DIN metal seat gate valves are a pivotal component in fluid handling systems across various industries. These valves, renowned for their robustness and reliability, serve as an essential solution for applications requiring assured shut-off capabilities and resilience against intense conditions. This article delves into the critical aspects that make DIN metal seat gate valves a preferred choice for industries, offering insights gleaned from both technical expertise and practical experiences.
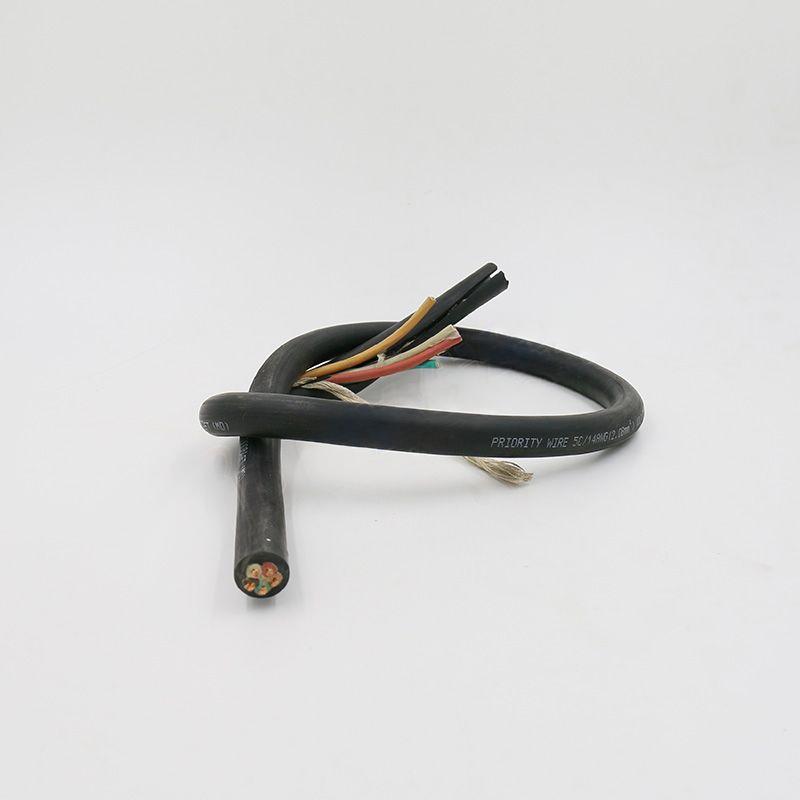
DIN metal seat gate valves, constructed adhering to the Deutsche Institut für Normung (DIN) standards, feature a metal-to-metal sealing mechanism which ensures a tight shut-off, essential for preventing leakage in pipelines carrying hazardous fluids. This metal seal is particularly beneficial in high-temperature and high-pressure environments, where rubber or composite seals might fail. Industries such as oil and gas, petrochemical, and power generation find these valves invaluable due to their ability to maintain integrity under severe operational conditions.
One of the distinctive features of DIN metal seat gate valves is their design which facilitates unobstructed flow and minimal pressure drop, crucial for maintaining operational efficiency and energy conservation. The precision engineering involved in producing these valves is reflective of the deep expertise embedded in DIN standards. By choosing a DIN compliant valve, users align themselves with a tradition of German engineering excellence, known for precision and reliability.
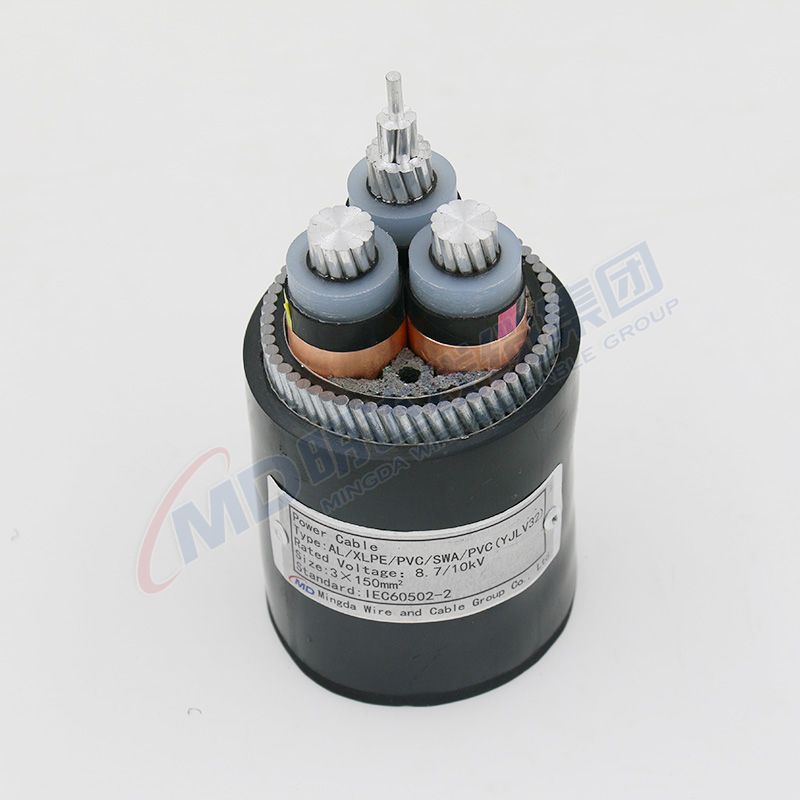
From an operational perspective,
the durability of metal seated gate valves cannot be overstated. Companies with experience in harsh environments emphasize the valves' long service life and reduced maintenance requirements compared to their soft-seated counterparts. The metal seats are highly resistant to abrasion, making them suitable for applications with particulate matter in the media.
din metal seat gate valve
Ensuring that the valve selections align with the exact requirements of the application is crucial. Experienced engineers recommend a thorough evaluation of the operating environment, taking into account factors such as pressure rating, temperature, and the nature of the fluid being controlled. The careful selection of materials, such as stainless steel, carbon steel, or specialty alloys, further empowers these valves to handle corrosive environments adeptly, thereby enhancing their authority and trustworthiness in critical applications.
The expertise of professionals in the manufacturing process of DIN metal seat gate valves is a testament to the quality and precision required for their application. Each valve undergoes rigorous testing to ensure it meets stringent industrial standards. Pressure tests, leakage tests, and operational tests simulate harsh conditions to validate performance, establishing a benchmark for trustworthiness.
For businesses looking to integrate these valves, it is crucial to partner with reputable manufacturers who provide comprehensive technical support and possess a track record of reliability. The after-sales support, including installation guidance and maintenance training, plays a significant role in optimizing the life span and performance of these valves, adding further value to the investment.
In conclusion, DIN metal seat gate valves stand out as a robust, efficient, and reliable choice for industries that demand uncompromised performance in challenging conditions. Their engineering excellence and proven history in critical industries make them an authoritative figure in fluid control solutions. By aligning with such high standards, businesses not only ensure operational integrity but also secure a trusted partner in achieving industrial excellence. As you evaluate your fluid handling needs, consider the unparalleled experience and expertise that come with DIN metal seat gate valves, and make a choice that stands the test of time and challenges.