Selecting the right ball valve for your application can be a critical decision, particularly when dealing with a standard size like the 2-inch ball valve. This guide will provide an in-depth analysis and understanding of this key piece of equipment, emphasizing experience, expertise, authoritativeness, and trustworthiness.
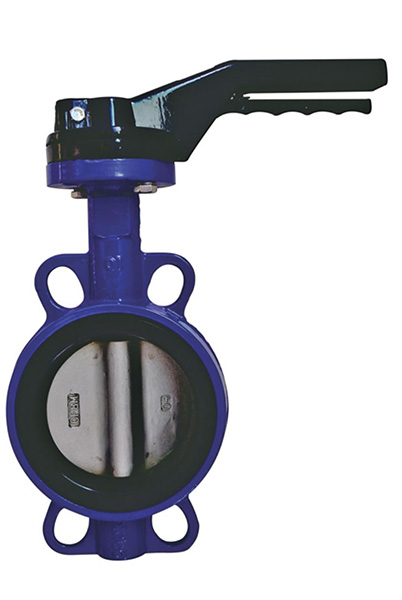
Ball valves, praised for their durability and reliability, are pivotal in controlling the flow of fluids in a wide array of industries. The 2-inch variant is especially popular due to its versatility and optimal size for medium flow systems. Typically used in sectors ranging from water treatment to oil and gas, its significance cannot be overstated.
An expert understanding of the 2-inch ball valve begins with its construction. These valves are usually crafted from robust materials such as stainless steel, brass, or PVC. Stainless steel is favored for its corrosion resistance and durability, making it ideal for challenging environments, like those involving corrosive fluids. Brass, on the other hand, offers a cost-effective alternative with decent performance for less demanding applications. PVC is utilized for non-chemical applications where lightweight and cost efficiency are priorities.
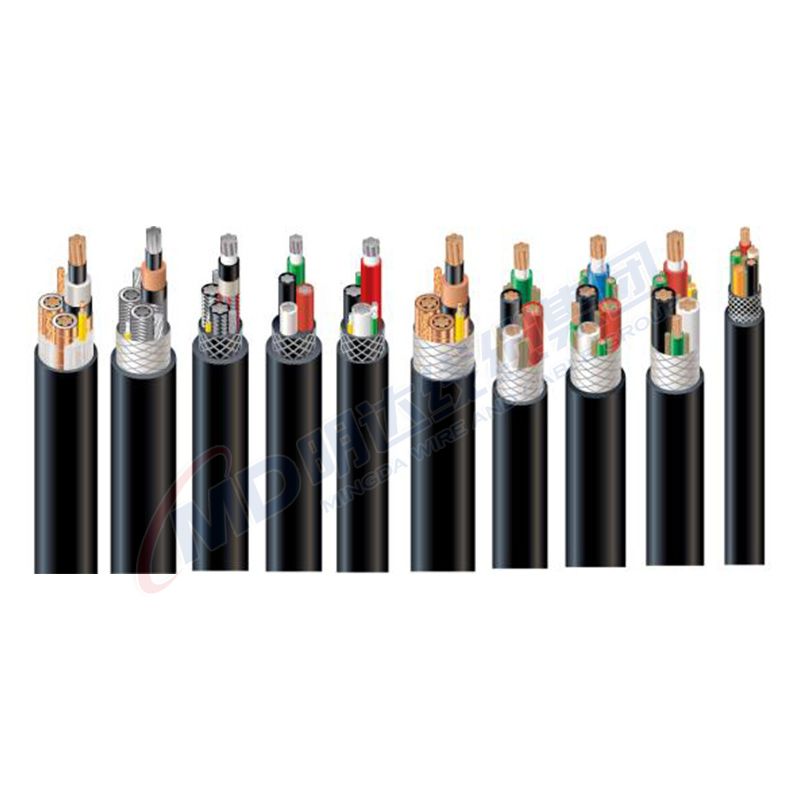
The operational mechanics of a ball valve are straightforward yet efficient. Inside the valve, a sphere (or ball) with a hole through its center pivots to allow or block flow. When the handle is turned a quarter turn, the hole aligns with the flow, enabling liquid or gas to pass. This simplicity, combined with a tight seal when closed, minimizes leakage and maintains system integrity, a reason for their widespread usage.
From an authoritative perspective, the selection of a 2-inch ball valve must consider the pressure ratings and temperature ranges it can withstand. Often rated around 1000 psi, these valves are suitable for a range of pressure requirements without compromising safety. Temperature resilience is equally critical; thus, it is crucial to ensure the selected material can handle the working temperatures to maintain operational efficacy and longevity.
ball valve 2 inch
The valve's lifecycle is another factor underlining its expertise. End-users must assess the valve's maintenance requirements and potential downtimes. A well-engineered 2-inch ball valve demands minimal maintenance due to its simple design and few moving parts. This aspect not only reduces operational costs but also enhances trustworthiness in industries where reliability is paramount, such as chemical manufacturing or energy production.
For enhanced experience optimization, installations should also consider the valve's end connections, which dictate installation costs and flexibility. Common end types include threaded, flanged, and welded. Threaded ends are cost-effective and easy to install and replace, while flanged ends provide added strength and are often preferred for higher pressure applications. Welded connections, though permanent, offer a leak-proof solution suitable for extreme conditions.
A real-world example underscores the importance of choosing the right 2-inch ball valve. In a notable scenario within the petrochemical industry, a company faced repeated downtimes due to valve failures. The oversight was traced back to using under-specified valves that could not withstand corrosive media and high pressures. By switching to stainless steel 2-inch ball valves with adequate pressure ratings, the firm enhanced its operational reliability, showcasing the product's trustworthiness and effectiveness when aptly chosen.
The expertise in 2-inch ball valves also extends to their actuation options. Manual valves are economical and sufficient for many operations; however, for automation needs, electric or pneumatic actuators can be integrated. Despite added costs, these actuators significantly enhance process efficiency and can be controlled remotely, proving invaluable in automation-focused industries.
In conclusion, understanding the multitude of factors influencing the selection and application of 2-inch ball valves is pivotal for leveraging their full potential. Employing such a valve that aligns with your specific requirements not only ensures system reliability and efficiency but also bolsters the credibility of your operations. As a result, companies can maintain seamless operations while mitigating risks associated with valve failures.