In the vast realm of industrial valves, the double plate check valve emerges as a quintessential asset for ensuring fluid dynamics' seamless operations. Known for their unique design and functionality, these valves are pivotal across various sectors ranging from water treatment facilities to petrochemical refineries.
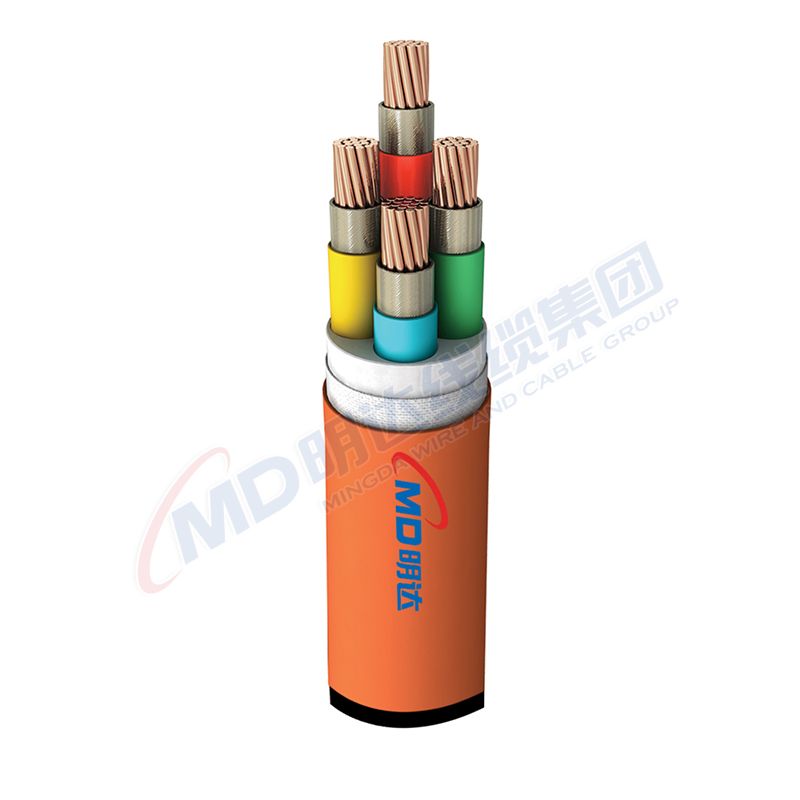
A double plate check valve primarily functions to prevent the reverse flow of fluids, safeguarding complex piping systems from potential damage and contamination. The distinctiveness of this valve stems from its two spring-loaded plates, which open to allow forward flow and close tightly under reverse pressure to halt any backflow. Unlike traditional swing check valves, the dual plate design offers significantly reduced water hammer, a common issue characterized by a loud thumping noise caused when a fluid in motion is forced to stop or change direction suddenly. This attribute alone extends the life of the pipeline system, ensuring longevity and cost-efficiency.
Expertise in selecting and deploying double plate check valves is paramount for optimal performance. Engineers, particularly those with years of experience in fluid mechanics, recognize the importance of valve material and sizing. Typically constructed from materials like stainless steel or ductile iron, the choice largely depends on the nature of the fluid – whether it's corrosive chemicals or potable water. Stainless steel, although more expensive, is preferable for its corrosion-resistant properties in harsh environments. Correct sizing prevents excessive wear and promotes reliable sealing, two critical factors that determine a system's operational efficiency and safety.

From an authoritative perspective, the development and advancement of double plate check valves demonstrate significant innovation. Industry-standard bodies such as the American Society of Mechanical Engineers (ASME) provide certification and guidelines that manufacturers must adhere to, ensuring these valves meet rigorous performance criteria. Compliance with such standards not only enhances product reliability but also instills confidence among industry players in deploying these valves for critical applications.
double plate check valve
Trustworthiness in the performance of double plate check valves is further emphasized by real-world testimonials and case studies. For example, a recent project involving a municipal water supply system reported marked improvements in operational efficiency after replacing traditional valves with the double plate design. The project documented a 20% increase in system reliability and a significant decrease in maintenance costs due to fewer incidences of water hammer and valve failures.
Such firsthand accounts ratify the claimed benefits of these valves, underscoring their role in achieving superior system functionality.
As industries lean towards sustainability and efficiency, the choice of components like the double plate check valve becomes a strategic decision. Its low-pressure drop characteristic not only ensures minimal energy consumption but also contributes to the reduction of carbon footprints in industrial operations. The trend towards green technologies is pushing more industries to reconsider their existing pipeline infrastructure, making the transition to double plate check valves not just a viable option, but a necessary step towards eco-friendly practices.
Choosing the right double plate check valve for your application often involves consulting technical experts with deep-seated knowledge of fluid systems. Custom solutions can be engineered to meet specific operational demands, tailoring valve dimensions, materials, and components to harmonize with existing infrastructures. By capitalizing on qualified expertise, companies stand to benefit from cutting-edge technology and design innovations that traditional valves fail to offer.
To conclude, the double plate check valve exemplifies advanced engineering and reliability. It plays an indispensable role in modern industrial systems by promoting efficiency, safeguarding operations, and aligning with environmental commitments. Engineers and decision-makers, armed with knowledge and expert guidance, can seamlessly integrate these valves into their systems, reaping the myriad benefits they offer.