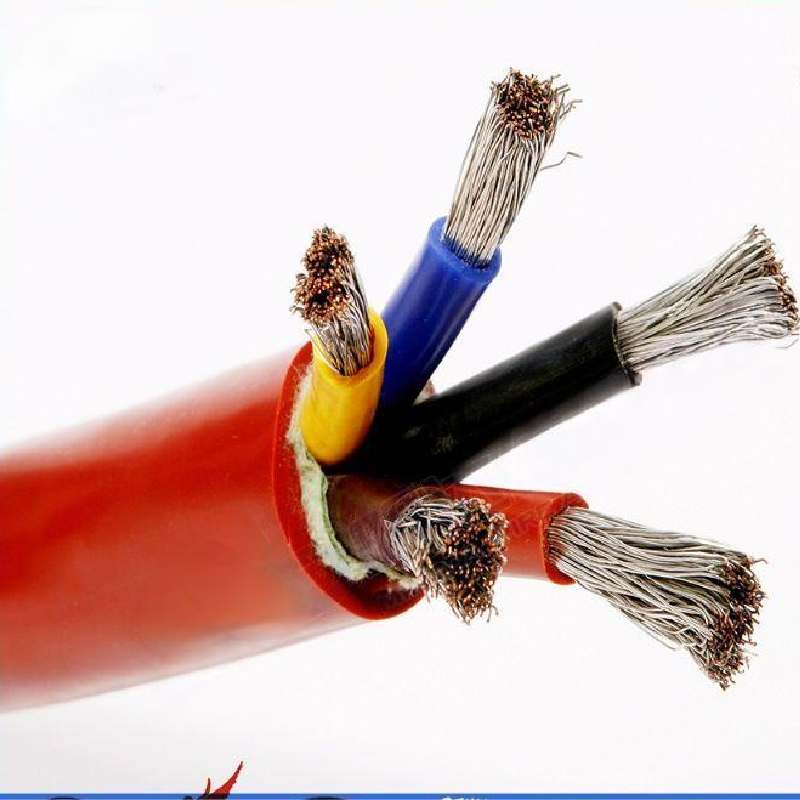
Ductile iron, as a material, offers a compelling mix of strength and ductility, characteristics that make it especially suited for demanding environments. Unlike traditional cast iron, ductile iron contains graphite in the form of nodules, rather than flakes, which imparts a superior tensile strength and impact resistance. These properties ensure that ductile iron check valves can withstand significant pressure and stress, making them ideal for high-performance applications.
The primary function of a check valve is to allow fluid to flow in one direction while preventing backflow. In systems where the prevention of reverse flow is critical for maintaining operational integrity, such as in water and wastewater management, ductile iron check valves provide a reliable solution. Their robust construction not only accommodates high flow rates but also protects the system from potential damage due to pressure surges or system failures.
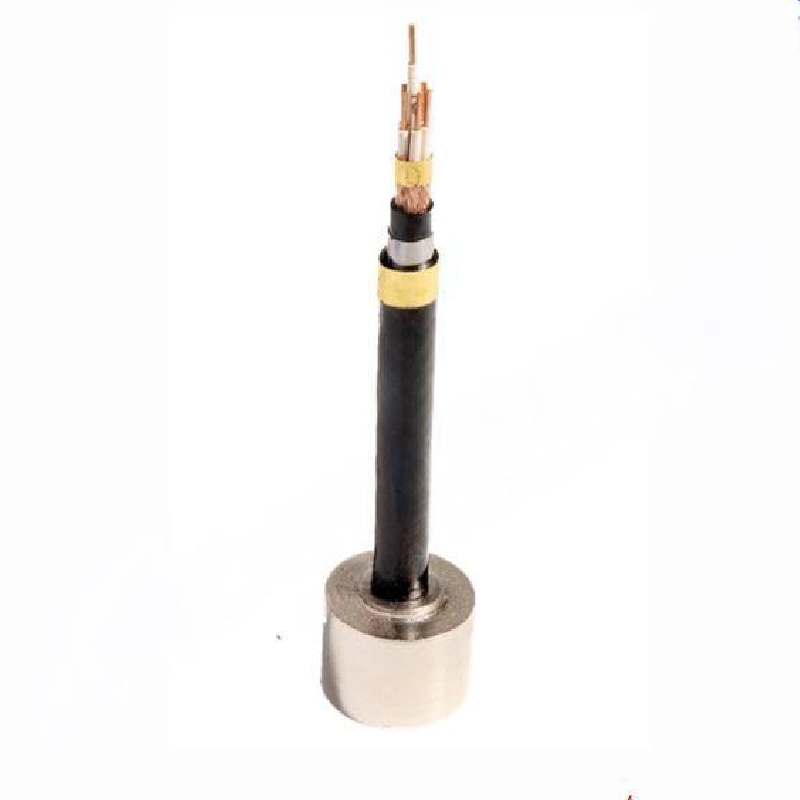
In terms of design, ductile iron check valves are available in various configurations, including swing check, ball check, and wafer check designs. Each type serves specific operational needs, with the swing check valve being one of the most commonly used due to its simple, yet effective, mechanism. The valve's disc swings open with the flow pressure and closes in response to reverse flow, making it particularly suitable for applications where a tight seal is paramount.
Beyond technical specifications, the implementation of ductile iron check valves represents a long-term cost-saving measure for industries. Their durability reduces the need for frequent replacements and maintenance, translating into reduced operational downtime. Moreover, their corrosion resistance ensures longevity even in chemically aggressive environments, such as in chemical processing plants or sewage treatment facilities.
ductile iron check valve
Expertise in selecting the right type and size of check valve is critical to optimizing performance. Factors such as pressure rating, temperature range, and the nature of the fluid being handled must be considered. Consulting with experienced engineers and specialists can provide valuable insights, ensuring the valve meets all system requirements and adheres to industry standards.
The authority of ductile iron check valves in industrial applications is further reinforced by their compliance with international standards such as ASTM A536, which sets forth specific requirements for the production of ductile iron materials. This compliance ensures that valves not only perform under expected conditions but also conform to regulatory mandates, providing additional assurance to operators and maintenance teams.
Trustworthiness is another key attribute of ductile iron check valves, given their proven track record in critical infrastructure projects around the globe. From large-scale water distribution networks to complex chemical plants, their ability to perform consistently under various conditions has been documented in numerous case studies and industry reports. This history of reliability makes them a preferred choice for professionals seeking a balance of performance, durability, and cost-effectiveness.
Furthermore, innovations in manufacturing and design have led to enhancements in ductile iron check valve technology. Advanced coatings and treatments now further extend their lifespan and efficiency, reinforcing their role as indispensable components in modern engineering solutions. By staying abreast of these developments, industries can continually improve their systems, promoting sustainability and operational excellence.
In conclusion, ductile iron check valves stand out as essential components in industrial fluid systems. Their combination of material strength, functionality, and longevity makes them an ideal choice for a range of applications. With proper selection and maintenance, industries can leverage these valves to protect assets, improve system performance, and achieve long-term operational goals.