The 2-inch ball check valve is a vital component in diverse industrial settings, offering unmatched reliability and efficiency. This crucial piece of equipment is engineered to allow fluids to flow in one direction, thereby preventing backflow and ensuring system integrity. Understanding its operational prowess, construction intricacies, and strategic applications is essential for professionals seeking to optimize fluid-handling systems.
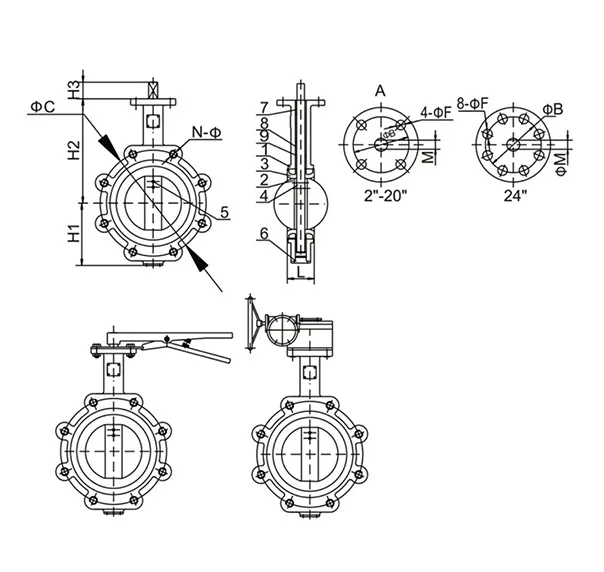
Ball check valves with a 2-inch diameter, distinguished by their spherical ball mechanism, are particularly favored in systems where maintaining a streamlined, consistent flow without backtrack is paramount. They are crafted with precision from a variety of robust materials such as stainless steel, PVC, or brass, each selected based on the specific application environment, whether it involves potable water, wastewater, slurries, or corrosive chemicals. These materials ensure that the valves can withstand significant wear and tear, chemical corrosion, and variations in pressure and temperature, thereby enhancing their longevity and performance.
A prime feature of the 2-inch ball check valve is its simplistic design, yet profound efficacy. The ball within the valve is precisely seated to impede flow in the reverse direction while allowing forward movement with minimal pressure drop. This significantly reduces the risk of fluid backflow that can compromise system functionality. In scenarios where gravity would typically cause back siphoning, especially in vertical installations, the ball acts swiftly to seal and protect the downstream components.

Expertise in selecting the right type of ball check valve is essential. The decision hinges on understanding the nuances of the fluid being handled. For instance, in sewage and wastewater industries, a nitrile-coated ball is often ideal, given its resilience to abrasive particles. Conversely, in scenarios involving higher temperatures or more aggressive chemicals, PTFE or stainless steel balls might be more suitable due to their enhanced chemical resistance and high-temperature tolerance.
2 inch ball check valve
Furthermore, the installation of the 2-inch ball check valve is crucial to its operation. It must be aligned correctly to ensure the gravitational forces or internal pressures accurately guide the ball into the seated position during reverse flow attempts. Regular maintenance checks, although minimal with these valves, can further ensure continued performance. Periodic cleaning and inspection for wear or corrosion can mitigate the risk of failures and prolong the service life of the valve.
Authoritative professionals in the field acknowledge that the choice of a 2-inch ball check valve can significantly influence not only the efficiency of a given system but also its overall operational costs. By preventing backflow effectively, these valves protect pumps and other devices from potential damage, thereby lowering repair costs and reducing downtime. In large-scale industrial operations, the economic impact of reduced wear on expensive machinery cannot be overstated.
Trust in the 2-inch ball check valve derives from its proven history and reliability across industries. From water treatment plants to chemical manufacturing, its application breadth is vast. Engineers and system designers continually turn to these valves for their predictable, low-maintenance operation that ensures safety and efficiency. It is not merely a component but an assurance of regulatory compliance, operational smoothness, and environmental responsibility.
In conclusion, the 2-inch ball check valve stands out as a paragon of fluid control engineering. Its deceptively simple design masks a complexity of function that is indispensable to the modern industrial tapestry. By selecting and utilizing these valves with a well-informed understanding of their properties and potential applications, industry professionals can unlock unparalleled system efficiency and reliability. Investing in the right valve not only safeguards operations but also underpins the foundational trust in industries that rely on precise fluid management.