Dual plate check valve wafer type products have gained significant recognition in various industries for their efficiency and reliability. Known for their compact design and effective performance, these valves play a crucial role in fluid management across numerous applications. This article demystifies the dual plate check valve wafer type, exploring its features, applications, and why they are considered essential by experts in the field.
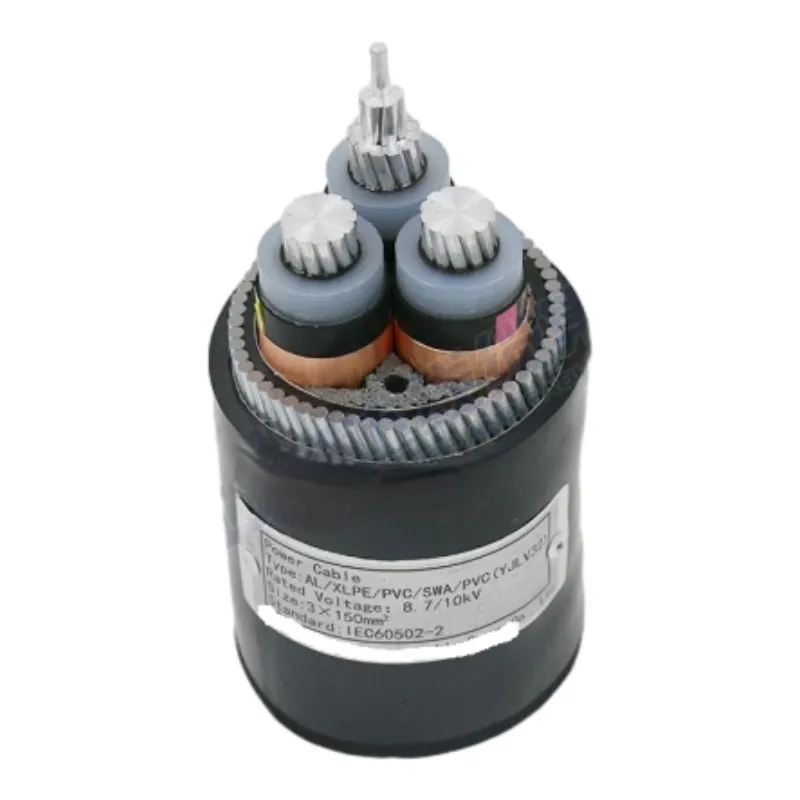
Dual plate check valves, commonly referred to as butterfly check valves, are engineering marvels designed to prevent backflow and ensure a one-way flow of fluids, which can be either gases or liquids. They consist of two spring-loaded plates that open with forward flow and close tightly when the flow reverses, thus preventing any backflow. The wafer type designation typically describes their thin, space-saving profile designed to fit between a set of flanges.
The engineering precision behind dual plate check valves ensures minimal pressure drop across the valve while providing maximum flow efficiency. This is a significant advantage over traditional swing check valves, which can cause substantial flow disruption. For engineers and process managers focused on optimizing system performance, the wafer-type structure of these valves is critical. It allows them to be installed in systems where space and weight are significant concerns without sacrificing performance.
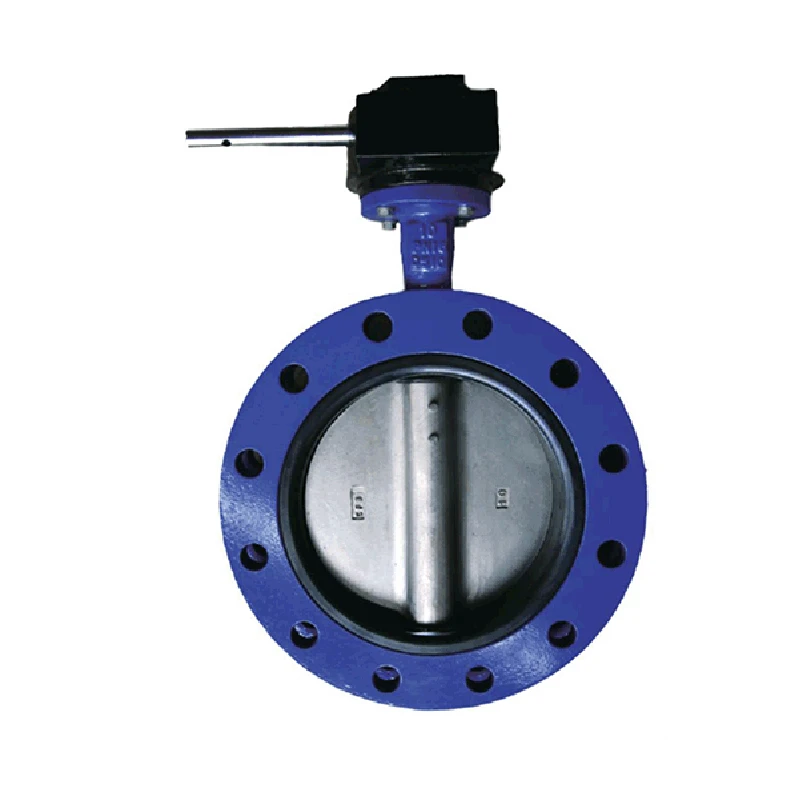
In terms of materials and construction, dual plate check valves are versatile, being manufactured from robust materials such as stainless steel, carbon steel, and specialty alloys, making them suitable for handling a variety of fluids, including corrosive fluids. This material diversity not only extends their applicability across different industrial sectors but also enhances their durability and life span, two factors that are integral to cost efficiency in fluid management systems.
From an expertise standpoint, the design of dual plate check valves allows for a low cracking pressure, meaning they open easily with a reduced upstream pressure. This feature is critical in systems where maintaining a low pressure drop is essential. Furthermore, the dual plate check valve wafer type can be configured with metal-to-metal sealing or soft sealing depending on the application's requirements, highlighting its adaptability to meet specific systems' needs.
dual plate check valve wafer type
Experts across industries praise dual plate check valves for their easy installation and low maintenance requirements. The simplicity of the wafer type design means fewer moving parts, which reduces wear and the potential need for repairs, leading to increased reliability. This characteristic is particularly vital in applications such as water treatment plants, HVAC systems, oil and gas pipelines, and chemical processing, where continuous operation is crucial.
Authoritative studies and technical references often cite the dual plate check valve wafer type for its enhanced safety features. The compact, versatile design minimizes the risk of water hammer—a common issue in conventional check valves that can lead to pipeline fatigue and failure. By effectively dampening the slam effect caused by fluid flow reversal, dual plate check valves reduce the risk of catastrophic system failures, thereby promoting a safer operational environment.
From a trustworthiness perspective, the widespread use of dual plate check valves in mission-critical applications speaks volumes about their reliability. Industries, including petrochemicals, pharmaceuticals, and food processing, employ these valves, trusting their performance to safeguard precious resources and ensure operational integrity.
Overall, dual plate check valve wafer type products combine expert engineering, durable construction, and trusted performance to offer an essential solution in modern fluid control systems. Their unique blend of efficiency, reliability, and adaptability reaffirms their position as a preferred choice for engineers and industry professionals worldwide. As industries continue to evolve, adopting more sophisticated technologies, these valves prove to be timeless pieces of engineering that continue to meet the demanding needs of contemporary fluid dynamics.