Air valves, an essential component in numerous industrial and domestic applications, play a critical role in maintaining system efficiency. Through firsthand expertise, it becomes apparent that an understanding of air valves can greatly enhance operational excellence and knowledge in their application.
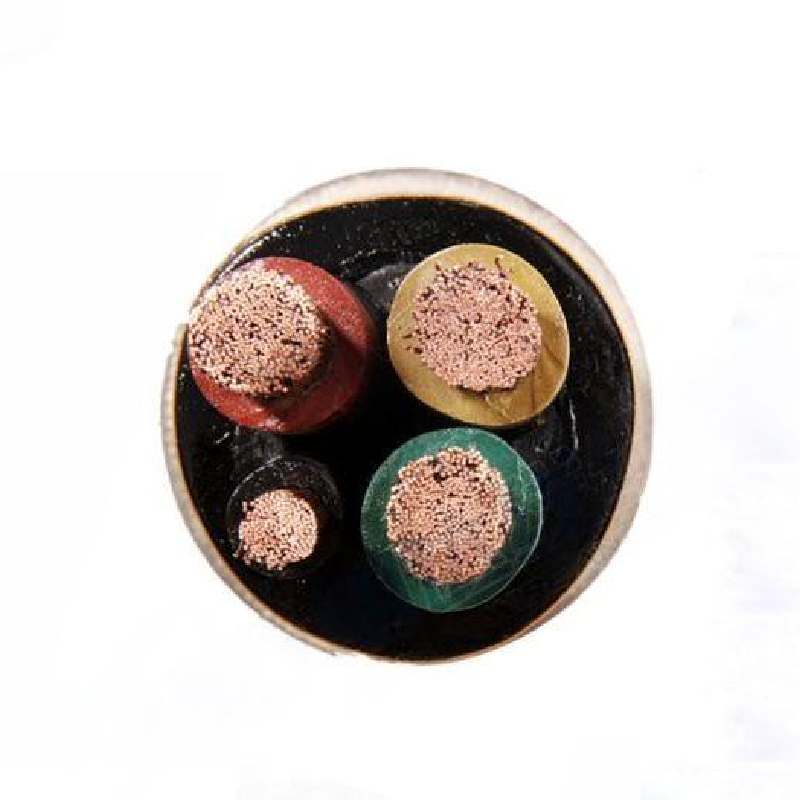
Air valves are primarily tasked with regulating, directing, and controlling the flow of air within various systems. They achieve this by allowing air to enter and escape, thereby maintaining atmospheric pressure and preventing the collapse of structures, particularly in pipeline systems. With hands-on experience in implementations, the importance of air valves can be critically examined in both indoor and outdoor systems, such as irrigation, water supply, HVAC systems, and pneumatic lines.
An air valve's functionality is deeply rooted in its design and specification. Expertise shows that each type, be it automatic, dual-function, or combination air valves, is uniquely suited for specific tasks. Automatic air valves are pivotal in continually releasing trapped air during system operation, thereby eliminating air pockets. Systems can thereby reduce the potential threat of air locking and improve overall mechanical efficiency. Dual-function air valves, on the other hand, not only discharge air from within pipelines during filling operations but also allow air to re-enter amid draining. Combination air valves bring together the best of both functionalities, ensuring comprehensive pressure control in complex operations.
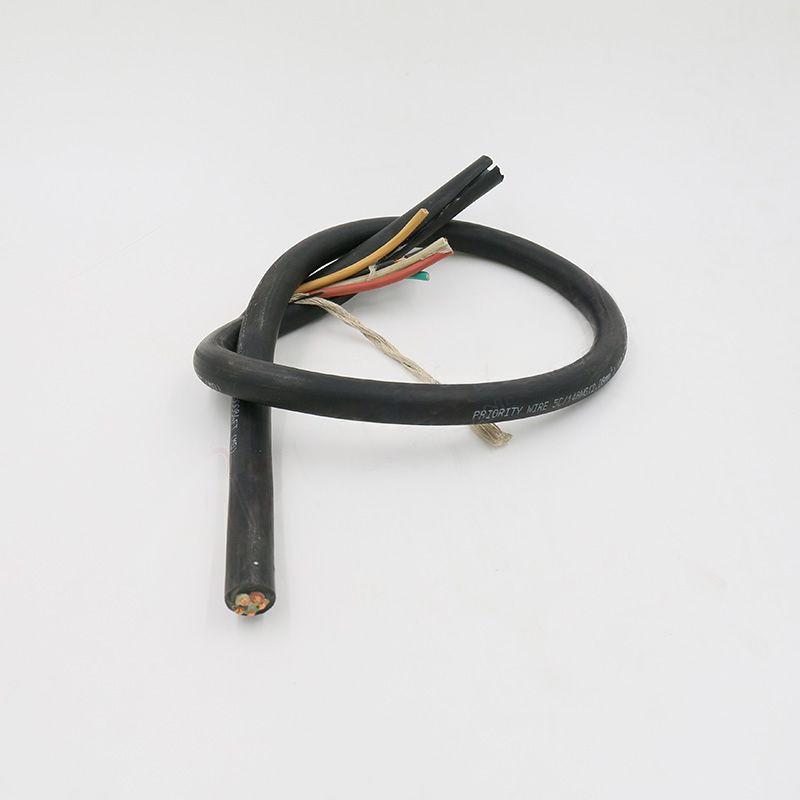
In-depth knowledge of material science is essential in selecting air valves because they come in varied materials like stainless steel, brass, and PVC.
Material selection directly impacts valve longevity and functionality, especially in corrosive environments. For example, in water treatment plants where chemical reactions are prevalent, stainless steel air valves are preferable due to their corrosion resistance and durability.
Expertise in installation and maintenance is equally important. Proper sizing and placement of air valves can significantly curtail energy consumption and prevent potential hazards like pipeline bursts. Inadequately sized valves or incorrect placements can result in inefficient air release, thereby escalating operational costs. Hence, it’s authoritative knowledge in the field that drives the seamless installation of such valves, offering maximized energy efficiency.
air valve
Genuine hands-on experience confirms that the life-cycle maintenance of air valves can also affect operational trustworthiness. Regular inspection and timely maintenance ensure they function optimally, significantly reducing downtimes in industrial setups. Trusted operational protocols advocate for routine checks which involve cleaning debris, checking for leakage, and lubricating mechanical components of the valve.
The safety implications of air valves cannot be understated. In high-pressure systems, their ability to regulate air greatly reduces the risk of accidental discharge or pressure overload. This authoritative stance is reinforced by rigorous industry standards and certifications that air valves must adhere to, ensuring conformity and safety compliance.
The integration of air valves in smart, IoT-enabled systems marks a new frontier in operational efficiency. Advanced solutions allow for remote monitoring and automated adjustments of valve operations, further enhancing reliability and performance in real-time.
In conclusion, with a nuanced grasp of technology and through learned expertise, air valves are critical components that bring both performance and protection to various systems. Their ability to regulate air flow and maintain pressure balance is pivotal to the functionality and safety of modern engineering applications. By adhering to industry standards and employing innovative solutions, air valves continue to support sustainable operational environments, reflecting their indispensable presence across industries.