The unsung heroes in the world of fluid dynamics are often overlooked, yet their presence is vital across numerous industries. Check valves, a quintessential component in various systems, ensure the flawless operation of processes by allowing fluid to flow in a single direction. Through years of practical experience and expertise, it's clear that these devices offer more than meets the eye.
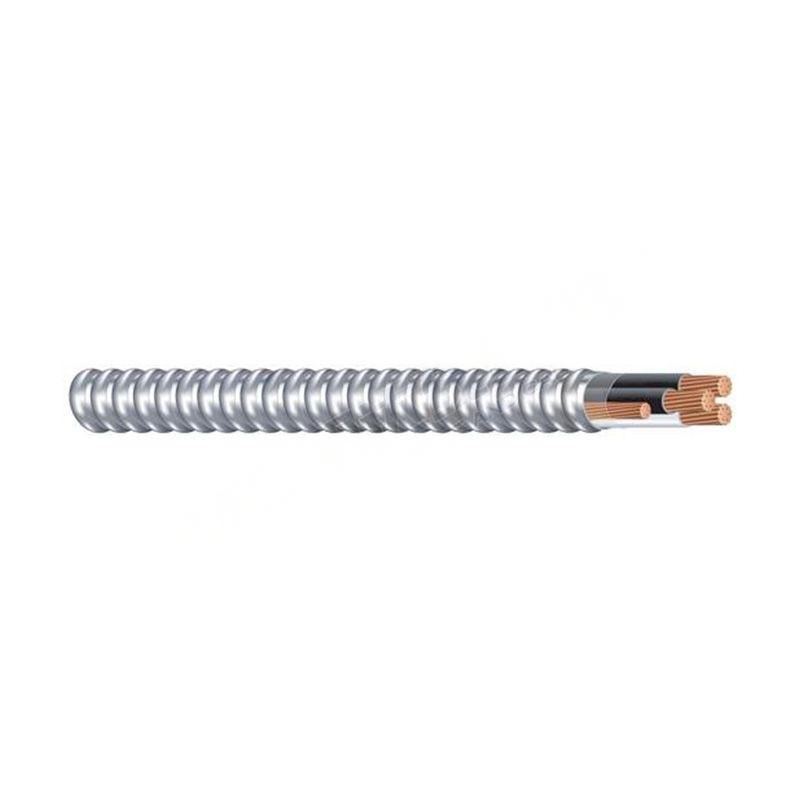
Renowned for their simplicity and efficiency, check valves work unobtrusively to prevent backflow, protecting piping systems from potential damage. Industries ranging from water treatment to oil and gas rely heavily on these devices. But why is their application so widespread, and what makes them an authoritative choice for various industries?
The fundamental principle behind check valves is their ability to respond automatically to differential pressure. When the pressure on the inlet side of the valve exceeds that of the outlet, the valve opens to allow flow. Conversely, when the pressure balance shifts,
the valve closes, safeguarding the integrity of the system. This responsive action forms the backbone of their operation, showcasing their adaptability across diverse operating conditions.

Among the many types of check valves, the swing check valve and the ball check valve are commonly used. Swing check valves, with their disc suspended on a hinge, are particularly suited for applications with minimal back pressure, such as wastewater management and HVAC systems. Their design allows for easy maintenance and low-pressure drop, enhancing their durability and reliability. Meanwhile, ball check valves use a spherical ball to block reverse flow, making them ideal for viscous fluids where a tight seal is essential, such as in chemical and food processing industries.
Years of engineering expertise have perfected check valve materials, providing solutions for the most demanding applications. Stainless steel, known for its corrosion resistance and high strength, is a preferred choice in harsh environments, such as marine pipelines and chemical plants. However, advanced composites and alloys are gaining traction, offering superior strength-to-weight ratios and exceptional durability at elevated temperatures.
check valve
Trust in check valves extends beyond their mechanical capabilities. Their installation simplicity and minimal maintenance requirements contribute to their widespread use. A well-chosen check valve not only extends the life of related components but also significantly reduces operational downtime, proving cost-effective and reliable for system operators.
Further augmenting their appeal, manufacturers continue to innovate, introducing features like noise reduction and water hammer mitigation, addressing common industry concerns. Incorporating these enhancements, the latest check valve designs boast an authoritative presence in both traditional and cutting-edge installations.
To ensure you select the right check valve, consider factors such as flow rate, pressure drop, and fluid characteristics. Collaborating with industry experts can be invaluable, providing insights tailored to your specific needs, reinforcing the valve's role in optimizing system performance.
In conclusion, check valves are a prime example of engineering simplicity coupling with industrial necessity. Their design not only addresses the fundamental need for one-way fluid control but also reinforces trust through consistent innovation and adaptability. Industries worldwide continue to endorse and implement these valves, recognizing their indispensable contribution to system efficiency and reliability. Evaluating and integrating the precise check valve enhances not only the system's integrity but also its potential for sustainable success.