In the ever-evolving world of industrial applications, selecting the right check valve is crucial for ensuring efficient and reliable system operations.
Cast steel check valves have emerged as a staple in various industrial sectors due to their robust construction and adaptable features. This article delves into the critical aspects of cast steel check valves, elucidating why they stand out and how they optimize industrial processes.
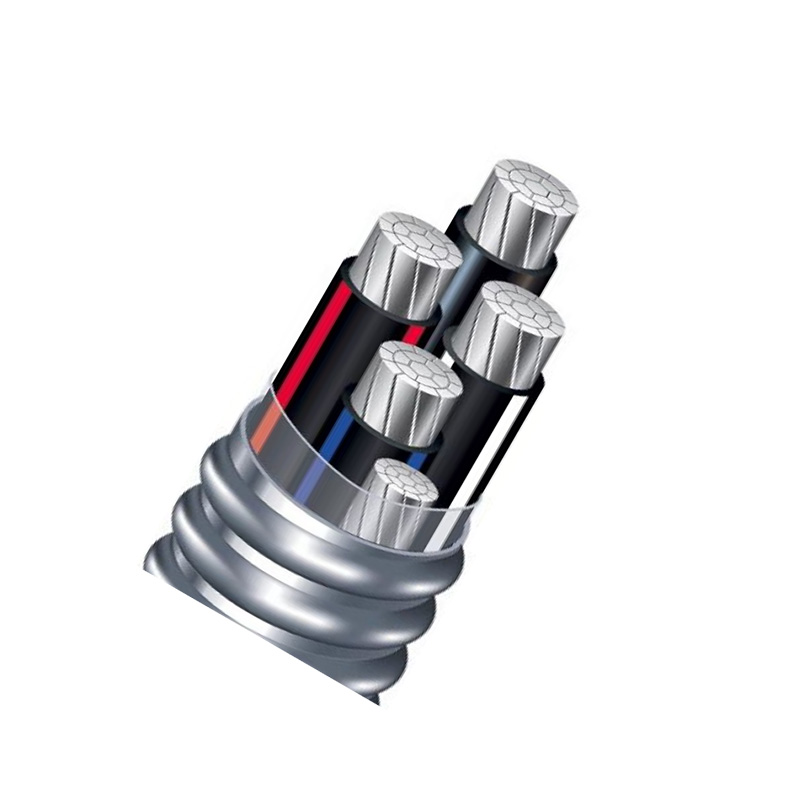
Known for their unparalleled strength and durability, cast steel check valves are specifically designed to handle high-pressure environments. These valves are constructed using high-quality steel, offering superior resistance to wear and tear, which is a significant advantage in processes involving corrosive or high-temperature substances. Industries such as oil and gas, petrochemicals, and power generation frequently utilize these valves owing to their resilience and longevity.
A pivotal factor contributing to the effectiveness of cast steel check valves is their ability to prevent backflow in piping systems. This prevention mechanism is crucial in safeguarding pipelines and machinery from potential damage caused by reverse flow. The valve opens automatically under pressure from the fluid on the inlet side, and once the pressure diminishes, it closes to prevent any unwanted return of fluid. This automatic response not only ensures the safety of operational processes but also optimizes performance by maintaining a unidirectional flow, thereby enhancing system efficiency.
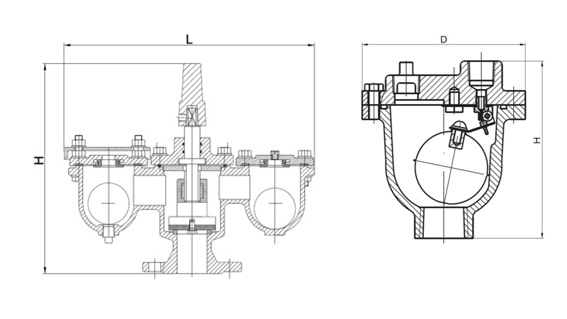
From a technical perspective, cast steel check valves are engineered with precision to meet specific operational requirements. They are available in various types, including swing check, lift check, and dual plate check valves, each suitable for different applications. For instance, swing check valves are preferred in systems where full flow or minimal restriction is necessary, while lift check valves are ideal where higher pressure drops are permissible. The varied options ensure that industries can select a valve that precisely fits their unique demands.
cast steel check valve
The expertise in designing these valves also lies in their adaptability to harsh environments. Their design incorporates features that withstand extreme pressures and temperatures, making them suitable for outdoor installations or under-the-sea operations. Advanced manufacturing techniques ensure that cast steel check valves maintain structural integrity even under severe mechanical stress, securing their status as a reliable choice for critical industrial processes.
Authoritativeness in the field of cast steel check valves is backed by rigorous testing and compliance with international standards. Reputable manufacturers subject these valves to stringent quality checks, including pressure testing, material composition analysis, and operational lifecycle tests, ensuring that they meet the highest benchmarks of quality and safety. Certifications from organizations such as the American Society of Mechanical Engineers (ASME) further attest to their reliability and performance.
Moreover, industry veterans trust cast steel check valves for their ease of maintenance and long service life. The simplicity in their design allows for straightforward installation and minimal maintenance interventions, a crucial factor in reducing downtime and operational costs. Their robust construction means fewer breakdowns, resulting in sustained productivity and lowered maintenance expenses over time.
In summary, cast steel check valves are a testament to engineering excellence and a critical asset in industrial settings. Their combination of durability, reliability, and efficiency, supported by expertise and stringent quality controls, makes them an essential component for numerous sectors. Choosing cast steel check valves not only means opting for a product with proven performance but also investing in a solution that champions operational efficiency and safety, hallmarks of a well-functioning industrial infrastructure.