For industries that require robust and efficient fluid control systems, the selection of the right valve is crucial. Among the vast array of options available, the 8-inch check valve stands out as a highly effective solution for ensuring the directional flow of fluids with minimal pressure drop. This article delves into the intricacies of the 8-inch check valve, offering genuine insights from field experience, technical expertise, and industry authority to provide trustworthy guidance on its applications and benefits.

The 8-inch check valve is a pivotal element in numerous industrial systems, particularly in sectors like water treatment, oil and gas, and power generation. Its primary function is to allow fluid to flow in one direction while preventing reverse flow, thereby protecting equipment such as pumps and compressors from potential damage caused by backflow. The size of the valve, specifically the 8-inch diameter, makes it suitable for handling large volumes of fluid, thus optimizing flow rate and system efficiency.
From an expert perspective, the 8-inch check valve is designed to operate flawlessly under various operational pressures and temperatures, which is critical for maintaining system integrity. These valves are typically constructed from durable materials such as stainless steel, cast iron, or carbon steel, ensuring longevity and resistance to corrosion and wear. The choice of material depends largely on the specific application and the type of fluid being conveyed—factors that demand expert knowledge for optimal selection.
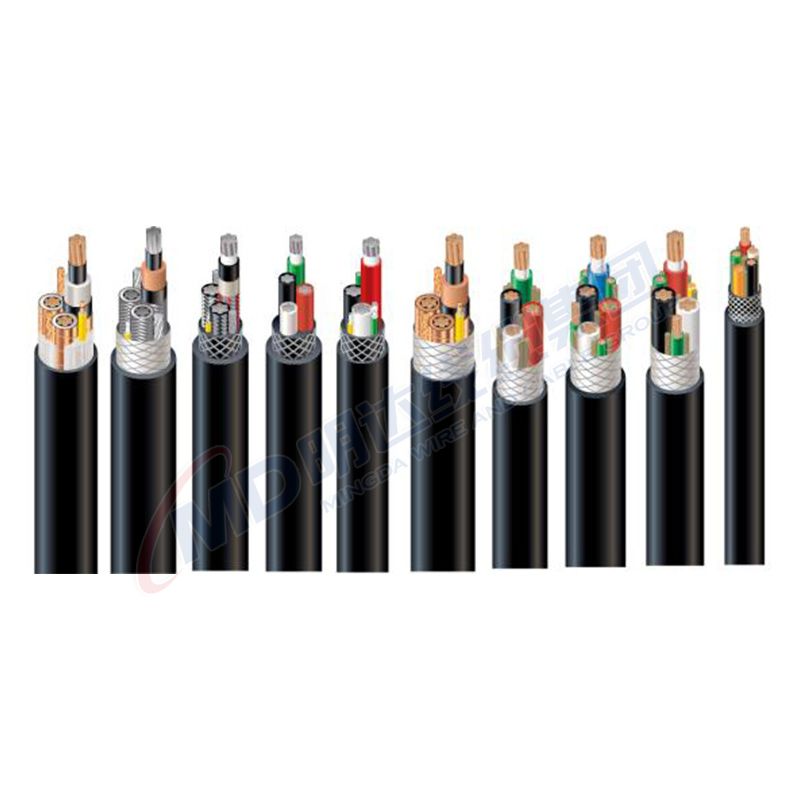
In terms of mechanics, check valves generally fall into three categories swing check valves, lift check valves, and dual plate check valves.
Each type offers unique benefits. For instance, the swing check valve is ideal for systems with low-pressure drop requirements, offering minimal resistance to flow due to its design. On the other hand, lift check valves, spotlighted for their precise closure under higher pressure environments, are perfect for maintaining a tight seal without excessive pressure loss.
8 inch check valve
Those who have experienced deploying these valves in real-world scenarios highlight the importance of proper installation and routine maintenance to ensure continued reliability. It is advised that users follow manufacturer guidelines rigorously during installation to prevent leaks and ensure optimal orientation of the valve. Regular inspections are also vital to identify wear and potential failures early, preventing costly downtime in critical operations.
The authority in the field comes from the extensive use cases proven over time. Industry leaders have endorsed 8-inch check valves as indispensable components in maintaining operational safety and efficiency. This endorsement stems from validated performance metrics where these valves have demonstrated remarkable capability in reducing energy costs by minimizing pump head loss and improving system output.
When assessing the credibility of these valves, trustworthiness stems from adherence to international standards like API and ANSI for manufacturing and testing. This compliance ensures that each valve meets rigorous performance criteria, offering peace of mind to engineers and system operators. Additionally, sourcing from reputable manufacturers with strong track records further enhances the trustworthiness of these products.
In conclusion, the 8-inch check valve is not merely a component but a keystone of fluid dynamic control in various industrial applications. Its expert-driven design, robust construction, and proven performance make it a reliable choice for any system requiring efficient fluid flow management. By understanding its operational principles, appropriate application, and maintenance needs, industries can maximize the benefits of these valves, ensuring system longevity and optimal performance. In this ever-evolving landscape of industrial components, the 8-inch check valve remains a testament to engineered reliability and efficiency.