When exploring the engineering marvels within the industrial sector, cast steel valves often stand out as essential components that combine durability, efficiency, and innovation. Renowned for their robustness and reliability, these valves are a pivotal part of numerous applications, playing a critical role in regulating the flow of fluids across various sectors including oil & gas, petrochemical, water treatment, and beyond.
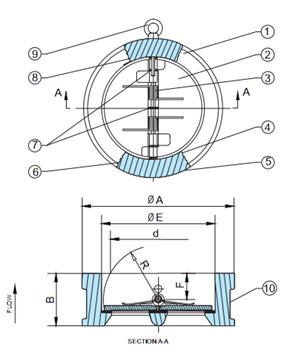
Crafted to endure the harshest of environments, cast steel valves are constructed using a process that involves the pouring of molten steel into molds, yielding superior strength and corrosion resistance. Such characteristics make them an optimal choice for operations where high pressure and extreme temperatures are prevalent. The cast steel's grain structure enhances the valve's mechanical properties, delivering unmatched performance in demanding situations.
From an engineering perspective,
the casting process offers significant advantages. By creating a uniform structure throughout the valve, it nullifies the risk of weak spots that can be detrimental in critical applications. Steel’s innate ability to resist deformation under strain further accentuates the valve's capacity to maintain integrity under heavy-duty operations. This translates into longer service life, reducing operational downtimes and maintenance costs.
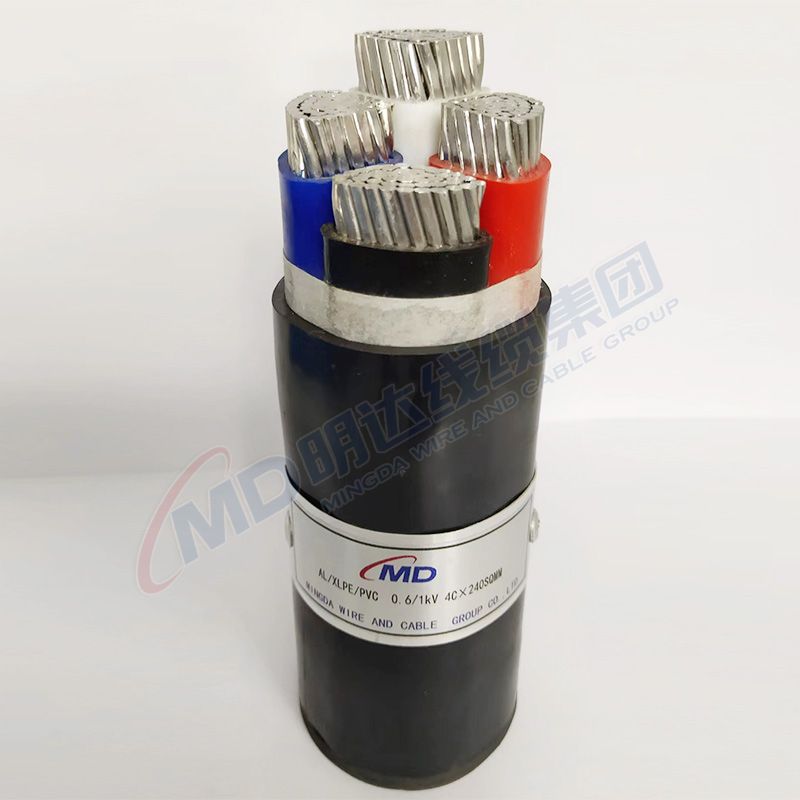
Professionals in industries that rely on these valves attest to their importance due to the peace of mind afforded by their reliability. The valve's operational precision ensures that fluid dynamics are controlled with exacting standards, safeguarding against the inefficiencies that can plague less robust systems. The adaptability of cast steel valves to accommodate various end configurations—be they flanged, threaded, or welded—extends their versatility, making them suitable for a multitude of installations.
The production of cast steel valves also aligns with stringent global standards, further reinforcing their credibility and authority in the market. Adhering to specifications such as API, ASTM, and ANSI not only ensures compliance with safety and quality benchmarks but also enhances trust with end-users. This convergence of expertise and adherence to authoritative measures is indispensable in sectors where the stakes are high and margin for error is minimal.
cast steel valve
Through an experiential lens, operators frequently highlight the ease of maintenance associated with cast steel valves. Their straightforward design allows for quick inspection and servicing without the need for complex tooling or extended downtimes. This accessibility underscores the design's focus on user-centric solutions, a factor that resonates well with both maintenance crews and operations managers keen on efficiency and productivity.
The market for cast steel valves is supported by manufacturers who are not merely suppliers but educators committed to disseminating knowledge about best practices and innovations. By hosting training sessions, webinars, and providing comprehensive resource materials, these companies position themselves as thought leaders, fostering an informed community of users who can maximize the potential of their valve systems.
Furthermore, sustainability considerations are increasingly being integrated into the lifecycle of cast steel valves. Manufacturers are optimizing production processes to reduce emissions, while also focusing on material recyclability. As industries globally pursue eco-friendly practices, such conscientious efforts elevate the trustworthiness of cast steel valves as solutions that contribute to sustainable development.
In conclusion, cast steel valves embody a fusion of experience, expertise, authoritativeness, and trustworthiness. They represent a pinnacle of engineering capability, offering robust solutions tailored to demanding industrial applications. As these industries continue to evolve, cast steel valves are expected to remain at the forefront, innovative and steadfast, delivering exemplary service grounded in time-tested strength and reliability.