The di wafer type butterfly valve is more than just an industrial component; it epitomizes the intricate blend of engineering innovation and industrial application. At its core, this valve is designed to offer superior flow control with compact convenience. In recent years, professionals across industries such as water treatment, oil and gas, and chemical processing have gravitated towards this valve due to its numerous benefits.
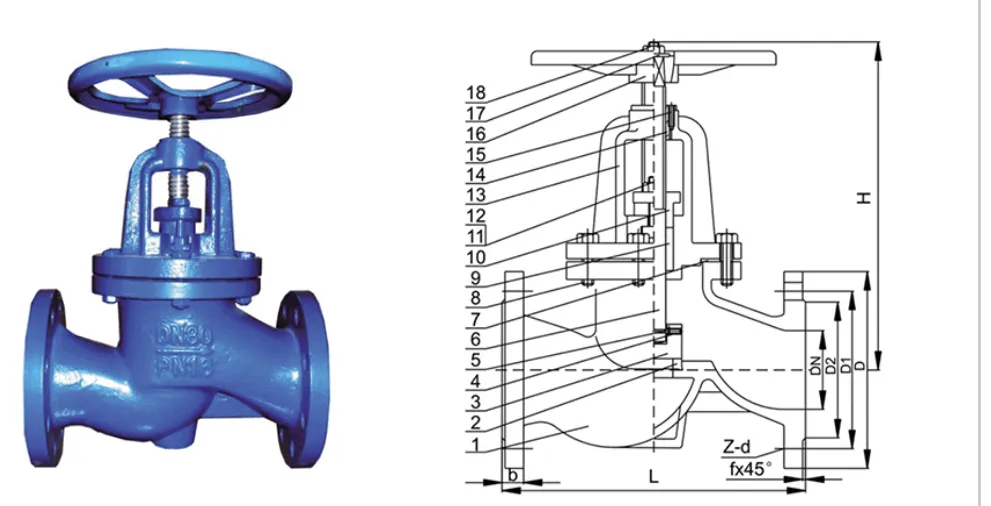
These butterfly valves are defined by their distinct wafer-style, which is designed for direct fitting between flanges. This design simplifies installation processes, as it eliminates the need for additional nuts and bolts. Experts appreciate this feature because it minimizes pipeline weight and ensures ease of maintenance, positioning it as an optimal choice over traditional flanged valves.
Delving into its functionality, the di wafer type butterfly valve excels in regulating flow through the utilization of a circular disc or vane that pivots around an axis. This rotational movement, controlled by an actuator or a manual lever, allows for precise modulation of fluid flow. With an increasing demand for efficient flow management, the expertise that these valves provide is nearly unmatched. They offer a robust solution for applications requiring quick shut-off capabilities—an aspect appreciated by industry veterans for its role in mitigating leak risks.

The durability of the di wafer type butterfly valve lies in its construction from ductile iron (DI). Ductile iron enhances the valve's mechanical strength and corrosion resistance. This material choice, reflecting extensive expertise in metallurgy, ensures that the valve can withstand the arduous conditions found in industrial environments. It further involves the integration of seat materials like EPDM, NBR, or PTFE to accommodate varying temperature and pressure conditions. This deeper understanding of materials science underscores the valve's adaptability across different applications.
In terms of authority, manufacturers of di wafer type butterfly valves bring decades-long legacies to the table. Renowned brands invest heavily in research and development to refine these valves, supporting them with certifications such as ISO and CE. These achievements reinforce the reliability of the product, assuring buyers of its adherence to global standards. Additionally, manufacturers provide comprehensive documentation, offering insights into valve specifications, installation guides, and maintenance procedures, which enhances its credibility among engineers and procurement specialists.
di wafer type butterfly valve
An important trust factor for many industries is the valve's ability to perform under stringent safety standards. The di wafer type butterfly valve is engineered to limit potential hazards like cracking or deformation during operation. Its design features, such as blowout-proof stems and low torque operations, add layers of protection, fostering trust among users who rely on these components to maintain seamless operations within their facilities.
The real-world application of di wafer type butterfly valves offers tangible proof of their effectiveness. For instance, in water treatment facilities, these valves control water flow with precision, optimizing treatment processes and minimizing waste. Within the oil and gas sector, they play a crucial role in ensuring efficient flow control and safety in complex pipeline systems. The chemical industry also benefits from their corrosion-resistant properties, which enhance longevity and operational stability.
The decision to opt for a di wafer type butterfly valve should be informed by a thorough understanding of your application needs. Consider factors such as fluid type,
operating temperature, and pressure conditions to select the right valve configuration. Consulting with experts who have hands-on experience with these valves can provide additional insights, ensuring that the chosen valve aligns with operational requirements.
In conclusion, the di wafer type butterfly valve stands out as a critical component for modern industrial applications. Its streamlined design, combined with the durable construction and adaptive functionality, positions it as a valued asset for industries in pursuit of efficiency and reliability. By choosing a reputable manufacturer and understanding the valve's capabilities, industries can enhance their operational infrastructure, demonstrating to stakeholders and competitors alike that they are equipped with the most advanced fluid control technology available.