Air pressure control valves are a crucial component in a myriad of industries, playing an essential role in the regulation of pneumatic systems. Understanding their function and benefits, and knowing how to select the right one for specific applications, can make a significant difference in efficiency and operational success.
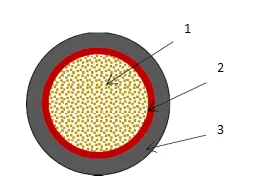
Air pressure control valves are designed to maintain constant downstream pressure across a wide range of flow conditions. By regulating the pressure, they ensure that machinery and equipment operate smoothly, safely, and efficiently. The controlled pressure is essential for protecting equipment from damage due to overpressure and optimizing performance by maintaining the desired pressure levels set by the operator.
These valves come in various forms, such as direct-operated, pilot-operated, and electronic pressure control valves, each suitable for different applications and levels of precision. Direct-operated valves are simpler and ideal for lower flow rates and less precise control. In contrast, pilot-operated valves provide more exact control for higher flow rates, making them suitable for industrial applications where precision is crucial. Meanwhile, electronic control valves offer even higher precision and adjustability, powered by digital technology and remote operation capabilities.
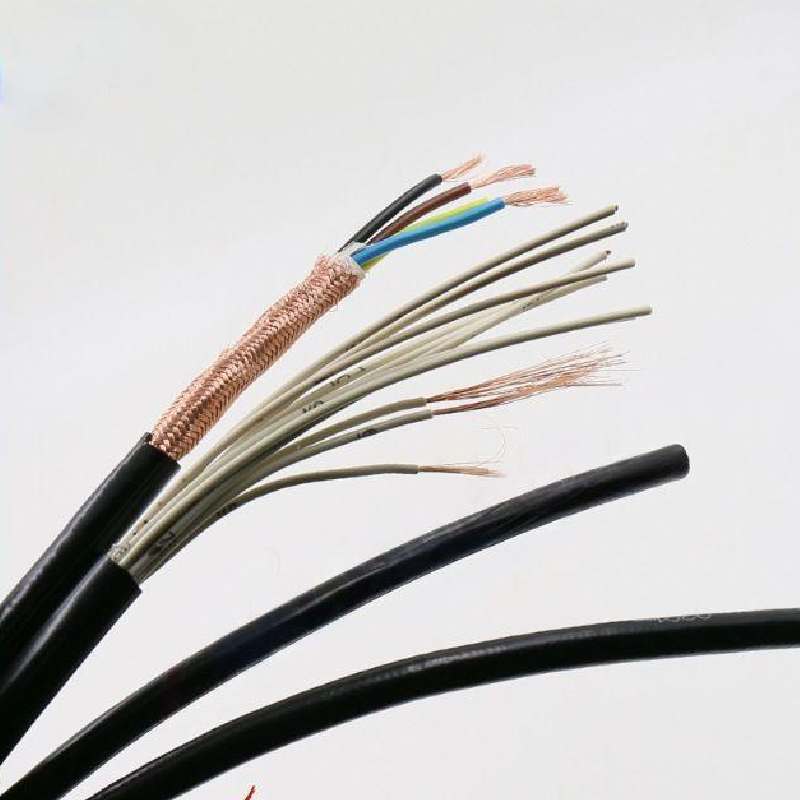
Expert insight is invaluable when dealing with air pressure control valves, especially when high precision and reliability cannot be compromised. When choosing a valve, consider factors such as the required flow rate, pressure range, fluid compatibility, and environmental conditions. The material of the valve is equally important; for instance, brass valves are common due to their good balance of durability and cost, while stainless steel is preferred in corrosive environments.
Real-world experience has shown that periodic maintenance is essential to ensure the longevity and efficiency of these valves. Over time, wear and tear can affect the valve's performance, leading to leaks and inconsistent pressure maintenance. Regular inspections should focus on checking for signs of corrosion, physical damage, or any obstructions that might impair the valve's function. Utilizing advanced diagnostics tools can further augment this maintenance routine, providing insights into the valve's performance and highlighting areas needing attention before they lead to significant issues.
air pressure control valve
Incorporating the latest technology in valve design and function can dramatically enhance performance. For instance, the advent of IoT has allowed for smart air pressure control valves that offer real-time data monitoring and feedback. These smart valves can predict potential failures and notify operators, thus averting downtime and efficiency loss. Additionally, they allow for better integration into automated systems, reducing human error and optimizing operations.
Industry specialists advocate for investing in high-quality air pressure control valves as an economical solution to long-term operational costs. While the initial cost might be higher, the reduction in maintenance costs, increased lifespan, and energy savings significantly outweigh the initial investment. High-quality valves not only improve process efficiency but also provide assurance in safety and compliance with industrial standards.
Building trust and credibility in the selection and use of air pressure control valves can be achieved by choosing reputable manufacturers and suppliers. Brands that have proven track records in innovation, quality, and customer support are preferable. Additionally, taking advantage of customer reviews and testimonials can provide insights into the real-world application effectiveness of a particular valve type or brand, further guiding purchasing decisions.
In summary, the understanding and management of air pressure control valves require a combination of expertise, real-life experience, and a commitment to maintaining the highest standards. Selecting the right valve involves a comprehensive assessment of operational needs and environmental factors, while ongoing maintenance and embracing technological advancements ensure maximum performance and longevity. By focusing on quality, trust, and authority, companies can maximize the benefits these essential components provide to their pneumatic systems, ultimately leading to cost savings, enhanced safety, and increased operational efficiency.