The double eccentric flange butterfly valve stands as a testament to modern engineering marvel, merging cutting-edge technology with meticulous craftsmanship. Renowned for its precision, adaptability, and efficiency, this valve has gained accolades across industries, making it an essential component in fluid control systems worldwide.
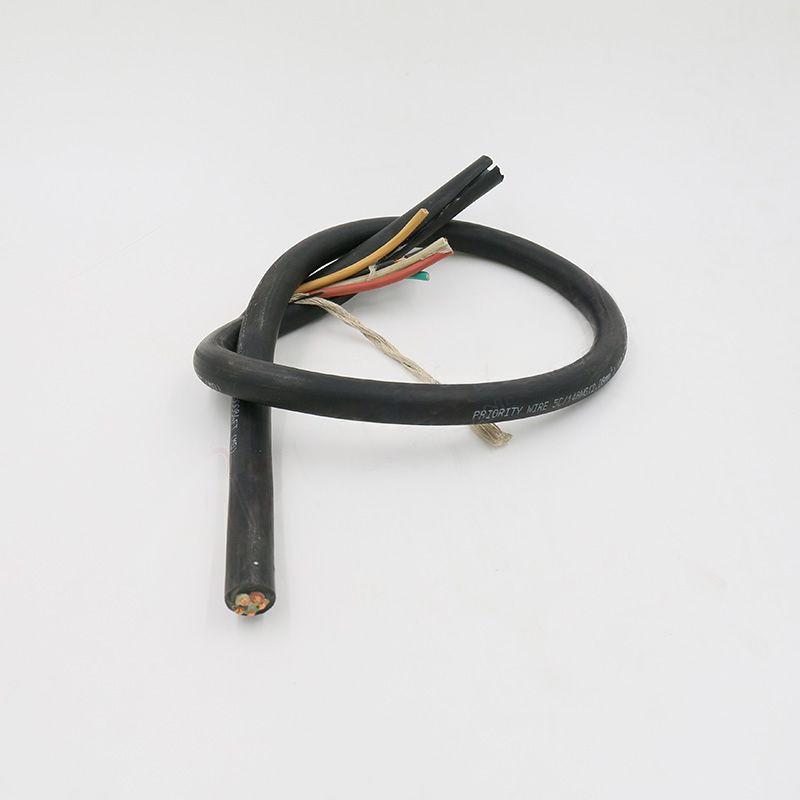
This double eccentric design is distinguished by its unique architecture. The innovation lies in its dual offset structure the shaft is offset from the center of the valve and body, and the disc is further offset from the shaft. This configuration ensures that the disc only comes into contact with the seal at the final stage of closure, significantly reducing wear and tear. This not only enhances the valve's lifespan but also minimizes maintenance requirements, leading to substantial cost savings for operators.
Integral to its design is the flange connection, which provides superior stability and strength. This makes the valve particularly suitable for high-pressure applications, where reliability is non-negotiable. Industries such as oil and gas, water treatment, and power generation choose these valves for their durability and ability to provide a tight seal under extreme conditions. The flange design also simplifies installation and replacement processes, a crucial consideration in fast-paced industrial environments.
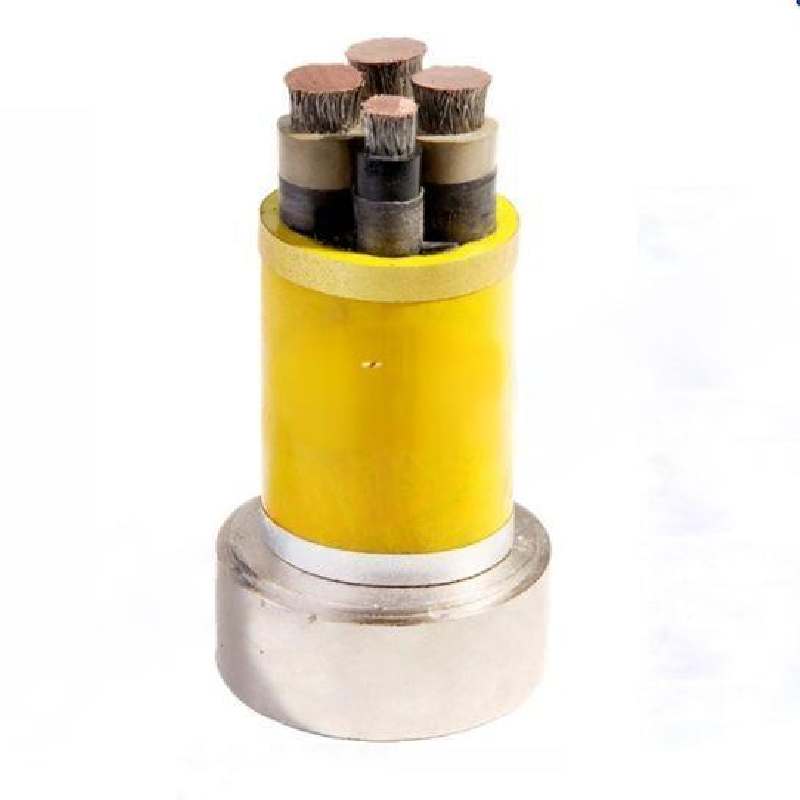
The material selection for double eccentric flange butterfly valves is another critical aspect. High-performance materials like stainless steel, carbon steel, and specialized alloys are often used, offering excellent resistance to corrosion, erosion, and extreme temperatures. This ensures that the valves perform optimally in challenging environments, providing peace of mind to engineers and operators alike.
An expert in valve technology might highlight how these materials and designs contribute to energy efficiency. By reducing leakages and ensuring precise flow control, they play a crucial role in energy conservation, aligning with global sustainability goals. This is a key selling point for industries looking to reduce their carbon footprint.
double eccentric flange butterfly valve
Ensuring quality and compliance is another area where double eccentric flange butterfly valves excel. Leading manufacturers subject these valves to rigorous testing, in line with international standards such as API, ISO, and EN. This commitment to quality is backed by decades of expertise and a proven track record, establishing trustworthiness and authoritativeness in the marketplace.
User-centric design has not been neglected. Many modern iterations of these valves come equipped with advanced features such as position indicators, automated actuation, and smart controls. These enhancements provide operators with real-time insights and control over the valve operations, integrating seamlessly with Industrial Internet of Things (IIoT) systems. Such innovations underscore the valve's adaptability to future technology landscapes, ensuring it remains relevant in ever-evolving industrial applications.
From an operational perspective, user experience (UX) with double eccentric flange butterfly valves is overwhelmingly positive. Users often remark on the intuitive interface, minimal torque requirements, and the smooth operation of the valve. These features reduce operator fatigue and error, thus enhancing overall plant safety and efficiency. The feedback loop between engineers, operators, and manufacturers has been instrumental in refining these valves continuously, a testament to the collaborative effort in advancing valve technology.
Finally, the future of the double eccentric flange butterfly valve looks promising. Continuous research and development efforts are poised to introduce even more resilient materials, finer control mechanisms, and enhanced digital integrations. As industries worldwide embrace automation and smart technologies, these valves are set to become even more integral to advanced fluid management systems.
In conclusion, the double eccentric flange butterfly valve represents more than just a mechanical component—it is an embodiment of engineering expertise, reliability, and forward-thinking innovation. Its ability to cater to a diverse array of industrial applications while maintaining efficiency and sustainability makes it a cornerstone in modern industrial infrastructure. As we move forward, its role and relevance are set to grow, driven by a commitment to excellence and the relentless pursuit of technological advancement.