In the intricate world of fluid control systems, the butterfly valve emerges as a quintessential component, bridging functionality with innovation. Engineered to regulate the passage of fluids through a pipeline, its design offers an optimal blend of simplicity and efficiency. As industries across the globe seek reliable solutions, understanding the nuances of butterfly valves becomes imperative.
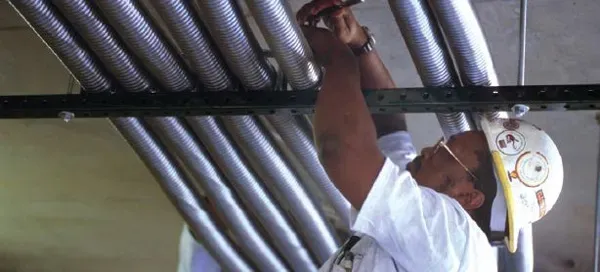
Butterfly valves are designed with a disc positioned at the center of the pipe, which rotates on a central axis. This disc, when turned, either permits or impedes the flow of the liquid or gas, making it a vital tool in a variety of applications, from water treatment facilities to power plants. One of the valve's standout features is its ability to provide a tight shut-off, even under high pressure and temperature conditions. This characteristic not only ensures safety but also maintains the integrity of the system.
The diversity in butterfly valve materials adds another layer of utility, allowing for customization according to specific needs. Common materials include stainless steel, cast iron, and PVC, each offering unique properties suitable for different environments. For instance, stainless steel is widely preferred in corrosive settings due to its resistance to rust and chemical damage. On the other hand, PVC is lightweight and cost-effective, often chosen for applications involving low-pressure systems.
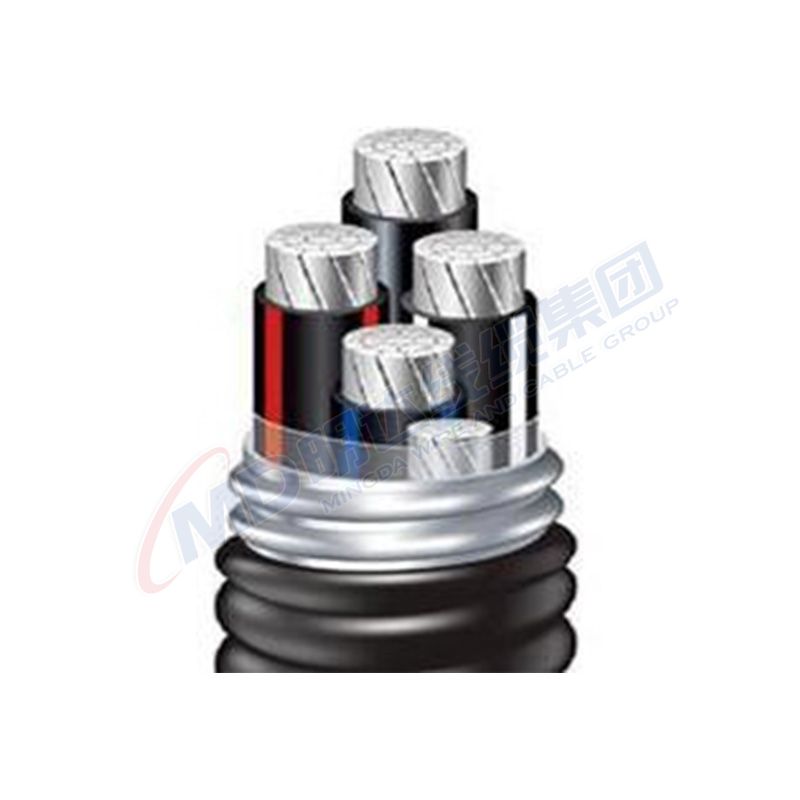
Advancements in technology have further expanded the capabilities of butterfly valves. The integration of automation systems enables precise control over fluid dynamics, significantly enhancing process efficiency. Automated butterfly valves can be operated remotely, streamlining operations and reducing manual intervention. This technological evolution not only lowers operational costs but also minimizes the risk of human error, thus elevating the trustworthiness of the system.
butterfly valve
The expertise required to select the appropriate butterfly valve cannot be overstated. It involves a comprehensive understanding of the operational environment, the nature of the fluids involved, and the specific requirements of the pipeline system. Collaborating with manufacturers who possess a strong track record and authority in valve technology ensures the deployment of a product that will perform optimally and durably over time.
Real-world experience with butterfly valves underscores their versatility. Industries have reported significant improvements in regulation precision and maintenance efficiency upon integrating these valves into their systems. For example, in the oil and gas sector, where pipeline integrity is paramount, butterfly valves have proven to be reliable components that withstand the rigors of a demanding environment. Users frequently commend their ability to withstand extreme conditions while delivering consistent performance.
Trust in butterfly valves also stems from adherence to industry standards and rigorous testing. Reputable manufacturers undertake extensive testing to ensure that their products meet or exceed established performance benchmarks. Certifications from recognized bodies further instill confidence, guaranteeing that the valves are built to withstand both current and unforeseen challenges.
In conclusion, the butterfly valve stands as a testament to the marriage of engineering precision and practical application. Its design simplicity, combined with advanced features, makes it an indispensable tool across myriad industries. It remains a preferred choice, not only for its cost-effectiveness but also for its ability to consistently deliver reliable results, thereby securing its place as a cornerstone in fluid control technology. With the continuous evolution in design and materials, the future of butterfly valves promises even greater innovations and efficiencies, positioning them as a critical asset in the industry’s pursuit of excellence in fluid management.