In the realm of fluid control, the check valve plays an indispensable role. This unassuming device is engineered to permit unidirectional flow, thus preventing backflow which could potentially damage pipelines or equipment. In systems involving liquids or gases, the importance of check valves cannot be overstated; they are pivotal in maintaining operational efficiency and safety.
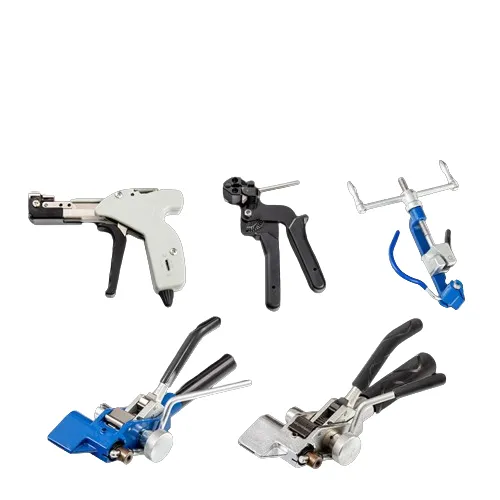
When selecting a check valve for any application, understanding its construction and functionality is paramount. Generally composed of plastic, metal, or composite materials, these valves are available in various designs, including swing, lift, and ball types.
Each variant offers distinct advantages, making it crucial to match the valve type with the specific requirements of the system. For instance, swing check valves are often preferred in systems that experience significant flow changes due to their ability to handle variations without frequent wear. Meanwhile, lift check valves are better suited for high-pressure environments due to their robust sealing capabilities.
Expertise in the application of check valves involves a comprehensive understanding of flow mechanics and system requirements. Factors such as the viscosity of the fluid, pressure changes, and potential for water hammer must be meticulously analyzed to select the appropriate valve. An inadequately sized or improperly chosen valve can lead to system inefficiencies, increased maintenance, and even catastrophic failure. Hence, consulting with engineers familiar with fluid dynamics is recommended to ensure optimal valve performance and longevity.
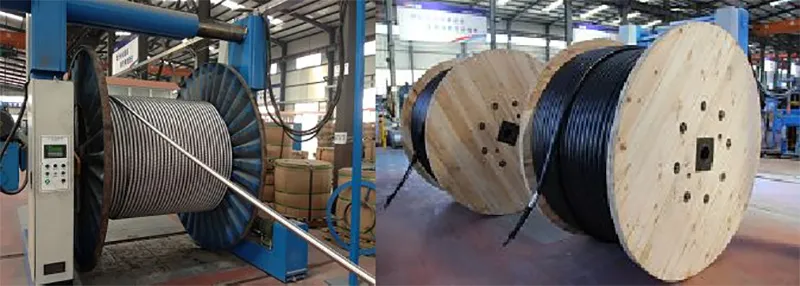
check valve
The authority of a check valve manufacturer plays a vital role in the reliability and durability of the product. Established manufacturers often have decades of experience in producing valves that comply with stringent industry standards. They typically offer extensive testing data and certification to verify the quality of their products. Moreover, these manufacturers provide warranties and after-sales support, reinforcing their commitment to product excellence. Investing in a valve from a reputable source not only enhances system reliability but also assures compliance with regulatory standards.
Trust in the application of check valves extends beyond product selection to encompass installation and maintenance practices. Proper installation by trained professionals avoids common pitfalls such as misalignment or excessive torque, which can compromise valve integrity. Regular maintenance is also crucial, involving routine inspections and prompt replacement of worn components to prevent leaks and ensure continued efficiency. Utilizing condition monitoring technologies can further augment trust by allowing for predictive maintenance, thus minimizing downtime and reducing operational costs.
In conclusion, the check valve is a critical component in the spectrum of fluid control systems, demanding careful consideration of design, quality, and maintenance to ensure functionality and safety. Professionals looking to optimize system performance should prioritize expertise in selection, authority in sourcing, and trustworthiness in installation and maintenance practices. Through these measures, systems will operate more efficiently, with reduced risk of failure and prolonged equipment lifespan, attesting to the invaluable role of check valves in industrial applications.