In the world of fluid control systems, the 12-inch butterfly valve stands out for its versatility and efficiency in various industrial applications. Whether it's used in water treatment, oil and gas, or chemical processing, this component offers a robust solution for regulating flow and ensuring seamless operations. Here, we dive deep into the specifics of the 12-inch butterfly valve, illuminating its features, advantages, and the incredible role it plays in modern engineering practices.
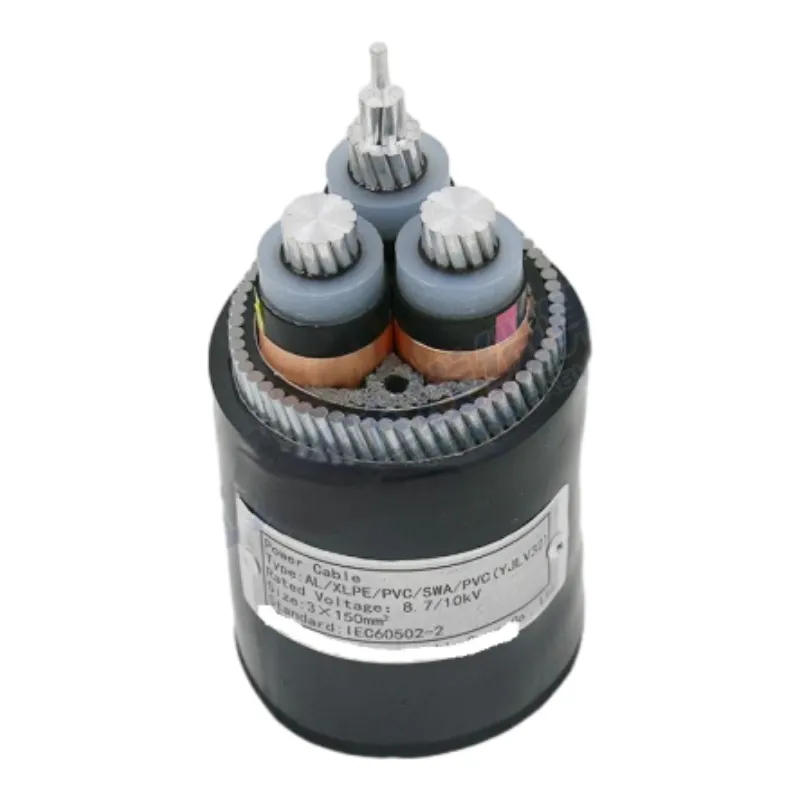
Crafted for reliability, the 12-inch butterfly valve is intricately designed to maintain control over the flow of liquids or gases. Its impressive diameter is particularly suitable for large-scale systems, offering the ability to manage substantial volumes with minimal effort. This valve operates with a disc that pivots on a central axis, allowing for quick shut-off and reduced pressure loss, an aspect that enhances energy efficiency across systems.
Engineers and industry experts favor the butterfly valve for several critical reasons. First, its streamlined construction—often comprising a body, disc, stem, and seat—ensures minimal maintenance. The valve's simplicity translates into fewer components that could potentially fail, offering a longer lifespan and reduced downtime for maintenance. Additionally, the compact design of the 12-inch butterfly valve means it occupies less space compared to other valve types, making it ideal for environments where space is at a premium.

In terms of material construction, the valve is available in a variety of durable options, including stainless steel, ductile iron, and polyvinyl chloride (PVC), each chosen based on the specific demands of the application. For instance, stainless steel provides excellent resistance to corrosion and extreme temperatures, making it a preferred choice in harsh environments. This adaptability to different conditions highlights the valve's expertise across varied industries.
Installation flexibility adds another layer of desirability to the 12-inch butterfly valve. It can be integrated into existing systems with relative ease, whether it's a lug type or wafer type configuration, allowing for hassle-free retrofitting into established pipelines. The alignment and realignment of these valves during installation or replacement contribute significantly to saving time and labor costs, factors that directly influence the bottom line in large industrial settings.
12 inch butterfly valve
Certification and compliance are key when discussing valves, contributing to their trustworthiness in the field. Leading manufacturers ensure that 12-inch butterfly valves conform to international standards, such as the American Society of Mechanical Engineers (ASME) and International Organization for Standardization (ISO). This compliance guarantees that users receive high-quality products that meet stringent safety and performance criteria.
In practical application,
the authority of the 12-inch butterfly valve is evident. Take the water treatment industry, for instance, where these valves regulate the flow of both raw and treated water with precision. Here, their ability to manage high-pressure systems efficiently without compromising on flow control is paramount. Similarly, in the oil and gas sector, the ability to handle diverse media, from crude oil to more volatile substances, underscores their indispensable role.
Moreover, the future of 12-inch butterfly valves points towards smart innovations. With advancements in automation and monitoring, these valves are increasingly being integrated with sensors and actuators. Such enhancements allow for real-time monitoring and remote operation, marking a shift towards more intelligent and responsive fluid management systems. This evolution not only increases operational efficiency but also boosts the safety and sustainability of industrial practices.
In conclusion, the 12-inch butterfly valve emerges as an exemplar of engineering prowess—combining experience-driven design, professional-grade construction, authoritative reliability, and trusted performance across industries. As technology continues to advance, these valves will likely sustain their pivotal role in optimizing fluid control systems around the globe, underpinning the delicate balance between innovative engineering and practical utility.