Selecting the right casting ball valve for industrial applications is a decision that can significantly influence operational efficiency and safety. Drawing from extensive experience and expertise in the field of industrial valves, there are several critical aspects to consider that underscore both the production quality and performance of these pivotal components.
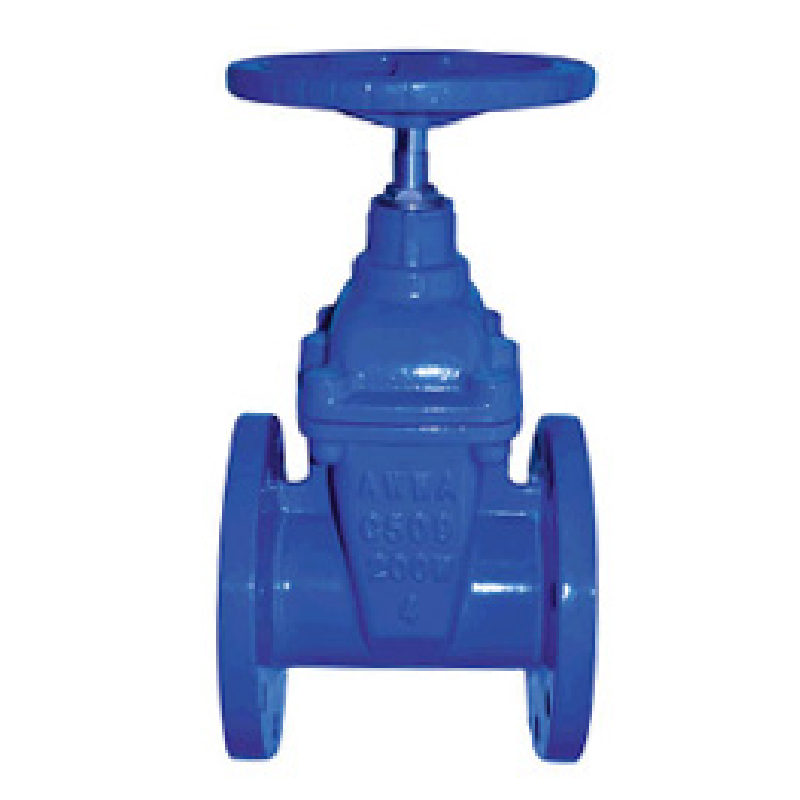
Casting ball valves are indispensable in industries ranging from petrochemical to water treatment, owing to their robustness and reliability in controlling fluid flow. These valves, typically constructed from durable materials like stainless steel or brass using a casting process, are designed to withstand high pressure and extreme temperatures, making them ideal for rigorous environments.
One of the key aspects of casting ball valve expertise is understanding the casting process itself. The casting method, whether it be sand casting or investment casting, influences the valve's mechanical properties and surface finish. Sand casting is often employed for larger valves where cost efficiency is a primary concern. However, for high precision and smoother finishes, investment casting is preferred, albeit at a higher cost. The choice of casting method affects not only the initial cost but also the lifespan and maintenance requirements of the valve.
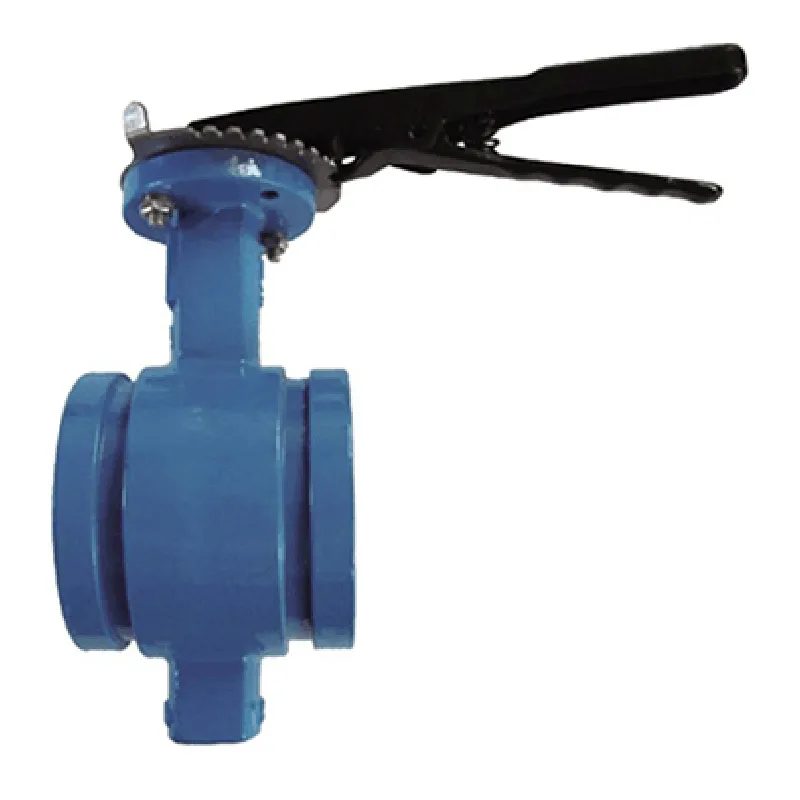
Additionally,
the design and construction of the ball valve are paramount. The precision in the spherical component — the ball — determines the valve's sealing efficiency and operational smoothness. High-precision manufacturing techniques ensure minimum friction and enhanced sealing, reducing wear and extending service life. Experts often recommend choosing valves with anti-static features and blow-out proof stems for added safety and reliability, especially in handling volatile or hazardous substances.
casting ball valve
Authoritativeness in the casting ball valve industry is frequently demonstrated by compliance with international standards. Reputable manufacturers adhere to standards such as API, ISO, and ANSI, which are benchmarks for quality and safety. These certifications are not merely bureaucratic hurdles but serve as a testament to the valve’s ability to perform under stated conditions. For industrial buyers, sourcing valves that meet these standards can significantly reduce the risk of operational failures and accidents.
Trustworthiness in a supplier is just as important as the technical specifications of the valve. Establishing a relationship with a reliable supplier involves evaluating their track record of delivery performance, after-sales support, and warranty offerings. A trustworthy supplier will provide detailed documentation, including maintenance guidelines and failure rate statistics, to instill confidence in their products.
Furthermore, real-world experience with casting ball valves highlights the importance of regular maintenance and inspection practices. Even the most robust valves can suffer from corrosion, sediment buildup, or mechanical wear. Proactive maintenance protocols can preempt costly downtimes and highlight potential issues before they escalate, thereby safeguarding operations and extending the equipment's lifespan.
In conclusion, when choosing a casting ball valve for industrial applications, one must consider the nuances of the casting process, adherence to industry standards, and the reliability of the supplier. Expertise in these areas can guide informed purchasing decisions that balance cost efficiency with operational reliability and safety. The intersection of these factors not only optimizes performance but also ensures that the valves serve their intended purpose with maximum efficacy, bolstering the overall productivity and safety of industrial processes.