In the competitive world of industrial applications, choosing the right components for fluid control systems is crucial for efficiency and safety. One such vital component is the butterfly valve with a gearbox, renowned for its robustness and precision in managing flow control. As a seasoned industry expert with years of experience, I can affirm the transformative impact that the correct choice in butterfly valves can have on your operations.
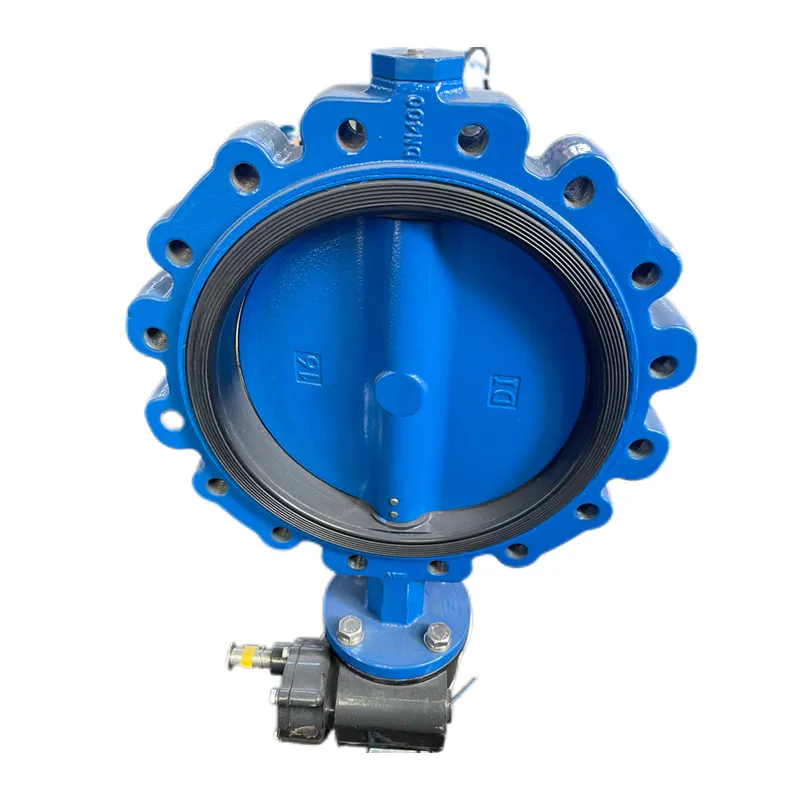
Butterfly valves, equipped with a gearbox, provide operators with precise control over fluid dynamics, crucial for industries such as oil and gas, water treatment, and chemical processing. The gearbox is a significant enhancement, allowing for easy manual operation even under high pressure or severe conditions by reducing the required torque to a manageable level. This makes it feasible to use larger diameter valves without the necessity of expensive actuation methods.
The integration of gearboxes into butterfly valves enhances their operational efficiency. Gearboxes serve to modulate the speed and twist of the valve stem, ensuring smooth and controlled open/close functions, and thus, maintaining steady flow rates. This aspect is particularly beneficial in process applications where consistency is paramount. Manual operation, facilitated by gearboxes, reduces the risk of mechanical failure since human oversight remains integral.
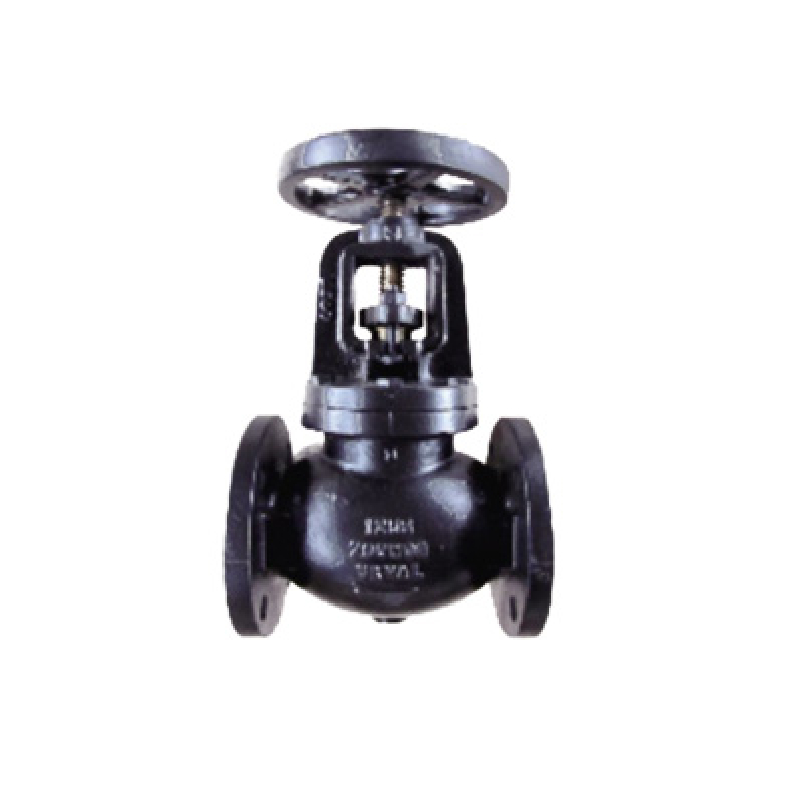
From an expertise standpoint, understanding the specifics of butterfly valve materials and construction is crucial. The typical design includes a disc mounted on a rotating shaft, positioned to provide a complete seal against two resilient valve seats. Designing valves with quality materials like stainless steel or ductile iron ensures durability and resistance to corrosion, particularly important in corrosive environments or with viscous media. Experts would recommend incorporating Teflon or rubber liner to ensure a tight seal and prolong the valve’s lifecycle.
butterfly valve with gear box
Authoritative insights suggest that selecting a valve should align precisely with the intended application environment. For instance, a valve used in a high-pressure steam line differs in construction from one handling potable water. An authoritative choice ensures maximum safety and avoids costly downtime due to leakage or failure. Consulting with manufacturers who provide documentation and testing reports can further solidify the decision-making process.
Building trust with suppliers and manufacturers cannot be overlooked. While purchasing, it is essential to thoroughly assess the supplier’s reputation, customer feedback, and post-purchase support. Many reputable manufacturers offer robust warranties and comprehensive after-sales services, implying their confidence in product quality and dedication to customer satisfaction. Trustworthy suppliers maintain transparency in their dealings, offering clear specifications and breakdowns of their products’ performance metrics.
Drawing from personal experience, I recall implementing a butterfly valve with a gearbox in a high-risk chemical plant operation. The concerns included dealing with aggressive chemicals and maintaining tight shut-off standards. The choice of a high-performance butterfly valve with an appropriate gearbox not only met safety standards but also improved maintenance efficiency. The easy-to-operate gear mechanism minimized the risk of operator error, and the valve’s quick, reliable response to control inputs translated into a smoother, safer process.
In conclusion, the selection of a butterfly valve with a gearbox should involve an immersive blend of experience, expertise, authoritative guidance, and supplier trustworthiness. By anchoring choices in these pillars, industrial applications can achieve optimal functionality and safety. Thus, in considering your next fluid control component purchase, reflect upon these facets to ensure you make an informed and beneficial decision, paving the way for enhanced operational success.