The ball valve flange type is a critical component in plumbing and industrial applications, revered for its unique ability to provide an exceptional seal combined with robust efficiency. As a cornerstone in the realm of fluid control, these valves are indispensable in systems where reliable shutoff and flow regulation are paramount. Understanding the ball valve flange type begins with appreciating its unique structural design and versatile application.
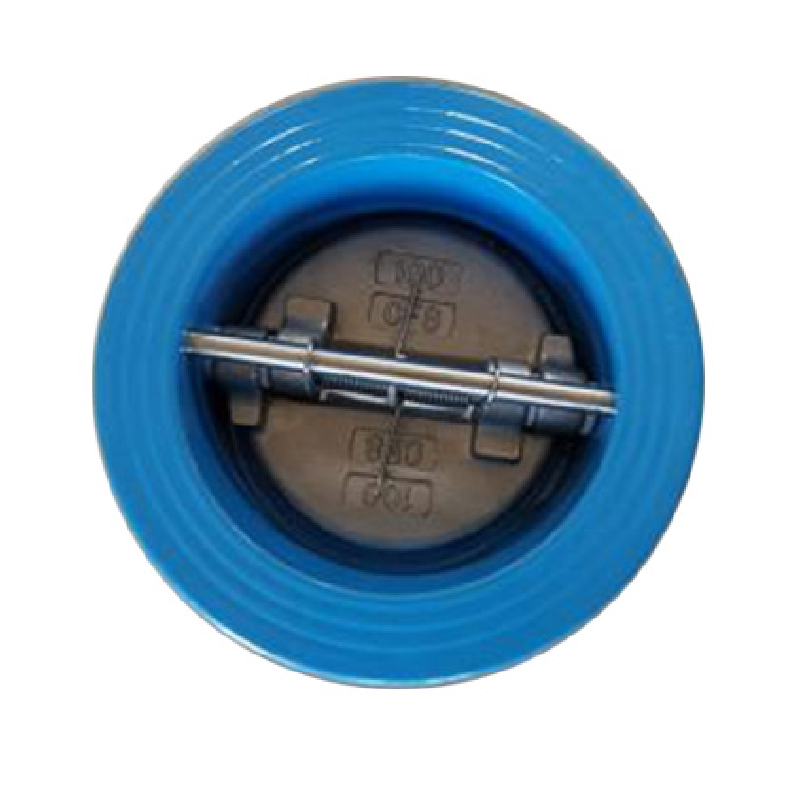
Ball valves are strategically designed with a rotatable perforated sphere (the ball) situated within the valve body. This sphere contains a bore that, when aligned with the pipe, allows fluid to flow freely. Conversely, when the bore is turned perpendicular to the pipe, flow is halted. The flange type in a ball valve refers specifically to the method of connecting the valve to the piping system. Flanged connections are preferred in many industries due to their durability and ease of maintenance; they allow the valve to be detached quickly for inspection or replacement without disrupting the entire system.
Expertise in the application of ball valve flange types is evident when considering the diversity of environments in which they operate. From high-pressure industrial systems to corrosive chemical plants, the robustness of these valves is unmatched. The flanged design enhances their reliability and safety, as the solid connection offers additional support to manage the stresses and strains experienced by the system. Moreover, they are made from a range of materials, including stainless steel, brass, and PVC, allowing them to be tailored for specific corrosive environments or pressure requirements.
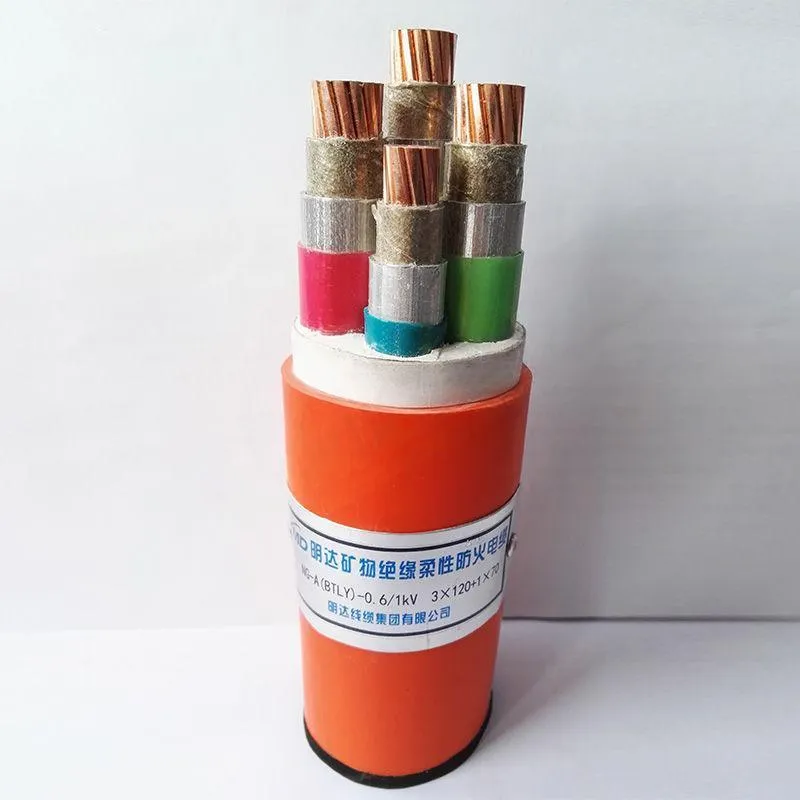
One significant advantage of the ball valve flange type is its capability to withstand extreme temperatures and pressures. In industries like oil and gas or power generation, where operational conditions can fluctuate drastically, having a valve that maintains its integrity without compromising on performance is critical. The flange connections not only support higher pressure ratings but also facilitate the accommodation of thermal expansions, essential in preventing system failures.
In terms of efficiency, ball valve flange types are renowned for their low torque requirement. This attribute enables them to be operated with less force compared to other valve types, reducing the risk of wear and tear during operation. Their exceptional durability translates to prolonged lifecycle and reduced maintenance costs, further enhancing their economic viability in large-scale operations.
ball valve flange type
Authoritativeness in discussing ball valve flange types also comes from understanding the standards and certifications that govern their usage. These valves often adhere to international standards such as ANSI, DIN, and ISO, reflecting their global acceptance and reliability. Compliance with these standards ensures that the valves meet stringent quality criteria, delivering peace of mind to operators and regulators alike.
Trust in the functionality and reliability of ball valve flange types is built on years of proven performance in countless applications. Many industries demand materials and components that are not only efficient but also reassuringly dependable - a testament to rigorous testing and longstanding experience in varied applications.
For those involved in the procurement or maintenance of fluid control systems, understanding the nuances of ball valve flange types is crucial. It involves considering factors such as pressure, temperature, and chemical compatibility, aligned with operational demands. Choosing the right valve design can significantly impact system efficiency, safety,
and longevity.
Ultimately, investing in quality ball valve flange types offers long-term benefits that surpass mere financial savings. With their durability, efficiency, and compliance with international standards, these valves stand as a key component driving the success of numerous industrial applications. As industries continue to evolve with technological advances and environmental considerations, the reliability of such a fundamental element remains undiminished, securing their place as a staple in the field of fluid management.