In the nuanced realm of fluid control systems, the check valve with counterweight emerges as a pivotal component, serving both specialized industrial requirements and everyday applications. Its unique design not only addresses the sophisticated needs of various industries but also embodies engineering ingenuity by tackling the challenges inherent in fluid dynamics.
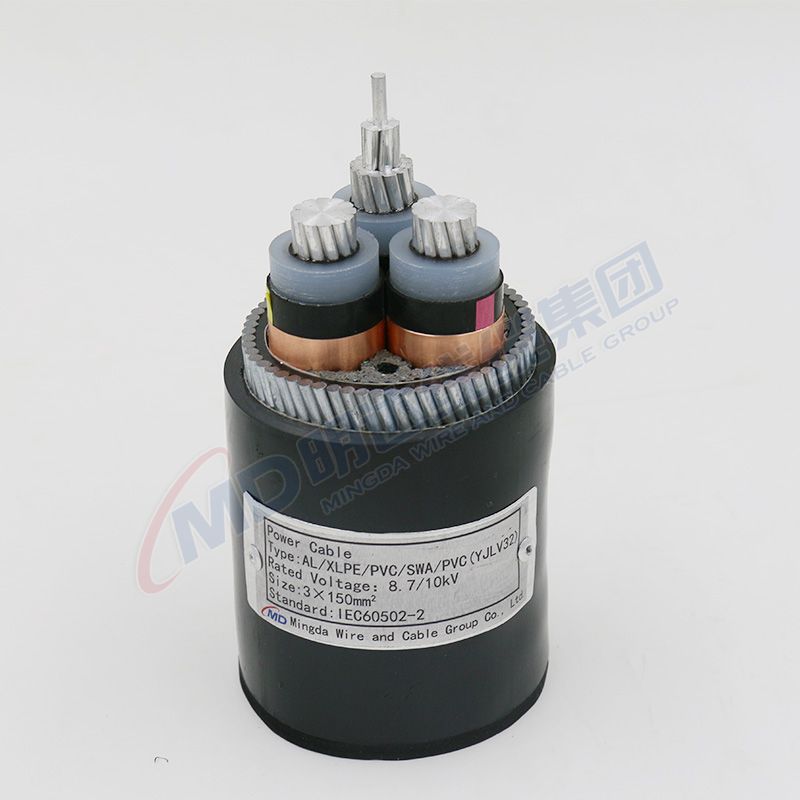
A check valve, at its core, functions as a one-way valve, ensuring unidirectional flow and preventing backflow which could potentially harm systems. The addition of a counterweight not only augments its utility but also imparts a greater degree of control over the flow characteristics. This ingenious modification makes the check valve with counterweight indispensable across numerous sectors, from wastewater management to oil and gas pipelines, each demanding reliable and robust solutions.
The expertise with which these valves are engineered reflects a deep understanding of both mechanical and hydrodynamic principles. Engineers meticulously design the counterweight to calibrate the valve’s response to flow changes. By doing so, they ensure that the valve opens and closes at precise intervals, minimizing water hammer and protecting sensitive components from shock and pressure spikes. This precision highlights not only the expertise involved in its creation but also the dedication to operational excellence.
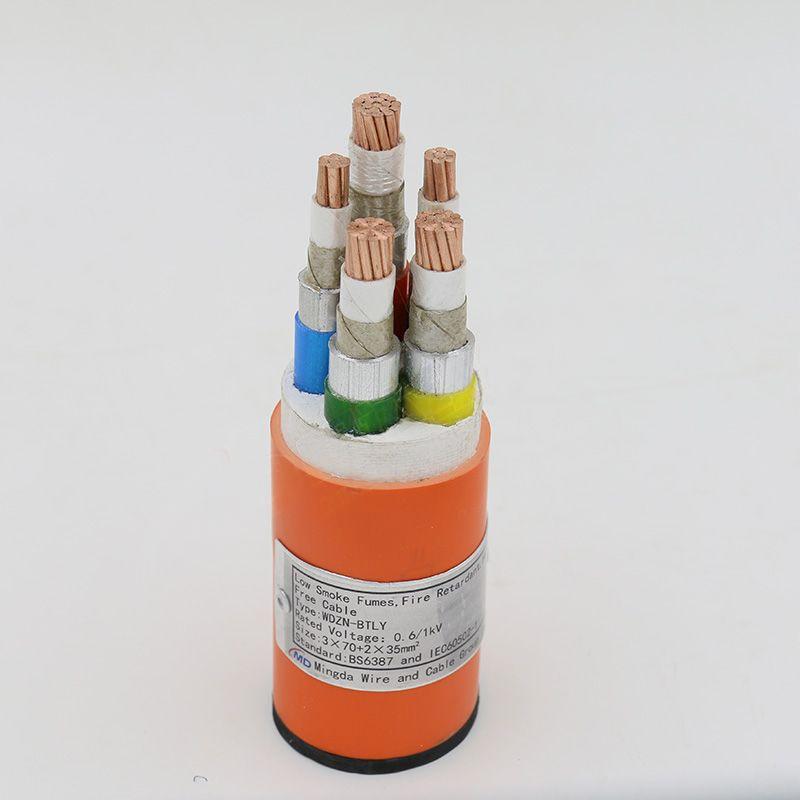
Furthermore, the check valve with counterweight achieves remarkable authority in fluid systems where variability and unpredictable flow conditions present significant hurdles. Its ability to endure tough conditions while maintaining optimal functionality elevates its status from a mere component to an authoritative solution in industrial settings. The robustness of its construction can withstand the test of time, often providing years of dependable service, thus marking its reliability.
In terms of experience, case studies consistently underscore the practical benefits of deploying check valves with counterweights in complex systems. One notable application is in the management of stormwater systems, where fluctuating flows due to weather conditions require adaptive responses. Here, these valves have demonstrated an exceptional ability to maintain system integrity, preventing backflow even in the face of significant pressure changes. As a result, their utilization not only ensures seamless operation but also mitigates environmental impacts, underscoring their ecological importance.
check valve with counterweight
Trustworthiness is another critical dimension of these valves, evident in the rigorous standards and certifications they meet. Many are compliant with international standards such as ISO for quality management, ensuring that users receive a product that not only meets but often exceeds stipulated requirements. This compliance serves as a testament to the manufacturers' commitment to delivering products that users can trust to safeguard their systems.
The penetration of check valves with counterweights into global markets further highlights their versatility and adaptability. They are embraced by industries worldwide, thanks to their ability to be tailored to specific needs, whether those are related to size, pressure, or environmental constraints. This adaptability significantly broadens their appeal and bolsters their authority in varied contexts.
Practical insights derived from field deployment provide a nuanced understanding of their advantages. Operators of large-scale irrigation systems have attested to the increased efficiency these valves bring, citing reduced energy requirements due to decreased resistance and improved system longevity. Such testimonials from seasoned professionals underline the real-world efficacy and reliability of these valves, driving further adoption and trust.
In summary, the check valve with counterweight is a quintessential example of how innovation, experience, expertise, and reliability converge in modern engineering. As industries continue to evolve, with demands for efficiency and sustainability at the forefront, the role of such specialized components is expected to grow, reinforcing their critical place in the landscape of fluid control systems. Their continued evolution signifies not just an adherence to traditional engineering principles but also a forward-looking approach to future challenges, ensuring that they remain an integral part of industrial infrastructures worldwide.