In the realm of fluid control systems, the ball check valve stands as a crucial component, renowned for its reliability and efficiency. This device, despite its seeming simplicity, plays a vital role in ensuring unidirectional flow in a wide array of applications, from plumbing systems to industrial pipelines. The ball check valve operates using a spherical ball inside a valve seat, allowing fluid to push the ball off the seat when flowing in the desired direction. When the fluid attempts to reverse, gravity and reverse flow force the ball back into the seat,
thereby sealing the passage.
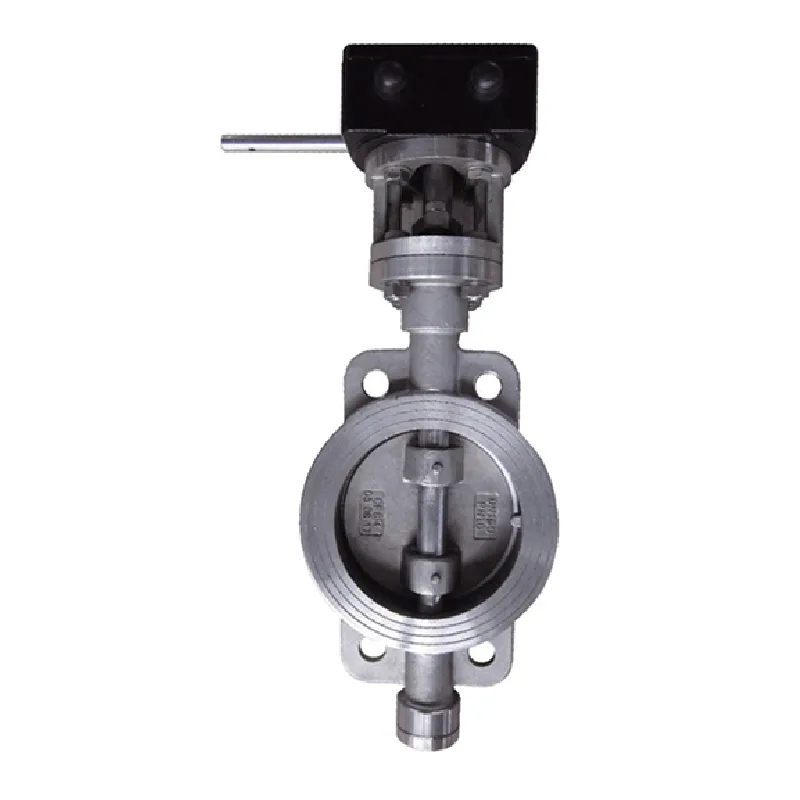
Experience showcases that the ball check valve is especially advantageous due to its relatively low maintenance compared to other types of valves. Designed to operate without the need for external control mechanisms, these valves reduce the chances of mechanical failure and are less susceptible to wear and tear. Users commonly report prolonged service life, even in demanding conditions, such as high-pressure or high-temperature environments. This longevity can be attributed to materials like stainless steel and PVC, which are often employed to construct ball check valves, enhancing their resistance to corrosion and thermal stress.
The expertise surrounding ball check valves extends to their functionality across various mediums, including gases, liquids, and semi-solids. In the oil and gas industry, for instance, these valves are critical for safety and efficiency, preventing backflow in drilling operations. Engineers in the field appreciate the straightforward installation process, which minimizes downtime and operational disruptions. Moreover, the capacity of these valves to perform in horizontal and vertical installations provides a versatile solution that can adapt to spatial constraints and specific project demands.
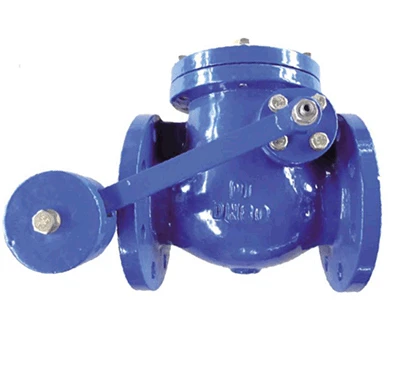
In authoritative engineering texts, ball check valves are often cited for their cost-effective performance. They deliver excellent return on investment, especially in large scale operations where operational reliability can mitigate risks of system failures. Industry leaders who rely on continuous operations, such as water treatment facilities and chemical plants, emphasize the importance of incorporating these valves into their fluid handling solutions. Their simple yet robust design minimizes potential points of failure, translating to fewer unplanned maintenance activities and thus lower operational costs over time.
ball check valve
Trustworthiness is further reinforced by the industry standards that ball check valves adhere to. Reputable manufacturers ensure these valves meet rigorous quality controls, often exceeding performance benchmarks set by international standards organizations like ISO and ANSI. Testing for pressure, temperature resistance, and leak-tightness is performed to guarantee that each unit can reliably perform its intended function under specified conditions. Certifications and compliance statements from third-party evaluators add an additional layer of confidence for both buyers and operators.
Real-world case studies frequently highlight the dependability of ball check valves in critical applications. For example, municipal water systems have demonstrated improved efficiency and reduced instances of backflow contamination with the integration of these valves. Similarly, in pharmaceuticals, maintaining sterile conditions is paramount, and using valves that promise unidirectional flow helps maintain system integrity and product purity.
The ball check valve's design, operational benefits, and proven track record across industries underscore its standing as an essential component in fluid control systems. Professionals and industries aiming to optimize their operational efficiency will find investing in high-quality ball check valves a prudent choice, not only for their durability and performance but also for the peace of mind they bring in critical applications.