In the realm of industrial piping systems, the 2-inch rubber expansion joint stands as a pivotal component, offering indispensable benefits to various sectors, including HVAC, chemical processing, and wastewater management. Recognized for its flexibility and resilience, this small yet robust device plays a crucial role in maintaining the integrity of piping setups across diverse applications. Furthermore, its essential function continues to be underscored by user experience and industry expert recommendations.

Among professionals involved in pipeline system management and maintenance, the expertise surrounding rubber expansion joints focuses significantly on the material's inherent capacity to absorb movement and vibrations. Rubber, as a material, is celebrated for its elasticity and adaptability. Over the years, industry leaders have leveraged these properties to design expansion joints that are not only effective in mitigating mechanical stress but also contribute to prolonging the lifespan of the entire piping setup.
Having delved deep into the mechanics and applications of 2-inch rubber expansion joints, experienced engineers regularly recommend these components particularly in environments where thermal expansion or contraction might otherwise jeopardize the safety and functionality of the systems. The collective experience of industry professionals highlights numerous instances where these joints have effectively prevented potential pipeline damages that could lead to costly repairs or shutdowns.
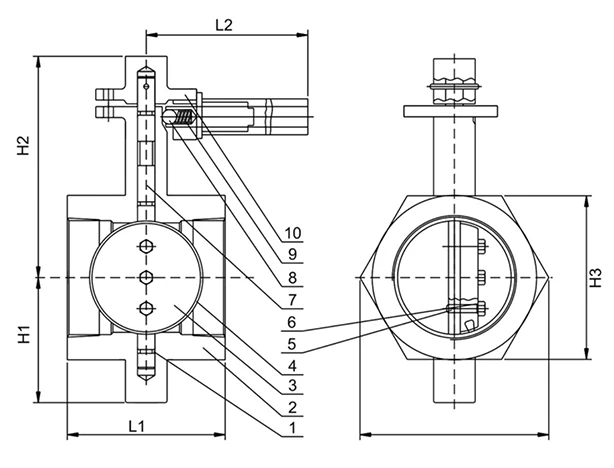
Expertise in this field unequivocally ties the success of rubber expansion joints to their capability of accommodating lateral, angular, and axial pipe movements. Given the compact size of a 2-inch joint, their installation and integration into existing systems is highly efficient and can often be completed without requiring extensive modifications to the piping structure. As specialists frequently note, this adaptability makes rubber expansion joints a preferred choice for engineers dealing with tight spaces and strict operational budgets.
2 inch rubber expansion joint
The authoritativeness of rubber expansion joints is reinforced by the robust testing and certification processes they undergo before being deemed market-worthy. Certifications from recognized industry standards such as ASTM (American Society for Testing and Materials) ensure that these joints can withstand prescribed pressure and temperature variations. This trustworthiness is vital for operators who rely on these joints to safeguard sensitive and costly machinery.
For facility managers and procurement officers, the purchase decision around rubber expansion joints typically involves evaluating several factors, including operating environments, temperature ranges, and chemical exposures. The extensive catalog of 2-inch rubber expansion joints available ensures that there are niche products tailored for specific industrial needs, whether it's resistance to abrasive materials or compatibility with high-temperature fluids. Expert advice often stipulates rigorous analysis of operational conditions to select the optimal joint, underscoring the intersection of practical experience and technical specifications in achieving desired outcomes.
For those new to sourcing rubber expansion joints, building trust in a supplier involves scrutinizing past performance, client testimonials, and after-sales support. The level of trust established between suppliers and their clients, based on consistent and reliable performance, translates into long-term relationships and ongoing business collaborations.
In summation, while the 2-inch rubber expansion joint may appear as a minor element within the larger system of industrial piping, its role is paramount in ensuring operational efficiency and safety. The culmination of practical user experiences, authoritative testing, and expert insights solidify its place as an indispensable component. By continuously innovating and adhering to stringent standards, the 2-inch rubber expansion joint not only meets but often exceeds the demanding expectations of contemporary industrial applications, establishing itself as an essential tool in the maintenance of complex piping systems.