Check valves, often overlooked, play a pivotal role in countless applications across diverse industries. These unassuming components, designed to permit fluid flow in one direction while preventing backflow, are essential in maintaining system integrity and functionality. From domestic plumbing systems to high-stakes aerospace projects, understanding the intricacies of these valves is crucial for anyone involved in the selection, installation, and maintenance of fluid control systems.
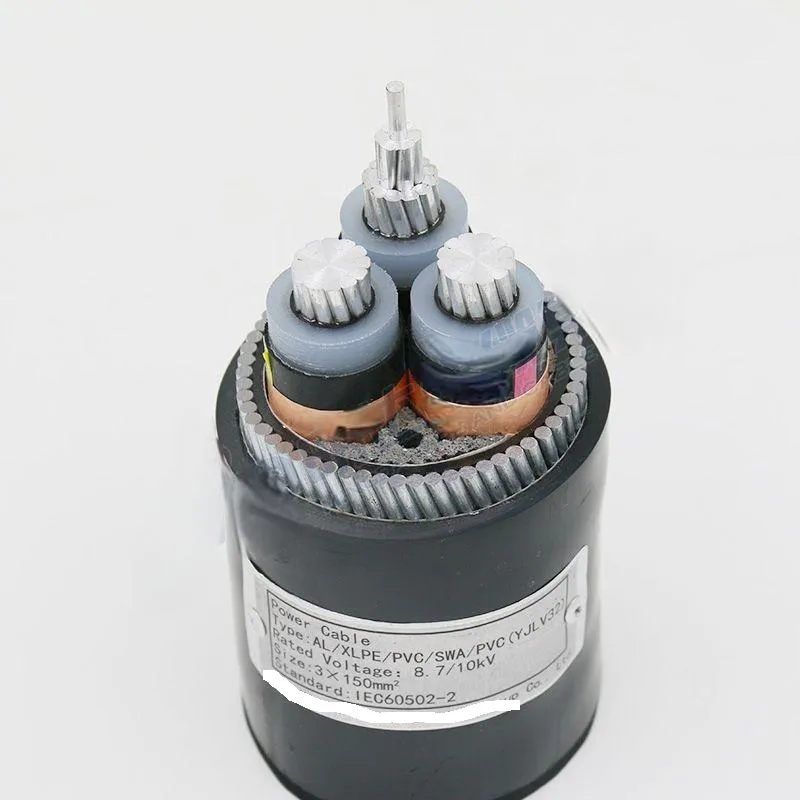
Experience and expertise underscore the effectiveness of check valves. Years of practical use have demonstrated that the right choice of valve type—be it swing, lift, disk, or double-door—impacts system performance significantly. For instance, swing check valves, with their simple operation, are highly effective in systems where gravity aids in the closure of the valve, thereby preventing flow reversal. On the other hand, lift check valves, requiring a more sophisticated mechanism, excel in applications demanding a tighter seal and higher pressure ratings.
The depth of expertise in selecting appropriate check valves comes from a comprehensive understanding of the materials suitable for different environments. Stainless steel, known for its corrosion resistance and strength, is often the go-to material in applications prone to harsh conditions or chemical exposure. Conversely, PVC valves offer a cost-effective solution for less demanding environments, ensuring efficiency without unnecessary expenditure.
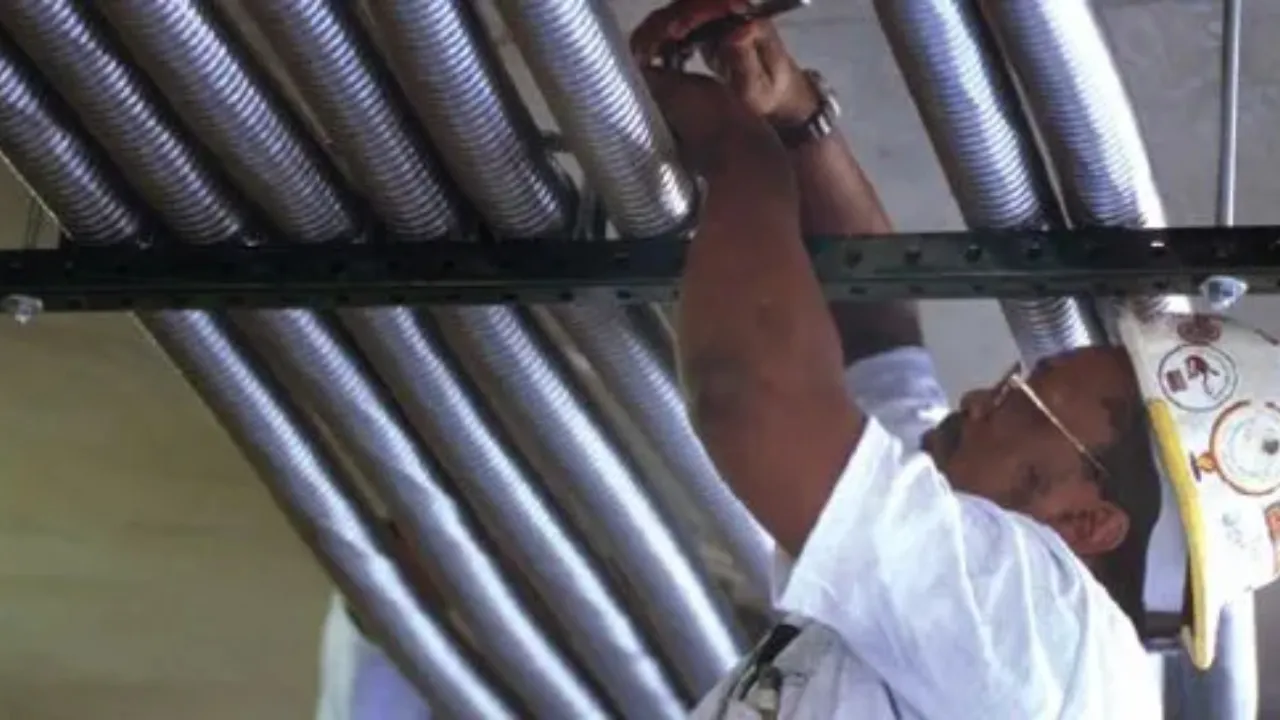
Authoritativeness in this domain is reinforced by leveraging insights from industry standards and guidelines, such as those from the American Society of Mechanical Engineers (ASME) and the International Organization for Standardization (ISO). Adhering to these standards ensures that the check valves are not only compliant but also reliable, minimizing the risk of failures that could lead to costly downtimes or hazardous leaks.
check valve
Trustworthiness in the realm of check valves is built through rigorous testing and quality assurance processes. Before reaching the end-user, each valve must undergo a series of tests to assess pressure tolerance, leak-tightness, and operational reliability. Manufacturers who are certified by recognized bodies, such as UL or CE, offer an added layer of assurance that their products have been evaluated against demanding safety and performance criteria.
For professionals in the industry, ongoing education and staying informed about the latest advancements in valve technology is paramount. Innovations such as smart valves, which integrate sensors and IoT capabilities for real-time monitoring, represent the forefront of check valve evolution. These smart systems provide invaluable data, offering insights into valve performance under various conditions and allowing for predictive maintenance that extends the lifecycle of the valves.
As applications for check valves expand, so too does the need for tailored solutions. Industries such as pharmaceuticals, food and beverage, and renewable energy each have unique requirements necessitating customized approaches to fluid control. For example, in food processing, valves must not only meet stringent hygiene standards but also ensure the smooth passage of viscous materials without compromising the system’s integrity.
In conclusion, the world of check valves is one characterized by a blend of tradition and innovation, with each valve designed to perform a specific task with precision and reliability. By integrating experience, expertise, authoritativeness, and trustworthiness, manufacturers and end-users alike can ensure optimal system performance and longevity. For those navigating the complexities of fluid dynamics, a thorough understanding of check valves is not just beneficial—it is indispensable.