Air valves are the unsung heroes of fluid and gas systems, often overlooked yet critically important. For individuals and businesses aiming to maximize the efficiency and longevity of their systems, understanding the integral role and selection criteria of air valves is vital. This guide provides expertise on the types, functionalities, applications, and maintenance of air valves, ensuring you make informed decisions backed by authority and trust.
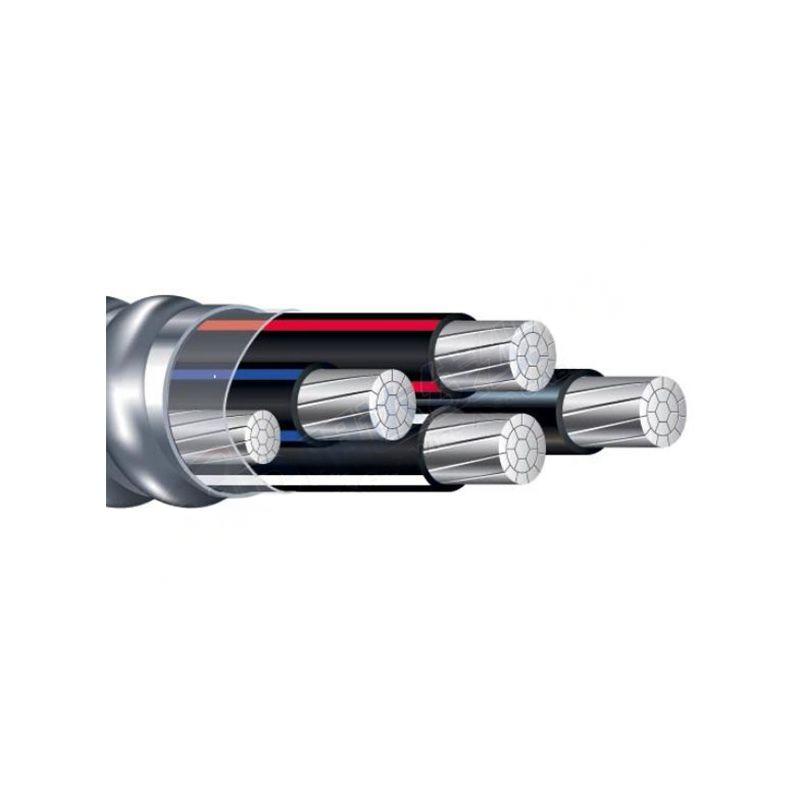
Air valves, designed to release unwanted air from pipelines in water supply systems, improve the efficiency and safety of systems by minimizing surge pressures and maintaining optimal flow. Their operational excellence can be likened to an experienced conductor orchestrating a symphony, where each note must be flawless to achieve harmony. Air valves achieve this by venting trapped air during both filling and operating stages and allowing air to re-enter when the system is drained, preventing vacuum conditions.
Among the different types, air release valves are particularly essential in high points of a pipeline where air accumulation is highest. Their primary purpose is to release small quantities of air that may collect during pipeline operation.
Meanwhile, air/vacuum valves serve a dual purpose. During draining, they admit large quantities of air, preventing atmospheric pressure from collapsing the structure. Combination air valves are hybrids that serve both aforementioned roles, emphasizing versatility in various operational scenarios.
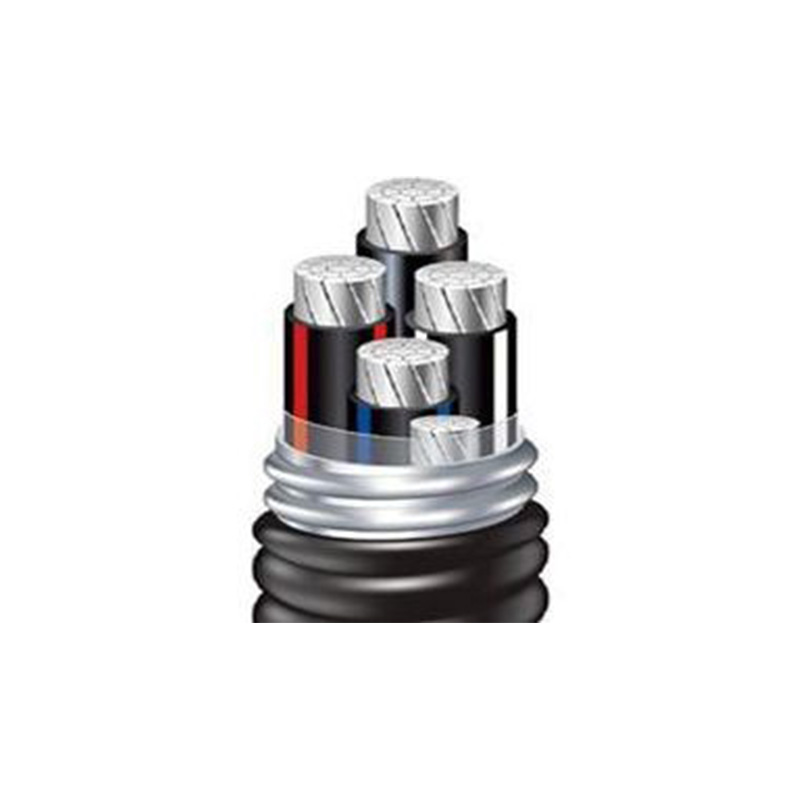
Selecting the appropriate air valve mandates a nuanced understanding of your system's specific needs. A selection should consider the fluid type, pipeline material, operating pressure, and the system's geographical layout. For instance, systems experiencing frequent troublesome air trapping would benefit significantly from a combination air valve rather than just a singular air release valve.
Installation is another critical factor influencing an air valve's performance. Proper installation, conforming to the manufacturer’s guidelines, ensures efficient operation. It’s crucial for the valves to be easily accessible for routine inspection and maintenance. In cases of elevated terrains or significant altitude variations, multiple air valves should be installed strategically to mitigate air locking.
air valve
From a maintenance perspective, regular inspections are non-negotiable. Even the most reliable air valves can succumb to wear and tear due to harsh environmental factors and routine operation stress. Meticulous maintenance schedules should be adhered to, examining for debris build-up, corrosion, and mechanical damage. This underscores the trustworthiness of a system, as any valve neglect can lead to system inefficiencies or catastrophic failures.
Air valves have evolved technologically, embracing smart solutions like sensors that provide real-time data on valve performance. This innovation enhances both reliability and proactive maintenance, ideally suited for complex and extensive systems that are challenging to monitor manually.
In industries where water and fluid dynamics are pivotal – such as irrigation, wastewater management, and industrial pipelines – air valves are indispensable in guaranteeing operational integrity and extending system lifespan. Their impact on safety and efficiency cannot be understated as they protect against the destructive forces of pressure surges and vapor lock conditions.
In conclusion, understanding the pivotal role and functionalities of air valves, grounded in technical expertise and empirical evidence, empowers consumers and professionals to implement systems that are both authoritative and reliable. Opt for air valves with mindful consideration of factors like type, application, installation, and maintenance to ensure your fluid systems operate at peak performance, a crucial component in maintaining an edge in today’s fast-paced industry landscape.