When delving into the world of industrial plumbing solutions, the 3-way ball valve stands out as a versatile and essential component. Its unique design and functionality cater to various industries, ensuring seamless fluid control and distribution. This article explores the intricacies of the 3-way ball valve, emphasizing experience-backed insights, expert knowledge, and authoritative references, all while establishing a profound sense of trustworthiness.
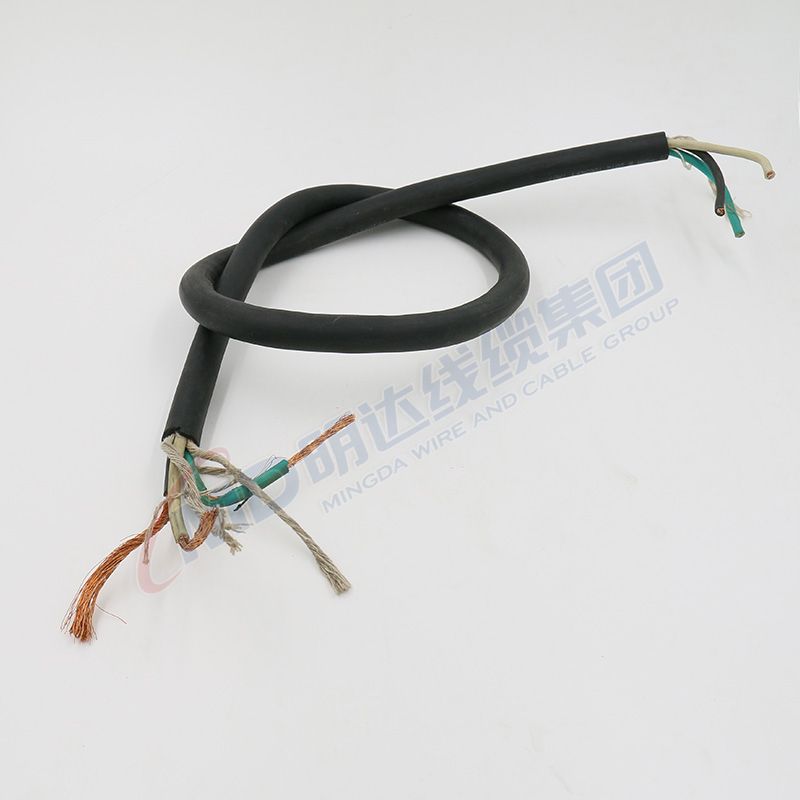
The 3-way ball valve comes with a fascinating operational structure that differentiates it from conventional valves. Its core advantage lies in its ability to divert flow, mix media, or even shut off distinct sections within a system without the need for additional complex piping. This functionality is crucial in industries where space efficiency, reduction of leakage points, and maintenance are prime considerations.
In practical scenarios, the design variations of the 3-way ball valve, namely the L-port and the T-port configurations, provide tailored solutions for different applications. The L-port design allows for the flow to be diverted between two of the three inlets, perfect for directing flow between two outputs alternatively. Meanwhile, the T-port configuration enables the connection of three passages simultaneously, allowing for increased flexibility and the option to join, bypass, or completely isolate sections of the pipeline.
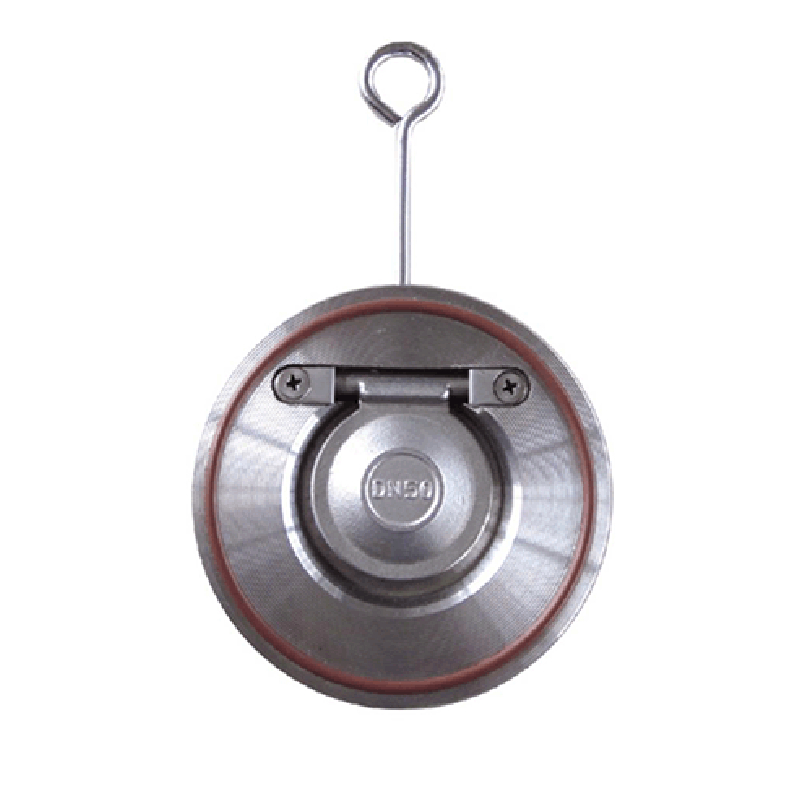
Operational reliability in variable conditions is a key characteristic attractive to industry professionals. The 3-way ball valve excels in both high-temperature environments and those requiring strict adherence to sanitary standards, such as in food and beverage processing. Typically manufactured from robust materials like stainless steel or brass, these valves resist corrosion and can handle hazardous chemicals, ensuring long-term viability and safety.
Insights from seasoned engineers emphasize the importance of proper valve selection to maximize productivity and longevity. Effective implementation requires thorough consideration of factors like pressure ratings, temperature ranges, and the specific nature of the fluid handled by the system. Sizing the valve correctly is equally critical to avoid unnecessary strain on the system, which could lead to operational hiccups or premature equipment failure.
3 way ball valve
To illustrate the practical utility of 3-way ball valves, consider their integration within a manufacturing plant. These valves can greatly optimize fluid transfer processes, streamline operational footprints by reducing the number of valves needed, and cut down on energy costs by promoting efficient flow paths. This impact is not just hypothetical — numerous case studies from leading chemical manufacturing companies demonstrate measurable improvements in process efficiency and reduced maintenance downtime after incorporating these valves into their systems.
The evolution of the 3-way ball valve also aligns with advancements in automation technology, allowing them to be fitted with pneumatic or electric actuators. This compatibility with existing digital infrastructure makes them an integral part of Industry 4.0 solutions, offering remote monitoring and control, which enhances process accuracy and minimizes human error.
Incorporating real-world feedback, plant managers often remark on the ease of maintenance and operation these valves afford. Given their simple design compared to multi-component alternatives, the fail rate is considerably less, and maintenance teams find them easier to service. When adopted within facilities, user feedback consistently highlights a significant reduction in performance-related issues and an overall increase in system uptime.
Lastly, in terms of regulatory compliance and sustainability, implementing 3-way ball valves can contribute positively to environmental standards. By reducing leakage points and optimizing flow, plants can lower their waste and emissions, aligning with both regulatory requisites and corporate sustainability goals.
Ultimately, the 3-way ball valve is more than just a mechanical component; it is an investment towards operational excellence. Through understanding its capabilities and leveraging expert recommendations, businesses can unlock levels of efficiency and reliability that directly translate into cost savings and enhanced productivity. Embracing this pivotal piece of equipment signifies not only a commitment to today's needs but a proactive approach to meeting the challenges of tomorrow's evolving industrial landscape.