Actuated valves, revered for their precision and reliability, play an indispensable role in modern industrial applications. These automated devices control the flow, direction, or pressure of liquids, gases, or slurries in a system, and their integration constitutes a pivotal aspect of fluid systems engineering. The prowess of actuated valves is highlighted in their ability to serve various industries, from oil and gas to water treatment and pharmaceuticals.
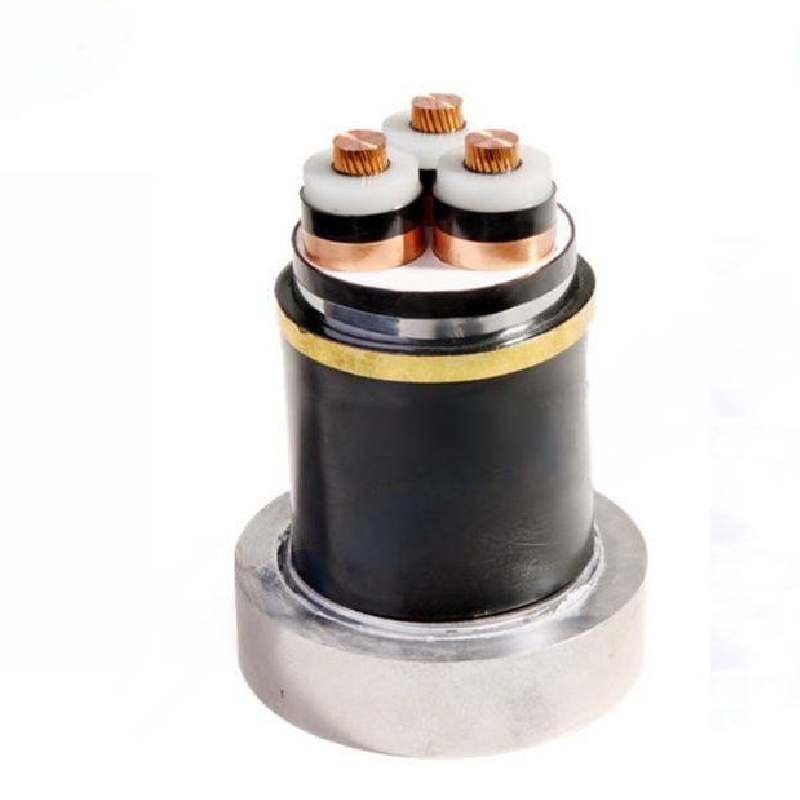
The construction of an actuated valve seamlessly combines mechanical engineering innovation with cutting-edge electronic advancements. These valves are typically classified based on the types of actuators employed, which include electric, pneumatic, and hydraulic systems.
Each actuation method offers unique benefits tailored for specific operational demands. For instance, electric actuated valves provide superior control and are favored in applications where precision is paramount, making them ideal for processes that require accurate flow regulation.
Expertise in the selection of actuated valves is paramount to ensure operational efficiency and cost-effectiveness. Engineers must consider a plethora of factors such as the medium being controlled, required flow rate, operational environment, and compatibility with existing system architectures. The expertise extends to understanding the nuances of valve materials—given that they can range from stainless steel to more exotic alloys like Hastelloy, each offering varying degrees of resistance to corrosion and temperature fluctuations. This knowledge facilitates the selection of appropriate valves that cater to specific operational conditions, ultimately enhancing longevity and performance.
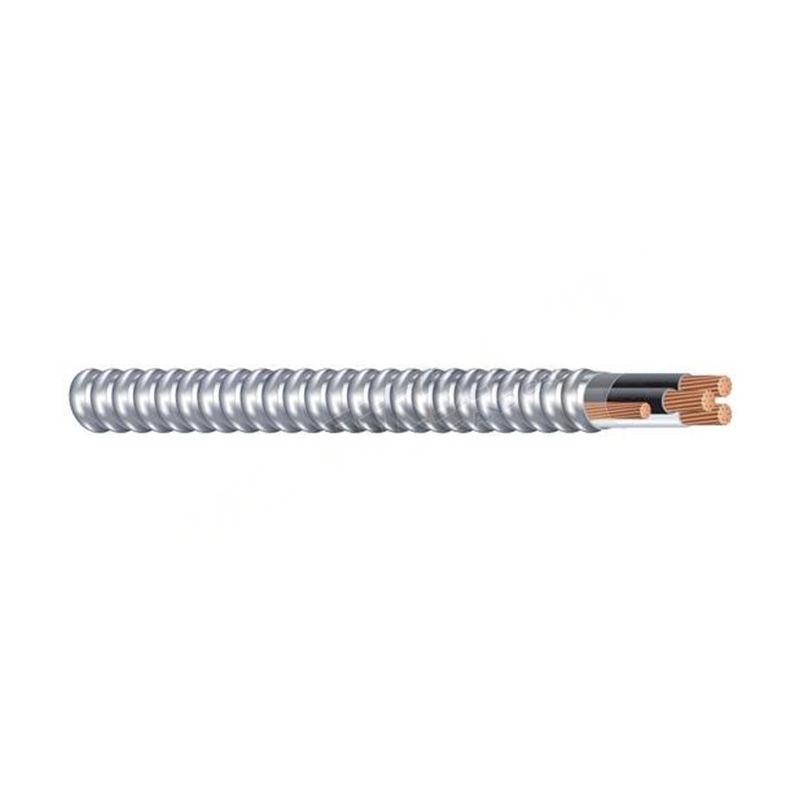
Experience in deploying actuated valves also encompasses knowledge of their installation, calibration, and maintenance. Proper installation is crucial to avoid leaks, which can lead to costly downtimes and safety hazards in sensitive industries. Regular maintenance checks and recalibration of the valve actuators are essential practices that ensure their optimal operation and extend their service life. Seasoned professionals understand the importance of predictive maintenance, which relies on real-time data analytics to foresee potential failures, thereby minimizing unexpected shutdowns.
actuated valve
Authoritativeness in the domain of actuated valves is often embodied by industry standards and certification. Compliance with international standards such as ISO, API, and ASME signifies the reliability and safety of these components. Leading manufacturers often collaborate with regulatory bodies to contribute towards developing and refining such standards, reinforcing their authority in the market. By adhering to these certifications, companies not only ensure product quality but also enhance their reputation in the global market.
Trustworthiness in actuated valve operations is intrinsic and can dictate the operational success of entire systems. The reliability of actuated valves reflects directly on the overall trust in the systems they control. Establishing trust is multi-faceted, involving transparent communication with stakeholders, end-users reporting consistently positive experiences, and leveraging customer feedback for continuous improvement. Trust is also built through extensive testing and validation processes, ensuring that each valve performs reliably under designated conditions before being deployed in real-world applications.
In the ever-evolving landscape of industrial technology, actuated valves continue to serve as a crucial innovation, driving efficiency and safety across myriad applications. As industries strive to enhance automation and reduce manual interference in operations, actuated valves emerge as quintessential tools. They not only ensure the seamless control of fluid dynamics but also promote the advancement of industrial standards, embodying precision and innovation in the engineering domain.
Choosing the right actuated valve is critical to achieving operational excellence. It involves an intricate balance of aligning operational requirements with the technical capabilities of the valves. As businesses increasingly leverage IoT and Industry 4.0 technologies, phase integration is crucial, paving the way for smart systems where actuated valves function as intelligent nodes within advanced process control networks. This forward-thinking approach promises to unlock new dimensions in industrial automation, heralding an era where efficiency, safety, and innovation coexist harmoniously.