Selecting the right components for fluid control systems in industrial applications is crucial to ensure efficiency, reliability, and safety. Among the array of options available, the double ball check valve stands out due to its unique design and functionality. This specialized valve type is not only an essential component in preventing backflow but also offers numerous advantages that make it preferable in a wide range of industries.
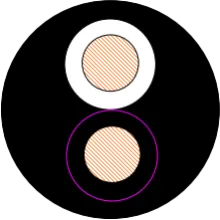
Double ball check valves are specifically engineered to enable unidirectional flow, automatically preventing reverse flow by using two balls within the valve housing. These balls are typically seated within two distinct chambers, each equipped with a spring-loaded mechanism that closes the ball onto the seat when fluid pressure drops or reverses. This configuration enhances the valve's sealing capabilities, providing a tight seal even under varying pressure conditions, which is ideal for applications where leaky valves could lead to contamination or costly downtimes.
One of the critical advantages of double ball check valves is their robustness and ability to handle high-pressure environments. This capability is particularly beneficial in industries such as oil and gas, chemical processing, and water treatment plants, where maintaining pressure integrity is essential. By deploying such valves, operators can assure a seamless flow process, minimizing the risk of system failures.

In addition to pressure handling, these valves are also lauded for their low maintenance requirements. The design simplicity, characterized by fewer moving parts compared to other valve types, decreases the likelihood of mechanical wear and tear. This, in turn, enhances longevity and reduces the operational costs associated with frequent replacements or repairs. When maintenance is required, the straightforward design allows for quick disassembly and reassembly, ensuring minimal downtimes and interruptions.
For engineers and facility managers prioritizing safety, double ball check valves offer heightened security due to their dual-seal mechanism. This design minimizes the risk of leaks, which is paramount in the transportation of hazardous or toxic fluids. Furthermore, they contribute to environmental protection by reducing the chance of accidental spills or emissions, aligning operations with stringent environmental regulations.
double ball check valve
Importantly, selecting the right material for double ball check valves can enhance their application suitability. Manufacturers often offer these valves in materials like stainless steel, brass, and PVC, each suited to distinct fluid types and operating environments. For example, stainless steel is optimal for corrosive applications, while PVC might be preferred for lighter, less aggressive substances. Consulting with experts and detailed analysis of the specific application needs can guide an informed material choice, ultimately enhancing the system's reliability and lifespan.
Furthermore, customization options available with double ball check valves allow for precise tailoring to specific operational needs. From varying sizes to accommodate different pipe diameters, to unique seating materials that improve resistance to specific chemicals, these valves can be adjusted in numerous ways. Such flexibility makes them a versatile solution, contributing significantly to their authoritative reputation in the industry.
To ensure optimal performance, it is crucial to source double ball check valves from reputable manufacturers who adhere to stringent quality standards. Certifications and compliance with international standards like ISO or ANSI provide additional assurance of the product's reliability and durability. Engaging with manufacturers who offer comprehensive support, including installation guidance, troubleshooting, and after-sales service, can further cement the trust in the investment.
In conclusion, double ball check valves represent a vital component in fluid management systems, offering unparalleled advantages in terms of reliability, efficiency, and safety. Their robust design, low maintenance needs, and adaptability make them an esteemed choice for industrial applications. By prioritizing quality and engaging with authoritative manufacturers, industries can leverage these valves to enhance operational integrity and protect both financial and environmental interests.